The Role of Chemicals in Cooling Water Systems An Overview
The management of cooling water systems is a critical aspect of industrial operations, especially in facilities such as power plants, refineries, and manufacturing plants. These systems play a vital role in maintaining operational efficiency and equipment longevity. However, to ensure optimal performance, various chemicals are often introduced into the cooling water to prevent problems that could arise during operation.
Cooling water systems operate through the transfer of heat away from industrial processes. The efficiency of this heat exchange can be significantly affected by scaling, corrosion, and biological growth within the cooling water. To combat these issues, a range of chemicals is employed, each serving a specific purpose to enhance the system's overall effectiveness.
1. Corrosion Inhibitors
Corrosion inhibitors are crucial in protecting metal components of cooling systems, such as pipes and heat exchangers. These chemicals work by forming a protective layer on the metal surfaces, thereby reducing the rate of corrosion. Common corrosion inhibitors include phosphates, nitrites, and azoles, each tailored to mitigate corrosion in different types of water chemistry. The choice of inhibitor depends on factors such as pH, temperature, and the metals involved. Regular monitoring of corrosion rates is essential to ensure that inhibitors remain effective over time.
Scaling, the buildup of mineral deposits, is another significant challenge in cooling water systems. Scale can severely impede heat transfer, increase energy consumption, and ultimately lead to costly downtime. Scale inhibitors, such as polyacrylic acids and phosphonates, are used to prevent the precipitation of calcium, magnesium, and other minerals that can form scale. These chemicals either modify the crystal growth of scale-forming minerals or keep them in suspension, allowing them to be easily removed or flushed from the system.
3. Biocides
chemical used for cooling water
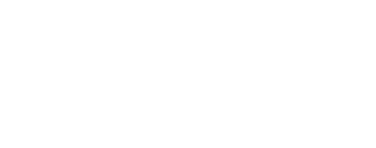
The presence of biological growth in cooling water systems can lead to biofouling, resulting in reduced heat transfer efficiency, increased pressure drops, and even the degradation of materials. Biocides are introduced to control microbial growth, including bacteria, algae, and fungi. Common biocides include chlorine, bromine, and non-oxidizing agents like isothiazolinones. The choice of biocide depends on the specific biological threats present and the operating conditions of the cooling system. Regular testing for microbial activity helps in determining the required frequency and dosage of biocides.
4. pH Adjusters
Maintaining the correct pH level in cooling water is crucial for optimizing the function of various chemicals and minimizing corrosion and scale formation. pH adjusters, such as sodium hydroxide or sulfuric acid, are used to alkalinize or acidify the water, respectively. The ideal pH range typically falls between 6.5 and 8.5, depending on the specific water chemistry and materials used in the cooling system. Routine pH monitoring is essential for maintaining optimal conditions.
5. Antifoam Agents
Foaming can disrupt the operation of cooling water systems by creating vapor pockets, reducing heat transfer efficiency, and increasing maintenance needs. Antifoam agents, such as silicone-based compounds, are added to mitigate foaming problems. These agents work by breaking down the surface tension of the foam, allowing it to collapse and preventing the accumulation of vapor pockets in the system.
Conclusion
In conclusion, the use of specific chemicals to treat cooling water is essential for ensuring the efficiency and reliability of industrial cooling systems. Corrosion inhibitors, scale inhibitors, biocides, pH adjusters, and antifoam agents each play a critical role in preventing issues that could compromise system performance. Proper management and regular monitoring of chemical treatments are vital for maintaining the balance needed to support effective cooling operations. By understanding and implementing the right chemical strategies, industries can enhance their cooling systems' performance, reduce maintenance costs, and improve overall sustainability.