- Introduction to Dosing Systems in Water Treatment
- Innovative Technologies Driving Efficiency
- Performance Comparison of Leading Manufacturers
- Tailored Solutions for Diverse Applications
- Real-World Case Studies Across Industries
- Best Practices for Maintenance and Calibration
- Future Trends in Chemical Dosing Systems
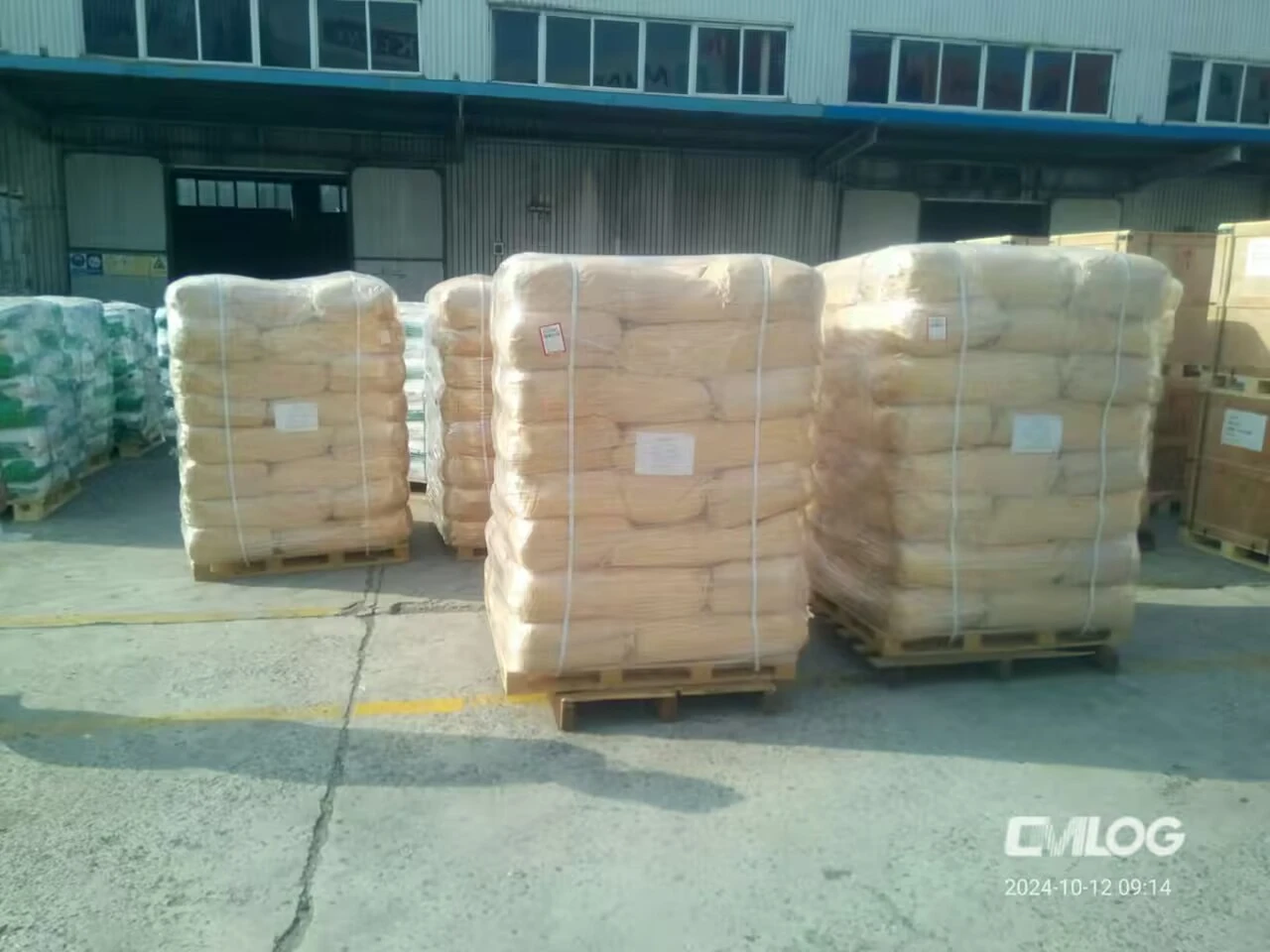
(dosing system in water treatment plant)
Understanding the Role of Dosing Systems in Water Treatment
Dosing systems are critical components in water treatment plants, ensuring precise chemical delivery for processes like coagulation, disinfection, and pH adjustment. Modern facilities handle flows ranging from 50 m³/day to 500,000 m³/day, requiring dosing accuracy within ±1.5% to meet EPA and WHO standards. These systems optimize chemical consumption, reducing operational costs by 18-22% compared to manual dosing methods.
Innovative Technologies Driving Efficiency
Advanced dosing systems now integrate IoT-enabled sensors and predictive algorithms. Key technological breakthroughs include:
- Automated viscosity compensation for chemical mixtures
- Real-time TOC (Total Organic Carbon) monitoring integration
- Self-cleaning peristaltic pumps with 20,000-hour lifespans
Performance Comparison of Leading Manufacturers
Brand | Flow Range (L/h) | Accuracy | Control Method | Maintenance Cycle |
---|---|---|---|---|
Brand A | 2-2,500 | ±0.8% | PID + AI | 18 months |
Brand B | 5-3,000 | ±1.2% | PLC Control | 12 months |
Tailored Solutions for Diverse Applications
Customization parameters for chilled water and wastewater systems vary significantly:
- Municipal Plants: 3-5 chemical injection points with flow rates exceeding 800 L/h
- HVAC Systems: Compact units (1.2m x 0.8m footprint) handling glycol mixtures
- Industrial Cooling: Corrosion-resistant materials for chlorine dioxide dosing
Real-World Case Studies Across Industries
A semiconductor factory reduced scaling incidents by 94% after implementing a multi-stage dosing system. The solution included:
- Dual redundant pumps for continuous operation
- Integrated SCADA system with <1s response time
- Annual chemical savings: $48,700
Best Practices for Maintenance and Calibration
Proactive maintenance extends equipment lifespan by 40-60%. Critical protocols include:
- Biweekly sensor calibration using NIST-traceable references
- Quarterly pump diaphragm inspections
- Annual full-system performance validation
Future Trends in Chemical Dosing Systems for Water Treatment
The global chemical dosing system market is projected to grow at 6.8% CAGR through 2030, driven by smart water infrastructure demands. Emerging innovations focus on:
- Nanotechnology-based dosing actuators
- Blockchain-powered chemical inventory tracking
- AI-driven predictive contamination response systems
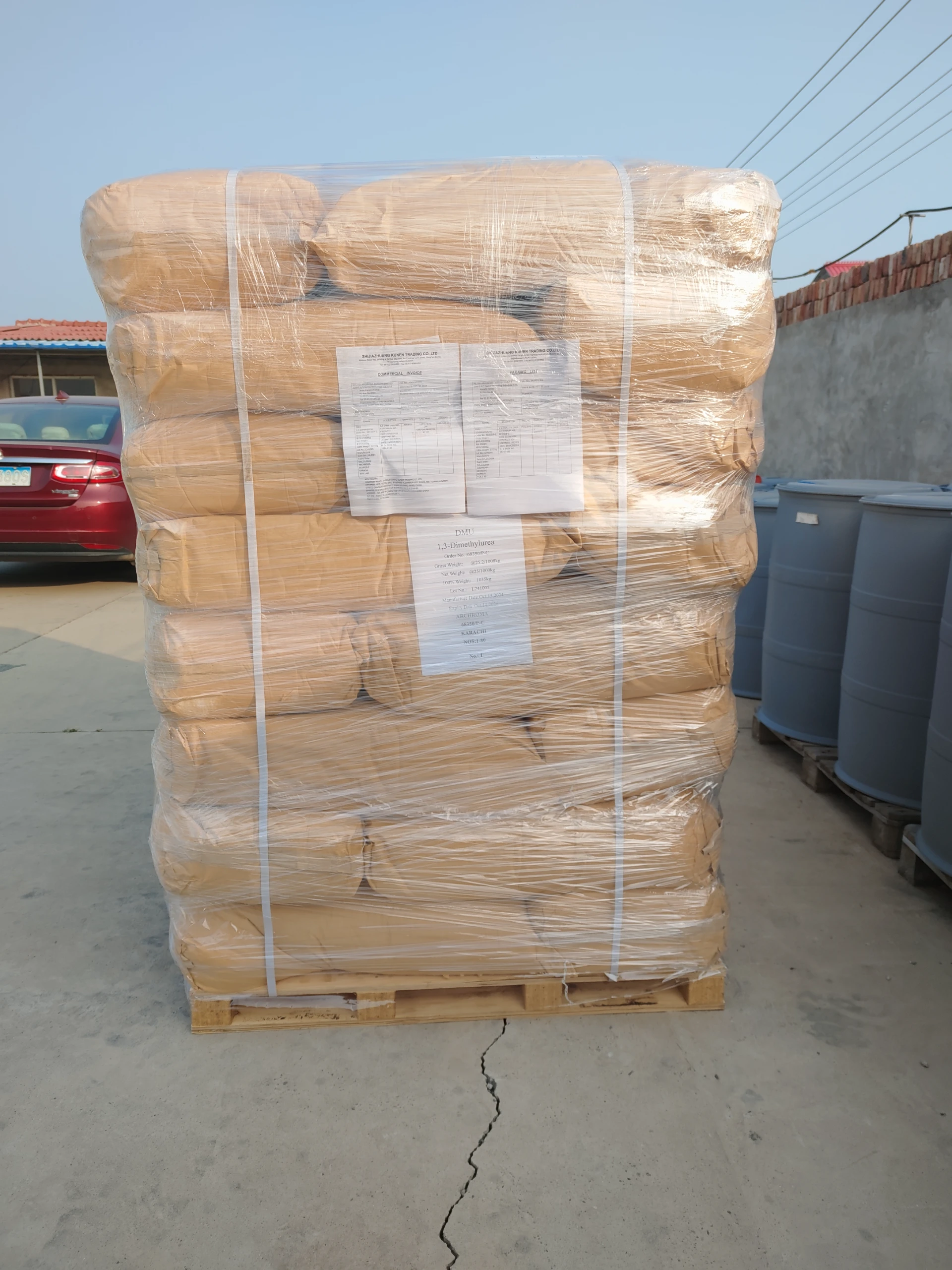
(dosing system in water treatment plant)
FAQS on dosing system in water treatment plant
Q: What is the primary purpose of a dosing system in a water treatment plant?
A: The dosing system accurately injects chemicals (e.g., chlorine, coagulants) into water to treat contaminants, balance pH, or prevent corrosion. It ensures precise control for safe and efficient water quality management.
Q: How does a chemical dosing system improve water treatment processes?
A: It automates chemical delivery to neutralize harmful substances, reduce scaling, and kill pathogens. This enhances treatment consistency while minimizing manual intervention and chemical waste.
Q: What components are critical in a chemical dosing system for water treatment?
A: Key components include storage tanks, pumps, injectors, sensors, and controllers. Sensors monitor parameters like pH or turbidity, triggering pumps to adjust dosing rates dynamically.
Q: Why is chemical dosing important in chilled water systems?
A: It prevents microbial growth, corrosion, and scaling in pipes and equipment. Proper dosing maintains system efficiency and extends the lifespan of chilled water infrastructure.
Q: How is maintenance handled for dosing systems in water treatment plants?
A: Regular calibration of pumps, inspection of chemical lines, and sensor validation are essential. Automated alerts and routine checks help prevent downtime and ensure accurate dosing.