Laser Marking Additives for Plastics Enhancing Marking Efficiency and Quality
In the modern manufacturing landscape, where branding and product identification are paramount, laser marking has emerged as an essential technique for marking plastics. This method utilizes concentrated beams of light, or lasers, to engrave or mark surfaces, offering precision and durability. However, to optimize the effectiveness of laser marking on plastics, the incorporation of laser marking additives is becoming increasingly important.
Laser Marking Additives for Plastics Enhancing Marking Efficiency and Quality
Colorants are perhaps the most common form of additives used in laser marking. These can include pigments that change color when exposed to the laser's heat. For instance, a black pigment might lighten to create a contrasting mark on a lighter-colored plastic surface, thus enhancing readability. This color transformation is vital for applications such as product labeling and traceability, where clarity is crucial for compliance with industry standards.
laser marking additives for plastics
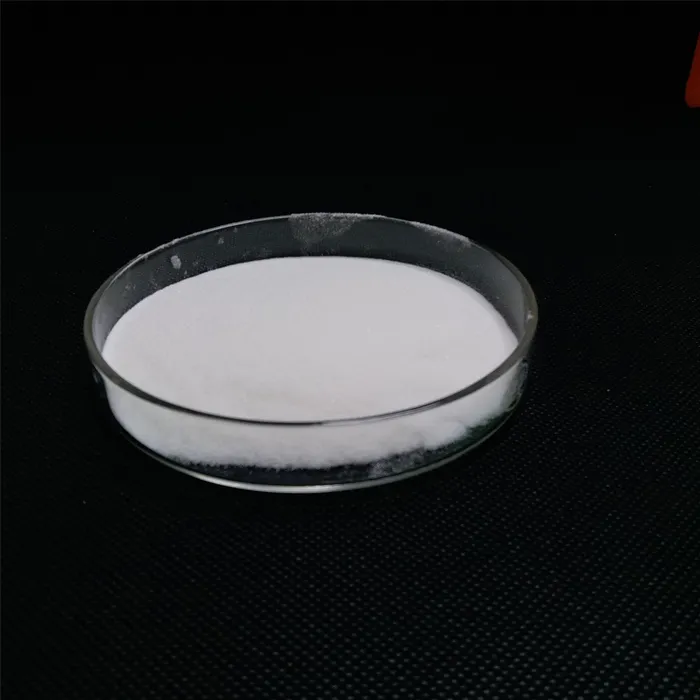
Foaming agents, on the other hand, create a three-dimensional effect during the marking process. When struck by the laser, these additives expand and produce a raised surface, which not only contributes to the aesthetic appeal of the marked area but also increases its durability. These raised marks are less susceptible to wear and tear, making them ideal for products that experience rough handling or environmental stress.
The choice of additive depends on various factors, including the type of plastic being used, the desired mark quality, and the application environment. For example, high-performance polymers like polycarbonate and acrylonitrile butadiene styrene (ABS) may require specific additives to achieve optimal results. Manufacturers must also consider the regulatory implications of the materials used in producing the final product, ensuring that they are compliant with safety standards.
Moreover, advancements in laser technologies have led to the development of more efficient marking systems that work seamlessly with these additives. As the demand for high-quality, durable markings on plastics continues to rise, the role of laser marking additives is expected to grow. They represent a crucial bridge between conventional manufacturing processes and modern laser technology, facilitating enhanced branding, traceability, and consumer safety in an increasingly competitive market.
In conclusion, laser marking additives are vital components in the quest for effective plastic marking solutions. By enhancing contrast and durability, these additives not only improve the aesthetic qualities of products but also contribute to better identification and compliance. The continued evolution of these technologies will undoubtedly lead to even more innovative applications in the future, reshaping the landscape of manufacturing and product design.