Chemicals Used in Cooling Towers Essential for Efficiency and Longevity
Cooling towers are crucial components in numerous industrial and commercial processes, enabling efficient heat dissipation and regulation. However, to maximize their performance, a range of chemicals is utilized for water treatment and maintenance. Understanding these chemicals and their functions can help ensure cooling tower efficiency, prolong lifespan, and prevent costly repairs or replacements.
1. Corrosion Inhibitors
One of the primary concerns in cooling tower operation is corrosion, which can lead to severe inefficiencies and structural failures. Corrosion inhibitors are chemicals designed to safeguard metal surfaces from corrosion by forming a protective film. Commonly used inhibitors include phosphonates, molybdates, and nitrites. Each of these chemicals works by either reducing the electrochemical reactions that lead to corrosion or by providing a barrier that protects the metal from corrosive agents in the water. Proper use of corrosion inhibitors is crucial, especially in systems that utilize recycled or treated water, which may contain aggressive ions that accelerate corrosion.
2. Scale Inhibitors
Mineral scale build-up can significantly impede heat transfer efficiency, leading to increased operational costs. Scale inhibitors, such as polyacrylic acid and phosphonates, help to control the formation of scale deposits by preventing minerals like calcium and magnesium from precipitating out of solution. These chemicals work by interfering with crystal growth and promoting the dispersion of scale-forming compounds. In systems that operate at higher temperatures or with hard water, the use of effective scale inhibitors can enhance heat exchange and reduce the frequency of maintenance shutdowns.
3. Biocides
Cooling towers are an ideal environment for microbial growth, including harmful bacteria like Legionella. To mitigate these risks, biocides are employed to control biological fouling. Common biocides include chlorine, bromine, and non-oxidizing agents such as isothiazolinones and quaternary ammonium compounds. Chlorine is effective and widely used, but it can be corrosive and may lead to the formation of harmful by-products. Therefore, careful monitoring and management of biocide levels are essential to balance efficacy and safety in the cooling system.
cooling tower chemicals used
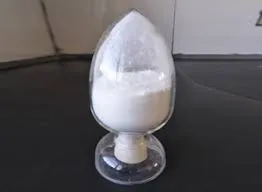
4. pH Adjusters
Maintaining the correct pH level is vital for the overall health of a cooling tower system. pH adjusters, such as sodium hydroxide or sulfuric acid, are used to keep the water within an optimal pH range (typically between 6.5 and 8.5). This ensures that corrosion inhibitors perform effectively and minimizes scaling tendencies. Monitoring and adjusting pH levels are essential practices in water treatment to protect equipment and enhance the efficiency of corrosion and scale inhibitors.
5. Defoamers
Foam can create operational issues in cooling towers by reducing heat transfer efficiency and leading to overflow. Defoamers are added to counteract foaming caused by oil, surfactants, or biomass. These chemicals work by breaking down foam bubbles, allowing for easier water circulation and efficient heat exchange. Regular use of defoamers helps maintain system integrity and operational reliability.
6. Cleaners and Descalers
Occasionally, cooling towers will require a thorough cleaning to remove accumulated dirt, scale, and biofilm. Specialized cleaning chemicals, such as citric acid and hydrochloric acid, are used to dissolve scale deposits and biofilms during maintenance sessions. Using these cleaners not only restores the cooling tower’s efficiency but also extends its operational lifespan.
Conclusion
The proper management of cooling tower chemistry is essential for maintaining efficiency, preventing downtime, and ensuring longevity. By utilizing a combination of corrosion inhibitors, scale inhibitors, biocides, pH adjusters, defoamers, and specialized cleaning agents, facility operators can address potential issues effectively and create a safer, more efficient cooling environment. Regular monitoring and proactive maintenance, combined with the correct chemical treatments, will help optimize the performance of cooling towers and contribute to sustainable industrial practices.