Chemical Foaming Agents for Plastics An Overview
Chemical foaming agents (CFAs) play a crucial role in the plastics industry, where they are used to produce lightweight materials with improved physical properties. These agents are substances that release gas upon decomposition, creating a foam structure within the polymer matrix. The use of CFAs offers several advantages, including reduced weight, enhanced insulation properties, and increased processing efficiency.
Types of Chemical Foaming Agents
CFAs are typically categorized into two main types endothermic and exothermic agents.
1. Endothermic Foaming Agents These agents absorb heat and decompose at elevated temperatures, releasing gases such as nitrogen and carbon dioxide. Common examples include azodicarbonamide and sodium bicarbonate. The endothermic reaction is beneficial as it helps in controlling the temperature of the polymer during processing, thereby minimizing thermal degradation.
2. Exothermic Foaming Agents In contrast, exothermic agents release heat along with gas, which leads to rapid foam formation. They include compounds such as calcium carbonate and ammonium bicarbonate. These agents are effective in applications where quick foam generation is required, such as in the production of lightweight structural components.
Benefits of Using Chemical Foaming Agents
The integration of CFAs into plastic processing yields numerous advantages
- Weight Reduction One of the primary benefits of using CFAs is the significant reduction in density, which leads to lighter products. This feature is particularly important in industries such as automotive and aerospace, where weight savings can enhance fuel efficiency and reduce emissions.
- Enhanced Insulation Properties The foam structure formed by CFAs provides excellent thermal insulation, making it ideal for applications needing thermal management
. This is especially advantageous in building materials and packaging, where maintaining temperature control is crucial.- Improved Mechanical Properties CFAs can enhance the mechanical properties of plastic products, such as impact resistance and tensile strength. The closed-cell foam structure provides better support under stress, which is vital for many engineering applications.
chemical foaming agents for plastics
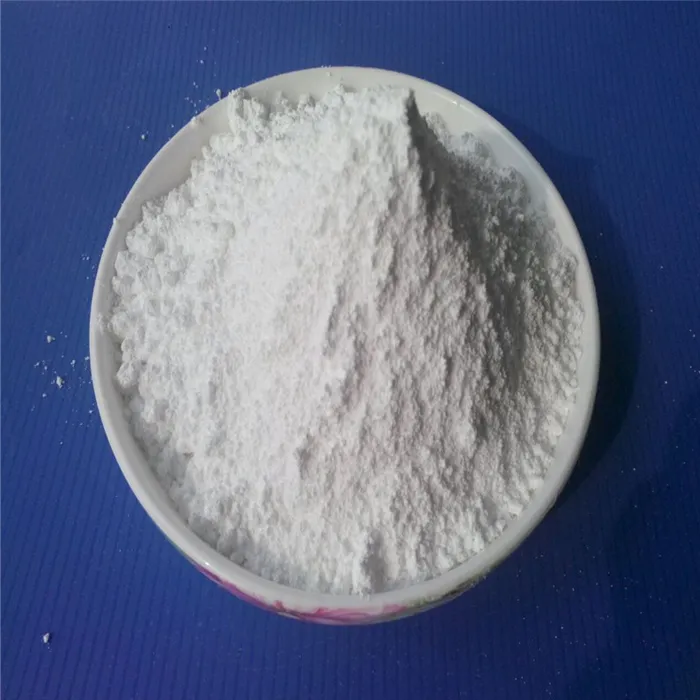
- Cost-Effectiveness By reducing the amount of raw material needed for production, CFAs can contribute to overall cost savings. Less material not only lowers production costs but also reduces the environmental impact associated with material extraction and processing.
Applications of Chemical Foaming Agents
CFAs are utilized across a wide range of industries and applications
- Automotive In the automotive sector, CFAs are used for manufacturing lightweight components such as dashboards, door panels, and bumpers, contributing to overall vehicle efficiency and performance.
- Packaging CFAs are widely used in packaging materials to create protective cushioning that helps prevent damage during transportation while minimizing material usage.
- Construction Insulative foams produced with CFAs are crucial in the construction industry, where they provide energy efficiency in building designs by reducing heat loss.
Challenges and Considerations
Despite their advantages, there are challenges associated with the use of CFAs. For instance, the selection of the appropriate CFA is vital, as it can influence the final properties of the plastic. Factors like processing temperature, compatibility with the polymer, and the desired density must be carefully considered. Moreover, ensuring uniform distribution of the foaming agent within the polymer matrix is essential to achieving consistent results.
Conclusion
In conclusion, chemical foaming agents are indispensable in the plastics industry, facilitating the creation of lightweight, insulative, and mechanically robust products. Their diverse applications across various sectors underscore their significance in enhancing product performance and achieving sustainability goals. As technology advances and the demand for innovative materials grows, the development and optimization of CFAs will undoubtedly continue to evolve, paving the way for more efficient and eco-friendly solutions.