Chemical Treatment in Cooling Towers
Cooling towers are essential components in various industrial processes, power plants, and HVAC systems, where they play a critical role in dissipating heat and improving operational efficiency. However, like any system that manages large volumes of water, cooling towers are susceptible to problems such as scale buildup, corrosion, and biological growth. To mitigate these issues, effective chemical treatment is necessary. This article explores the significance of chemical treatment in cooling towers, the types of chemicals used, and best practices for maintenance.
Importance of Chemical Treatment
The primary goal of chemical treatment in cooling towers is to maintain water quality and ensure the efficiency of the cooling system. The untreated water in cooling towers can lead to the formation of scale, which is primarily composed of calcium carbonate and other minerals. Scale buildup can severely impair heat exchange efficiency, leading to increased energy consumption and reduced overall performance.
Corrosion is another significant issue that can arise in cooling systems, primarily due to the presence of dissolved oxygen and low pH levels. Corrosion not only damages the cooling tower components, including pipes and heat exchangers, but can also lead to costly repairs and downtime. Moreover, the presence of algae, bacteria, and other microorganisms can result in harmful biofilms, reducing the system's efficiency and potentially contaminating the water supply.
Types of Chemicals Used
Chemical treatment in cooling towers typically involves several categories of chemicals
1. Scale Inhibitors These chemicals prevent scale formation by modifying the crystallization process of minerals in the water. Common scale inhibitors include phosphonates and polyacrylic acids, which help to keep calcium, magnesium, and other minerals in solution.
2. Corrosion Inhibitors To protect against corrosion, a variety of inhibitors can be applied, including film-forming amines, phosphate compounds, and molybdate. These chemicals create a protective layer on the metal surfaces, reducing the direct contact with corrosive agents.
chemical treatment in cooling tower
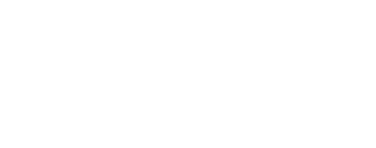
3. Biocides To control microbial growth, various biocides are introduced into the cooling water. These can be chlorine-based, bromine-based, or non-oxidizing biocides. Proper use of biocides is crucial to prevent the proliferation of harmful bacteria and algae, which can lead to biofouling.
4. pH Control Agents Maintaining optimal pH levels is important for both corrosion control and scale prevention. pH control agents, such as sodium hydroxide or sulfuric acid, may be used to adjust the water's acidity or alkalinity, fostering an environment less conducive to corrosion and scale formation.
Best Practices for Chemical Treatment
To ensure the effectiveness of chemical treatment in cooling towers, several best practices should be followed
- Regular Monitoring Continuous monitoring of water chemistry is essential. Parameters such as conductivity, pH, and microorganism levels should be regularly checked to assess the need for chemical adjustments.
- Proper Dosing Chemicals should be added in precise amounts based on water analysis. Over-dosing can lead to adverse effects, including increased chemical costs and potential harm to the cooling system.
- System Cleaning Periodic cleaning of cooling towers and associated components should be implemented to remove scale, biofilms, and other contaminants, thereby enhancing system efficiency.
- Professional Consultation Engaging with water treatment professionals can provide valuable insights and recommendations tailored to specific cooling system requirements, ensuring compliance with industry regulations and optimizing water treatment protocols.
In conclusion, the chemical treatment of cooling towers is a vital aspect of maintaining operational efficiency, preventing system failures, and ensuring environmental compliance. By understanding the importance of chemical treatment and adhering to best practices, facilities can achieve significant long-term benefits and sustainability in their cooling operations.