The Role of Stabilizers in Plastics Ensuring Durability and Performance
Plastics have become an integral part of modern life, finding applications across a vast array of industries, from packaging and automotive to electronics and healthcare. However, the durability and performance of plastic materials can be significantly impacted by environmental factors such as UV radiation, heat, and oxidative conditions. To combat these issues, stabilizers are added to plastic formulations, enhancing their longevity and ensuring that they maintain their desired properties throughout their service life.
Stabilizers play a crucial role in modifying the physical and chemical properties of plastics. They are primarily employed to protect against degradation caused by exposure to ultraviolet (UV) radiation, heat, and various chemicals. The addition of these stabilizers not only extends the lifespan of plastic products but also improves their aesthetic qualities, mechanical strength, and overall performance.
The Role of Stabilizers in Plastics Ensuring Durability and Performance
Another critical category of stabilizers is thermal stabilizers. High temperatures during processing or in end-use applications can lead to thermal degradation, impacting the polymer chains and compromising the material's integrity. Thermal stabilizers are often used in the production of polyvinyl chloride (PVC) and polycarbonate, ensuring that these materials remain stable and retain their mechanical properties even when subjected to high heat. Without these stabilizers, manufacturers would face significant challenges in producing plastics that could withstand elevated temperatures without degrading.
stabilizer in plastic
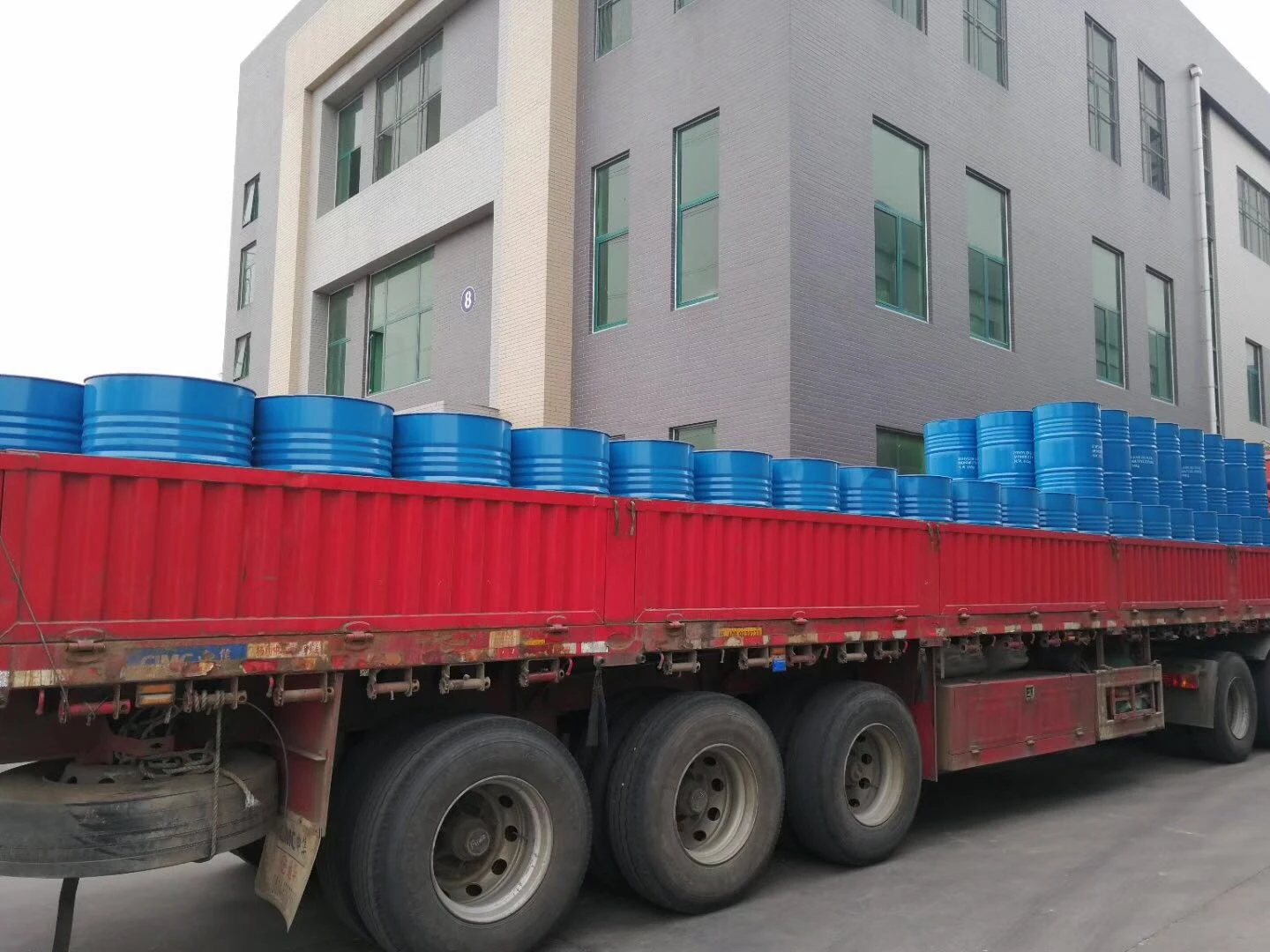
Antioxidants are also a key component in stabilizing plastics. These additives prevent oxidative degradation, a process that can occur when plastics are exposed to heat, air, or light. Oxidative degradation can lead to discoloration, loss of mechanical properties, and ultimately, material failure. By incorporating antioxidants into plastic formulations, manufacturers can significantly enhance the material's resistance to aging, ensuring a longer service life and better performance in various environmental conditions.
Beyond degradation resistance, stabilizers also contribute to improving the processing characteristics of plastics. For instance, some additives facilitate better flow properties during injection molding or extrusion, allowing for more efficient manufacturing processes. This can lead to reduced production times and higher quality finished products.
It's important to consider the environmental impact of stabilizers in plastics, particularly concerning their potential toxicity and effects on human health. As regulatory standards become increasingly stringent, manufacturers are seeking safer alternatives while maintaining the efficacy of their products. Biodegradable stabilizers and those derived from renewable resources are gaining traction as viable options that meet safety and environmental criteria.
In conclusion, stabilizers are fundamental to enhancing the durability, performance, and appearance of plastic materials. As the demand for high-performance plastics continues to grow, so too does the importance of effective stabilization technologies. These additives not only extend the life of plastic products, making them more sustainable, but they also ensure that manufacturers can produce high-quality, reliable plastics that meet the needs of consumers and industries alike. With ongoing advancements in stabilization technology, the future of plastics looks promising, paving the way for innovations that will benefit both manufacturers and end-users.