Chiller Water Treatment Chemicals Ensuring Efficiency and Longevity in Cooling Systems
In modern industrial and commercial buildings, chiller systems are pivotal for maintaining optimal conditions, especially in larger environments. These systems play a crucial role in refrigeration and air conditioning, providing the necessary cooling to keep operations running smoothly. However, like all mechanical systems, chillers require regular maintenance to ensure not just optimal performance but also longevity. One of the key components of this maintenance is the treatment of chiller water, which often involves the use of various chemicals.
Chiller water treatment is essential for preventing common issues such as scale formation, corrosion, and biological growth within the cooling system. Each of these problems can significantly affect the efficiency and lifespan of the machinery. Therefore, the application of appropriate treatment chemicals can help mitigate these risks.
Scale Formation
One of the main challenges in chiller systems is scale formation, especially in regions with hard water. When minerals such as calcium and magnesium come into contact with the heat exchange surfaces, they can precipitate out of the water, leading to scale buildup. This scale acts as an insulator, reducing the efficiency of heat transfer and increasing energy consumption. To combat this, scale inhibitors, which are typically phosphonates or polymers, are added to the chiller water. These chemicals work by sequestering calcium and magnesium ions, thus preventing them from crystallizing and depositing on surfaces.
Corrosion Control
Corrosion is another significant concern in chiller systems, particularly those made of metals such as copper, steel, and aluminum. The use of untreated or improperly treated water can lead to rust and pitting, ultimately causing leaks and mechanical failure. To address this issue, chemical corrosion inhibitors are employed. These chemicals often include azoles, amines, and phosphates, which form a protective film on the metal surface, significantly reducing the rate of corrosion. Regular monitoring of water chemistry and appropriate dosing of these inhibitors are crucial for maintaining the integrity of the cooling system.
chiller water treatment chemicals
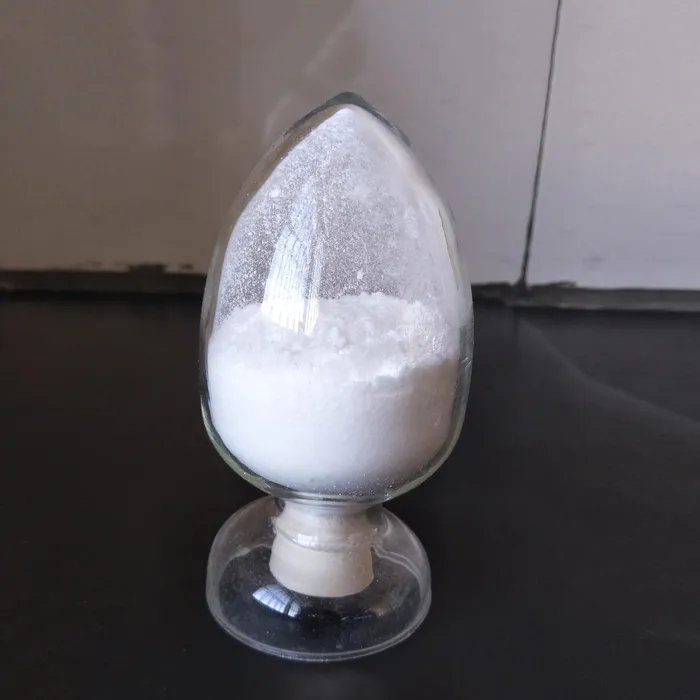
Biological Growth Management
Chiller systems, especially those using open cooling towers, are susceptible to biological growth such as algae, bacteria, and other microorganisms. The growth of these organisms can lead to biofilm formation, which further contributes to fouling and can even introduce health risks due to pathogens like Legionella. To mitigate biological growth, biocides such as chlorine, bromine, or non-oxidizing biocides are commonly used. These chemicals effectively control microbial populations and ensure that the cooling system remains hygienic and efficient.
Environmental Considerations
While the importance of chiller water treatment chemicals is clear, so too is the need for environmental responsibility. Many chemical treatments can have negative effects on groundwater and aquatic ecosystems if not handled correctly. Industry standards and regulations increasingly require the use of environmentally friendly alternatives wherever possible. This has led to the development of advanced treatment programs that focus on minimizing chemical usage while maximizing efficacy through improved system monitoring and control technology.
Conclusion
In conclusion, the effectiveness and longevity of chiller systems significantly rely on proper water treatment. By utilizing a combination of scale inhibitors, corrosion mitigators, and biocides, facility managers can ensure that their cooling systems operate at optimal efficiency while extending their service life. As environmental concerns continue to rise, the trend towards more sustainable and eco-friendly treatment solutions will likely shape the future of chiller water management, ultimately leading to improved performance and decreased ecological impact. Investing in the right water treatment strategies not only safeguards the equipment but also contributes to operational efficiency and cost savings.