Mineral Fillers for Plastics Enhancing Properties and Performance
Mineral fillers have become an integral part of the plastics industry, serving as additives that improve the properties of plastic materials. These fillers are naturally occurring or processed mineral substances that are incorporated into plastic formulations during the compounding process. Their inclusion can significantly modify the physical characteristics of plastics, such as strength, rigidity, thermal stability, and cost-effectiveness.
Types of Mineral Fillers
There are various types of mineral fillers commonly used in plastic production, each offering unique benefits
1. Calcium Carbonate This is one of the most widely used fillers in plastics. It is valued for its ability to enhance rigidity and decrease production costs. Calcium carbonate can be used in various applications, including packaging, pipes, and automotive components. It also improves the surface finish of the final product.
2. Talcm Known for its excellent dispersibility and high strength-to-weight ratio, talc is often used to improve the impact resistance and thermal stability of plastics. It is common in automotive and consumer goods applications.
3. Clay Adding clay to plastics can enhance mechanical properties and improve barrier performance. Clay filler can also contribute to flame retardancy when used in specific formulations, making it suitable for electrical and electronic applications.
4. Barytes (Barium Sulfate) This mineral filler provides a high specific gravity, which is advantageous for certain types of industrial plastics. Barytes also improve the opacity of opaque plastics, making it ideal for applications requiring these properties.
5. Silica Used as a reinforcing filler, silica improves the tensile strength and durability of plastics. It is frequently found in tire manufacturing and other applications requiring high-performance materials.
mineral fillers for plastics
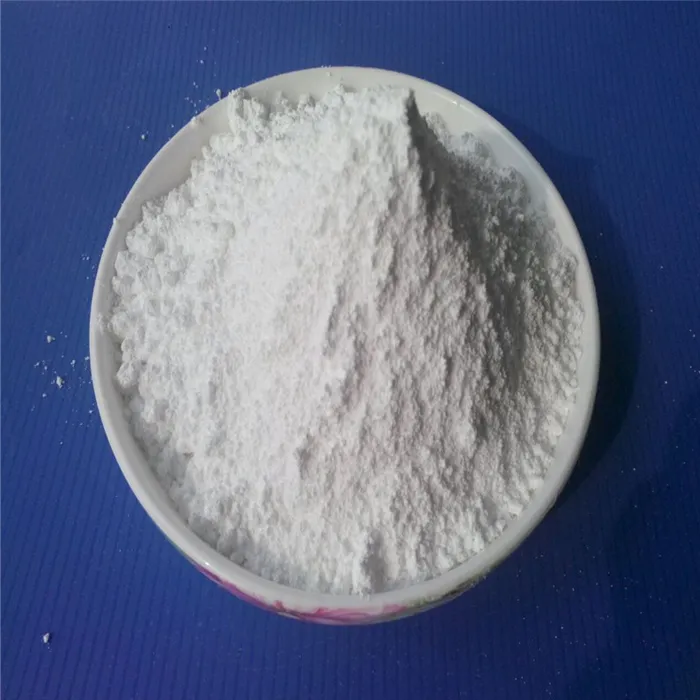
Benefits of Using Mineral Fillers
The incorporation of mineral fillers into plastics confers numerous advantages
- Cost Reduction Mineral fillers are generally less expensive than polymers, allowing manufacturers to reduce production costs without compromising the performance of the plastic. This is particularly beneficial in high-volume applications where cost efficiency is crucial.
- Enhanced Mechanical Properties Fillers contribute to improved stiffness and strength, making the final products more durable and wear-resistant. This is important in applications where the physical integrity of the plastic is critical.
- Lightweight Alternatives Many mineral fillers are lightweight, enabling the production of plastics that are both strong and light. This is particularly advantageous in sectors like automotive and aerospace, where weight reduction is often a priority.
- Improved Processing Certain fillers can enhance the flow characteristics of plastics during processing, making it easier to work with. They can influence how the material behaves during molding or extruding, promoting more efficient production processes.
- Environmental Benefits The use of mineral fillers can aid in the development of more sustainable plastic products. By reducing the amount of polymer needed, manufacturers can create lighter-weight products that may lead to lower carbon footprints during transport and use.
Conclusion
The role of mineral fillers in the plastics industry cannot be overstated. They not only enhance the physical properties of plastics but also contribute to cost-effectiveness and improved processability. As industries continue to seek better performance and sustainability, the demand for mineral fillers is expected to grow, leading to innovations in formulations and applications. Researchers and manufacturers are continuously exploring new types of fillers and their potential roles in developing advanced plastic materials that meet the evolving demands of various markets. The future of plastics looks promising with mineral fillers at the forefront, driving enhancements in both performance and environmental responsibility.