Chemicals Used in Boiler Feed Water Ensuring Efficiency and Safety in Steam Generation
Boilers are essential components in many industrial processes, providing steam for heat and power generation. To ensure the efficient operation of a boiler, the quality of the feed water is critical. Contaminants present in untreated water can lead to scale formation, corrosion, and a host of operational issues. As a result, various chemicals are employed to treat boiler feed water, enhancing its quality and ensuring optimal performance.
Understanding Boiler Feed Water Treatment
Boiler feed water treatment is the process of reducing or eliminating contaminants in the water to ensure its suitability for steam generation. The primary concerns regarding water quality include hardness, dissolved oxygen, and the presence of impurities such as alkalinity and silica. Consequently, specific chemicals are used to combat these issues and maintain water quality.
1. Oxygen Scavengers Preventing Corrosion
Dissolved oxygen in boiler feed water is a significant contributor to corrosion in boiler systems. Oxygen scavengers, such as sodium sulfite and hydrazine, are common chemicals added to boiler feed water to eliminate oxygen. These compounds react with oxygen to form non-corrosive by-products, thereby preventing corrosion of metal components in the boiler system. Regular monitoring of dissolved oxygen levels is essential to optimize the dosage of oxygen scavengers and maintain the integrity of the boiler.
2. Scale Inhibitors Controlling Hardness
Hardness in water is primarily due to the presence of calcium and magnesium ions. When heated, these minerals can precipitate to form scale on the boiler's heating surfaces, reducing efficiency and leading to potential failures. Scale inhibitors, including phosphonates and polyacrylic acids, are often used in water treatment processes. These chemicals act by interfering with the crystallization process of calcium and magnesium salts, thus preventing scale formation. Proper dosage and monitoring are vital to ensure that these inhibitors remain effective in maintaining water quality.
chemicals used in boiler feed water
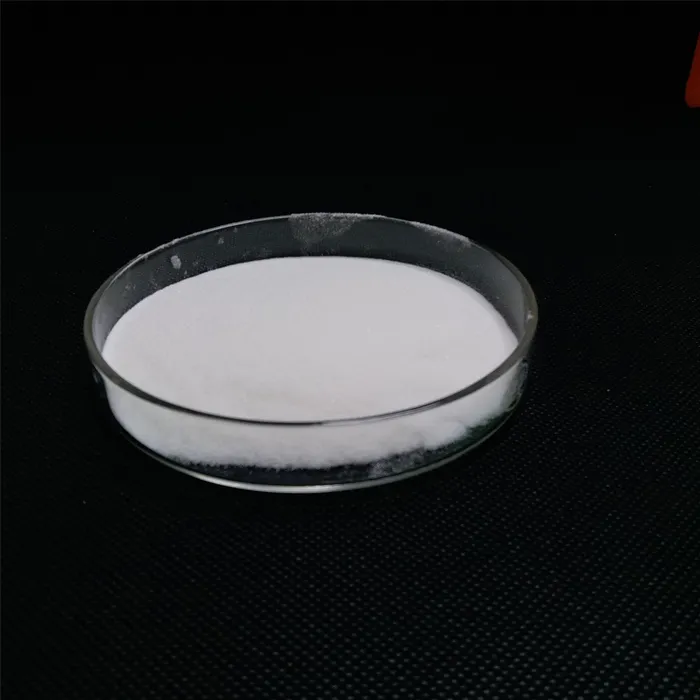
3. pH Control Agents Optimizing Alkalinity
The pH level of boiler water has a direct impact on its corrosion potential and scaling tendencies. Maintaining an optimal pH range (usually between 10.5 and 11.5) is crucial for minimizing corrosion and maintaining the stability of the feed water chemistry. Chemicals such as sodium hydroxide or sodium carbonate are used to adjust the pH of boiler feed water. By carefully controlling the pH, operators can achieve a stable environment that minimizes the risk of corrosion and scaling.
4. Corrosion Inhibitors Protecting Metal Surfaces
In addition to oxygen scavengers, specialized corrosion inhibitors are utilized to protect the metal surfaces within the boiler. These inhibitors, such as film-forming amines and molybdate compounds, form a protective layer on the metal surfaces, reducing the rate of corrosion even in the presence of potential corrosive agents. The application of corrosion inhibitors is essential in maintaining the longevity and efficiency of boiler systems, especially in high-stress environments.
5. Aldehyde-Based Biocides Controlling Microbial Growth
Microbial growth in boiler systems can lead to biofouling, which severely impacts efficiency and operational reliability. Aldehyde-based biocides, such as glutaraldehyde, are used to control microbial populations in the feed water. Regular treatment ensures that biofilms do not form, thus preserving the integrity of the boiler’s operation.
Conclusion
The use of chemicals in boiler feed water treatment is an essential practice to ensure the efficient and safe operation of boiler systems in various industries. By employing oxygen scavengers, scale inhibitors, pH control agents, corrosion inhibitors, and biocides, operators can maintain high water quality, maximizing energy efficiency and minimizing maintenance costs. With ongoing advancements in chemical treatment technologies, industries can continue to enhance the performance and longevity of their boiler systems, leading to safer and more efficient operations. Understanding the role of these chemicals is vital for engineers and operators alike, ensuring that they can make informed decisions for optimal boiler operation.