Cooling Tower Chemical Treatment Ensuring Efficiency and Longevity
Cooling towers play a vital role in various industrial and commercial applications by dissipating heat from process equipment and maintaining optimal operating temperatures. However, to ensure efficient operation and extend the lifespan of cooling towers, regular chemical treatment is essential. This article explores the importance of chemical treatment for cooling towers, the common chemicals used, the potential problems that can arise without proper treatment, and best practices for effective management.
The Importance of Chemical Treatment
Cooling towers operate by exchanging heat from the water to the atmosphere. During this process, several factors can compromise the efficiency and functionality of the system, including scale formation, corrosion, and biological growth. Chemical treatment is crucial for mitigating these issues. By using specific chemicals, operators can prevent scale deposits, control pH levels, and inhibit the growth of microorganisms such as algae and bacteria.
Effective chemical treatment leads to several benefits, including improved heat transfer efficiency, reduced energy consumption, and decreased maintenance costs. Furthermore, it significantly extends the life of the cooling tower, allowing for better return on investment.
Common Chemicals Used in Cooling Tower Treatment
1. Biocides These chemicals are essential for controlling the growth of bacteria, algae, and other microorganisms that can thrive in the warm, moist environment of a cooling tower. Common biocides include chlorine, bromine, and various non-oxidizing biocides. Proper dosing is crucial, as excessive use can lead to harmful by-products and affect downstream equipment.
2. Corrosion Inhibitors To protect metal components of the cooling tower from oxidation, corrosion inhibitors are added. These chemicals form a protective layer on the metal surface, preventing corrosive agents in the water from causing damage. Common corrosion inhibitors include phosphonates and organic inhibitors.
3. Scale Inhibitors Scale formation can significantly hinder the heat exchange process. Chemicals such as polyacrylic acid and phosphonates are used to inhibit the precipitation of minerals, such as calcium and magnesium, which form scale deposits. This ensures smooth operation and reduces the frequency of cleaning and maintenance.
4. pH Control Agents Maintaining the proper pH level in the cooling water is critical for optimal performance. Chemicals like sodium hydroxide or sulfuric acid are used to adjust pH levels, which can prevent both corrosion and scaling.
cooling tower chemical treatment
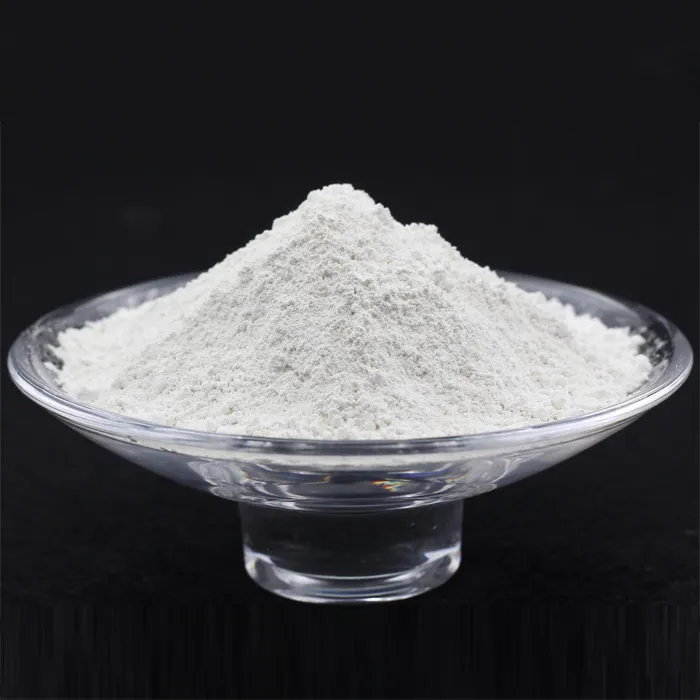
Risks of Neglecting Chemical Treatment
Failing to incorporate proper chemical treatment can result in significant operational issues. Scale buildup can lead to reduced heat transfer efficiency, requiring more energy to achieve desired cooling levels. Corrosion can cause leaks and equipment failure, resulting in costly repairs and extended downtime. Additionally, unchecked biological growth can lead to Legionella outbreaks, posing serious health risks.
Moreover, regulatory compliance can be a concern, as many jurisdictions require specific water treatment protocols to prevent environmental harms. Neglecting these aspects can lead to fines and further scrutiny from regulatory bodies.
Best Practices for Effective Cooling Tower Chemical Treatment
1. Regular Monitoring Implementing a regular monitoring schedule for water quality parameters—such as pH, conductivity, and microbiological content—is essential. This allows for timely adjustments to chemical dosing.
2. Tailored Treatment Programs Every cooling system is unique; therefore, treatment programs should be tailored according to specific operational conditions, water chemistry, and environmental factors. Consulting with water treatment professionals can ensure optimal program development.
3. Training and Safety Protocols Ensuring that staff is well-trained in handling chemicals and understands safety protocols is vital. This can minimize risks to personnel and the environment.
4. Periodic System Cleanings Regularly scheduled cleanings can help remove any existing build-up and ensure the system operates at peak efficiency.
5. Documentation and Compliance Keep detailed records of chemical usage, monitoring data, and maintenance activities to ensure compliance with environmental regulations and facilitate effective management.
In conclusion, the chemical treatment of cooling towers is not just an operational requirement but a strategic approach to enhancing system efficiency, longevity, and safety. By understanding the importance of systematic chemical management, operators can achieve optimized performance and a significant return on investment in their cooling systems.