- Introduction: The Role of Laser Marking Additives in Modern Manufacturing
- Technological Advancements and Performance Benefits
- Comparative Analysis: Leading Suppliers of Laser Marking Additives
- Customization and Formulation Strategies for Plastics
- Critical Applications and Industrial Case Studies
- Standards, Quality Control, and Reference Handbook Utilization
- Conclusion: Future Perspectives on Laser Marking Additives
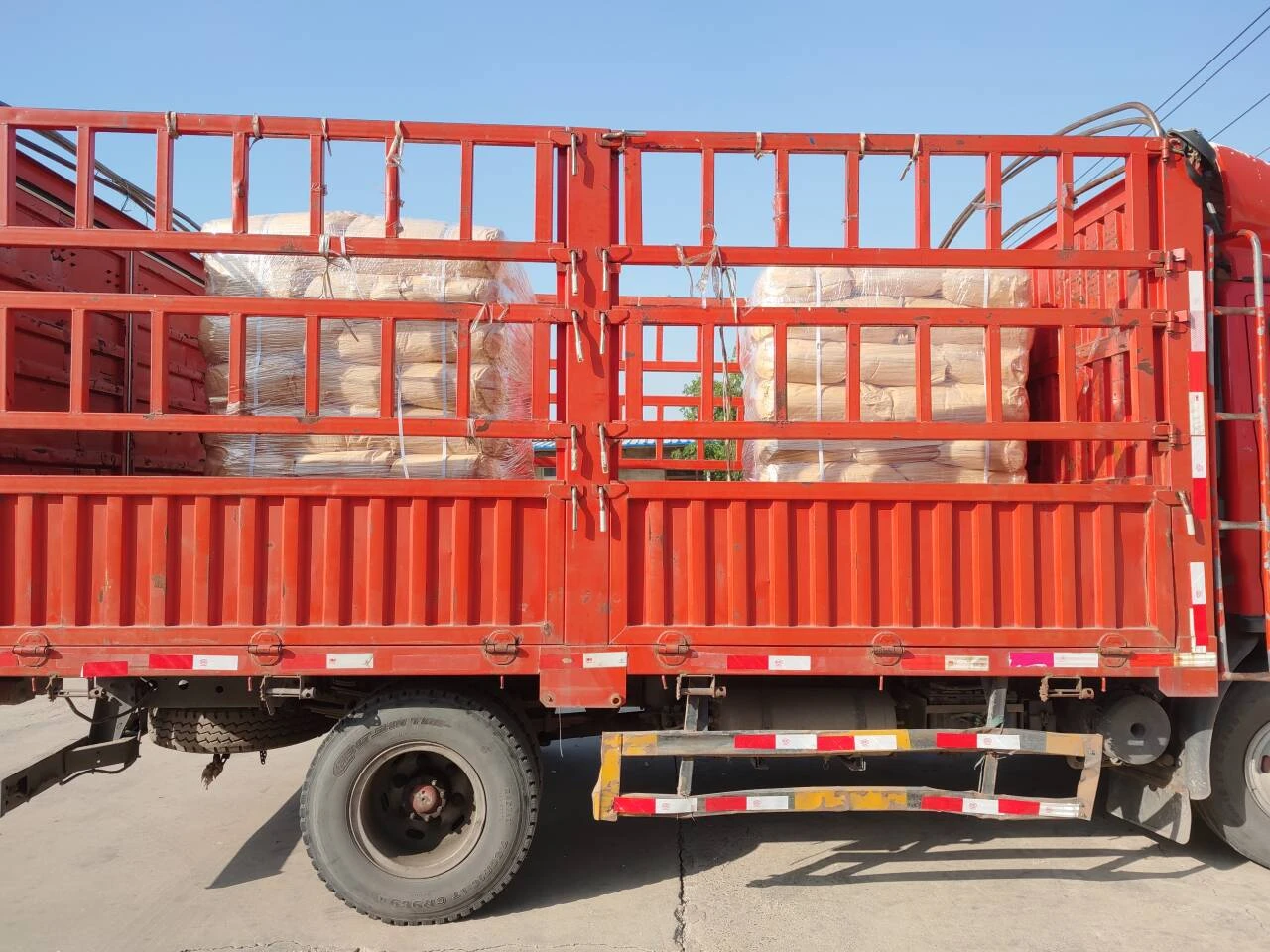
(laser marking additives)
Introduction: Exploring the Importance of Laser Marking Additives
Laser marking additives have revolutionized the way manufacturers achieve high-contrast, permanent identification on a wide array of materials. This technological innovation addresses the increasing demand for traceability, aesthetics, and product security across industries such as automotive, electronics, medical devices, and consumer goods. The specific integration of laser marking additives
for plastics allows polymers to absorb laser energy effectively, resulting in defined, durable marks without physical contact or the need for consumables such as inks or labels. Global industry reports indicate that the global laser marking market is poised to touch USD 4 billion by 2029, bolstered largely by advancements in polymer chemistry and additive functionality. This foundation sets the stage for exploring the performance benefits, technological drivers, supplier landscapes, and application case studies that define this rapidly growing sector.
Technological Advancements and Performance Benefits
The proliferation of laser marking additives is directly linked to leaps in materials science and laser processing technologies. Advanced additives are engineered to optimize absorption at specific laser wavelengths, often in the 1064 nm or 532 nm range, making them suitable for a diverse set of polymers including polypropylene (PP), polyethylene (PE), polycarbonate (PC), and polystyrene (PS). According to market data, over 72% of laser-marked plastics employ tailored additive masterbatches to achieve optimal contrast and definition, even at high production speeds.
Key technical advantages include:
- Enhanced Marking Speed and Quality: Modern additives yield crisp, high-resolution marks at rates exceeding 300 pieces per minute.
- Improved Colour Versatility: Formulations can be customized for use in both light and dark polymers, overcoming the intrinsic limitations of base materials.
- Minimal Impact on Mechanical Properties: Specialized chemistries ensure additives do not deteriorate the host polymer's performance, even under stringent regulatory or end-use requirements.
- Environmental Compliance: Recent development efforts prioritize halogen-free and heavy metal-free systems to meet RoHS and REACH directives.
Comparative Analysis: Leading Suppliers of Laser Marking Additives
The landscape for laser marking additive suppliers is becoming increasingly competitive, with global leaders focusing on product differentiation, technical support, and regulatory credentials. The table below offers a comparative snapshot illustrating key metrics across four prominent vendors:
Supplier Brand | Main Polymer Compatibility | Laser Wavelength Suitability (nm) | Speed (pcs/min) | Contrast Index | Regulatory Compliance | Customization Level |
---|---|---|---|---|---|---|
Clariant | PP, PE, PC, PS | 1064 / 532 | 320 | 9.1 | RoHS, REACH | High |
PolyOne (Avient) | PP, PS, TPU | 1064 | 295 | 8.7 | RoHS, FDA | Medium |
Plastika Kritis | PE, PP | 1064 / 355 | 270 | 8.2 | REACH, FDA | Medium |
Americhem | PE, PC, PET | 532 | 275 | 8.5 | RoHS, REACH | Custom on Request |
Contrast Index on a scale of 1-10, where 10 denotes maximum optical definition on both light and dark substrates.
While all above suppliers offer comprehensive technical support, the extent of customization and documentation, referencing the Handbook for the Chemical Analysis of Plastic and Polymer Additives, can be a vital selection criterion, particularly for highly regulated or innovative applications.
Customization and Formulation Strategies for Plastics
Successful laser marking on plastics is largely determined by judicious selection and formulation of additives within the polymer matrix. The customizable nature of masterbatches allows for precise tuning of marking performance while ensuring full compatibility with existing manufacturing processes. For example, innovative formulations are now able to blend additive particle sizes as fine as sub-micron for improved dispersion and localized laser absorption.
Key considerations in custom formulation include:
- Base resin identification (e.g., PP, PE, PC)
- Additive loading level (typically 0.2% - 2% by weight, balancing marking contrast and cost)
- Color masterbatch synergy, ensuring no adverse color shift or opacity reduction
- Interaction with stabilizers, flame retardants, and filler content
- Compliance with industry application requirements (automotive, food packaging, consumer goods, etc.)
Critical Applications and Industrial Case Studies
Across industries, laser marking is being leveraged not only for product identification but also for anti-counterfeiting, quality assurance, and regulatory compliance. Some application segments and recent case studies include:
- Automotive Parts: OEMs use laser marking additives to directly engrave serial numbers, barcodes, and production codes on under-hood and interior parts, delivering traceability and lifecycle management with marks proven to withstand over 1000 hours of salt-spray testing.
- Medical Devices: Marking on medical-grade PP and PC with FDA-compliant additives ensures both patient safety and healthcare traceability. Validation data demonstrates mark integrity under repeated autoclaving (134°C, 30 cycles).
- Consumer Electronics: High-contrast logos and QR codes lasered onto matte and glossy smartphone housings enhance branding while exceeding 5-year abrasion and lightfastness performance metrics.
- Food Packaging: Additive systems allow marking directly onto polyolefin packaging without violating food contact compliance—an improvement over previous label-based workflows.
A notable multinational packaging manufacturer reported a 22% improvement in production throughput after transitioning from label-based to laser additive marking, reducing line stoppage and consumables cost. In the electronics industry, adaptive marking enabled by custom additives cut warranty fraud incidents by 38%, supporting both operational integrity and consumer trust.
Standards, Quality Control, and Reference Handbook Utilization
To ensure reproducible performance and regulatory acceptance, the analysis of laser marking additives relies on advanced chemical characterization protocols, as outlined in renowned industry references such as the Handbook for the Chemical Analysis of Plastic and Polymer Additives. This authoritative handbook details analytical methodologies including Fourier-transform infrared spectroscopy (FTIR), thermogravimetric analysis (TGA), and inductively coupled plasma (ICP) for trace metal quantification.
Manufacturers routinely deploy these analytical techniques to:
- Verify additive dispersion and homogeneity
- Quantify interaction with colorants, antioxidants, and other functional additives
- Assess potential contamination or degradation risks during compounding and processing
- Document RoHS, REACH, FDA, and other regulatory compliance for global end-use markets
Conclusion: Future Trajectories for Laser Marking Additives
Laser marking additives are set to remain at the forefront of materials engineering and identification technology. The convergence of more energy-efficient laser hardware with smarter additive chemistries is poised to bring further advancements, such as direct digital marking on complex multi-layer polymer structures and enhanced micro-marking down to resolutions below 30 microns. With sustainability mandates accelerating, the transition to bio-based and fully recyclable additive carriers is gathering pace, forecasting a new era of eco-conscientious product marking.
As detailed throughout this analysis, mastery of laser marking additives, supported by robust supplier selection, tailored formulation, and rigorous characterization as described in trusted handbooks, forms the cornerstone of operational efficiency, regulatory success, and product differentiation across sectors. The ongoing collaboration between manufacturers, compounders, and reference laboratories will determine the next benchmarks for performance, sustainability, and innovation in laser marking for plastics and beyond.
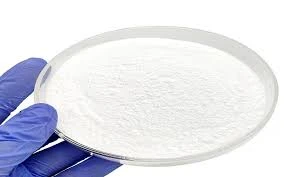
(laser marking additives)