The Role of Fillers Used in Plastics
In the world of materials science, plastics have emerged as one of the most versatile and widely used materials. From household items to automotive parts, plastics can be found in nearly every facet of modern life. However, the properties of plastics can be significantly enhanced through the addition of fillers, which are substances mixed into the polymer matrix to improve various characteristics. This article examines the types of fillers used in plastics and their impact on functionality, cost, and sustainability.
*Types of Fillers*
Fillers can be categorized into two main types inorganic and organic fillers. Inorganic fillers, such as calcium carbonate, talc, and silica, are commonly used due to their cost-effectiveness and ability to improve mechanical properties. For example, calcium carbonate not only reduces production costs but also enhances the stiffness and impact resistance of the plastic.
Organic fillers, including wood flour, cellulose, and natural fibers, are increasingly popular due to their renewable nature and reduce carbon footprint. These fillers not only improve strength but also contribute to a more sustainable product. For instance, plastics reinforced with natural fibers have gained traction in the automotive industry as manufacturers are continually seeking lightweight, strong materials that also address environmental concerns.
*Functional Benefits*
The inclusion of fillers can modify the physical, thermal, and mechanical properties of plastics. For example, fillers can enhance tensile strength and reduce material brittleness, thus making plastics more durable. Additionally, incorporating specific fillers can improve thermal resistance, making them suitable for applications exposed to heat.
Fillers also play a pivotal role in improving the processing characteristics of plastics. For instance, adding an appropriate amount of filler can result in better flow properties during injection molding, leading to enhanced efficiency in production processes. Furthermore, certain types of fillers can improve the barrier properties of plastics, making them more effective for packaging applications where protection against moisture or gases is crucial.
fillers used in plastics
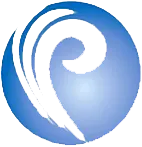
*Economic Impact*
From an economic perspective, one of the primary reasons for the incorporation of fillers is cost reduction. High-performance plastics can be expensive, but the introduction of fillers allows manufacturers to maintain desired performance levels while reducing material costs. This is particularly beneficial in mass-production settings, where cost efficiency is vital for competitiveness.
However, the economic benefits must be balanced against potential trade-offs. While fillers can reduce the raw material cost, they can also impact other properties such as aesthetic quality and processing requirements. Manufacturers need to find the right balance to ensure they meet the desired specifications for end products without compromising on quality.
*Sustainability Concerns*
As the world moves towards sustainability, the choice of fillers is increasingly dictated by environmental considerations. The use of recyclable or biodegradable fillers is gaining attention in the plastics industry, as it aligns with the growing demand for eco-friendly products. This trend not only addresses environmental issues but also appeals to consumers who are more conscious of sustainability.
Research and development in this area are critical. Innovations in bio-based materials and fillers derived from agricultural waste offer promising avenues for reducing reliance on fossil fuels and minimizing carbon footprints.
*Conclusion*
The use of fillers in plastics is not merely a means to an end but an integral part of material development that influences functionality, economics, and sustainability. As industries continue to evolve in their quest for performance, cost-efficiency, and environmental responsibility, the role of fillers will remain crucial. By understanding and leveraging the benefits that fillers bring, manufacturers can ensure the advancement of plastics that are not only versatile but also responsible.