The Role of Fillers Used in Plastics
In the realm of manufacturing, plastics have emerged as essential materials due to their versatility and lightweight properties. However, the incorporation of fillers into plastic formulations has significantly enhanced their performance and application scope. Fillers are typically inorganic or organic materials added to plastics to improve various properties or reduce costs. This article explores the types of fillers commonly used, their benefits, and their impact on the plastics industry.
Types of Fillers
Fillers can be broadly categorized into two main types functional fillers and non-functional fillers. Functional fillers are added to improve specific properties of the plastic, while non-functional fillers are primarily used to reduce costs.
1. Functional Fillers These fillers enhance the mechanical, thermal, or electrical properties of plastics. Common examples include - Calcium Carbonate Widely used in polypropylene and PVC, this filler improves stiffness, impact resistance, and reduces production costs. - Talc Known for its reinforcing properties, talc enhances thermal stability and rigidity, making it popular in automotive and consumer products. - Glass Fibers Often used in engineering thermoplastics, glass fibers significantly improve tensile strength and dimensional stability.
2. Non-Functional Fillers These are often employed to lower material costs without altering the resin's performance substantially. Examples include - Clay This inexpensive filler can enhance barrier properties and control viscosity. - Wood Flour Used in composite materials, wood flour contributes to a more sustainable production process while providing bulk and reducing cost.
Benefits of Using Fillers
The inclusion of fillers in plastic formulations yields numerous advantages
fillers used in plastics
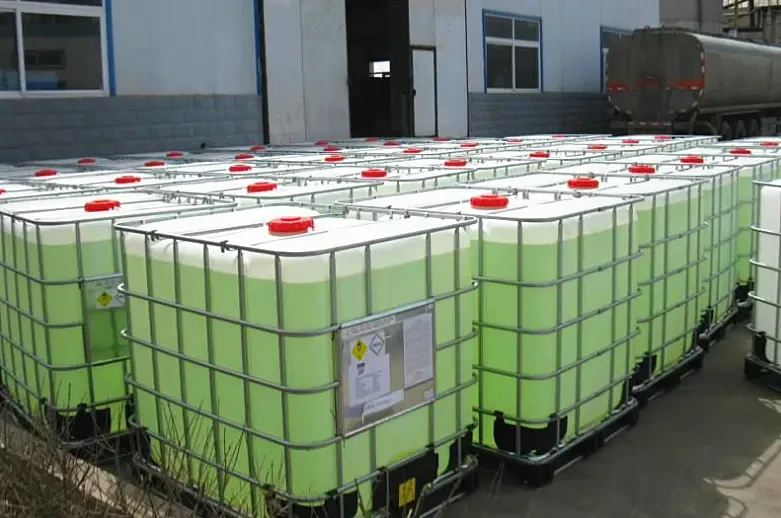
- Cost Reduction Fillers can lower the overall cost of plastic products, allowing manufacturers to maintain competitiveness in pricing. By partially replacing expensive resins with cheaper fillers, companies can optimize production expenses. - Enhanced Properties Fillers can improve various properties such as mechanical strength, thermal stability, impact resistance, and rigidity. By carefully selecting the type and amount of filler, manufacturers can tailor the performance of plastics to meet specific application requirements.
- Sustainability As environmental concerns grow, the use of natural fillers, such as cellulose and hemp, has gained traction. These bio-based fillers can help reduce the carbon footprint and promote more sustainable manufacturing practices.
- Processability Fillers can affect the processing characteristics of plastics. For example, certain fillers can improve the flow properties of molten plastics, making it easier to mold complex shapes in manufacturing processes.
Environmental Considerations
While fillers bring numerous benefits, their environmental impact should also be considered. Some inorganic fillers, like heavy metals, can contribute to pollution and waste issues. Hence, the trend is shifting towards using eco-friendly, biodegradable fillers to mitigate adverse environmental effects. Manufacturers are increasingly researching alternatives that are both effective and sustainable.
Conclusion
Fillers play a crucial role in the plastics industry, offering a multifaceted approach to enhancing plastic materials' performance while keeping costs in check. As innovation continues, the advent of new fillers and improvements in sustainable practices will likely shape the future of plastic manufacturing. By balancing functionality, cost, and environmental responsibility, the incorporation of fillers will remain a vital aspect of developing advanced plastic products in various industries. From automotive to consumer goods, the impact of fillers is undeniable, fostering a more efficient and sustainable use of plastic materials.