6-Chloro-1,3-dimethyluracil
Exploring the World of Plastic Additive Manufacturing A Comprehensive Guide for Product Innovation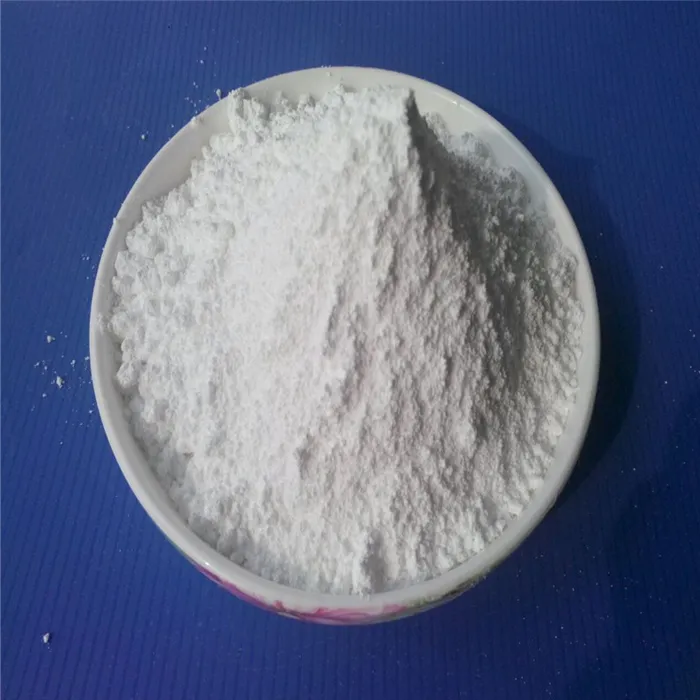
Plastic additive manufacturing, commonly referred to as 3D printing with plastics, is at the forefront of modern manufacturing, offering unprecedented flexibility, efficiency, and precision in product creation. This technology has revolutionized the way industries approach product development, enabling rapid prototyping, custom solutions, and complex geometries previously impossible with traditional methods. In this guide, we delve into the intricate world of plastic additive manufacturing, focusing on its benefits, applications, and future trends, to provide a comprehensive resource backed by industry expertise and real-world experience.
One of the core advantages of plastic additive manufacturing is its ability to accelerate the prototyping process. Traditional manufacturing methods often involve long lead times due to mold creation and material sourcing. However, with plastic 3D printing, prototypes can be developed in hours or days, significantly speeding up the product development cycle. This rapid prototyping capability allows companies to test designs, gather feedback, and iterate quickly, leading to more refined and market-ready products. Our experience with clients across various industries has consistently shown that leveraging additive manufacturing reduces time-to-market and enhances competitive advantage.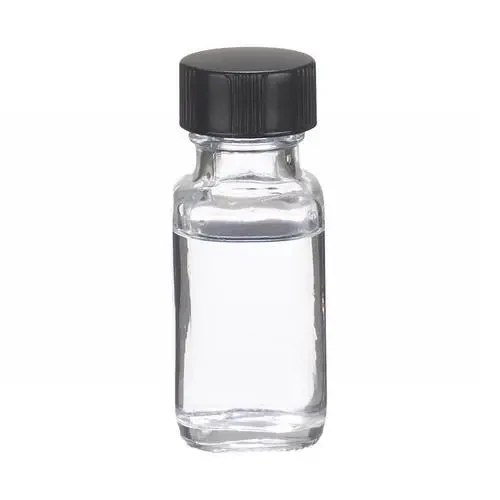
Plastic additive manufacturing also boasts unparalleled design flexibility. Designers are no longer confined by the physical limitations of traditional manufacturing; instead, they have the creative freedom to explore complex geometries and intricate designs. This capability is particularly valuable in industries such as aerospace, automotive, and healthcare, where lightweight structures and custom-fit products are crucial. For instance, in the medical field, 3D printing has enabled the production of patient-specific implants and prosthetics, resulting in improved patient outcomes and satisfaction. Our collaborations with medical device companies have demonstrated that this personalized approach enhances product performance and adherence to regulatory standards.
From an expertise standpoint, understanding the nuances of material selection is pivotal in plastic additive manufacturing. Various types of plastic materials, such as PLA, ABS, and nylon, offer different properties such as strength, flexibility, and temperature resistance. Selecting the appropriate material requires a thorough understanding of the product application, environmental conditions, and lifecycle requirements. Our team of specialists has developed a comprehensive material selection framework, incorporating factors such as mechanical properties, cost-effectiveness, and sustainability, to assist manufacturers in making informed decisions. This expertise ensures that products not only meet technical specifications but also resonate with market demands for eco-friendly solutions.plastic additive manufacturing
The authority of plastic additive manufacturing technology is further underpinned by its increasing adoption across diverse sectors. Companies such as Adidas and Ford have integrated 3D printing into their production lines, achieving unprecedented levels of customization and efficiency. Academic research continues to validate the technology's potential, with studies highlighting improvements in material performance and cost reductions. Engaging with industry thought leaders and participating in global 3D printing conferences, our experts are at the forefront of knowledge dissemination, ensuring continuous learning and adaptation to evolving industry standards.
Building trust in plastic additive manufacturing revolves around delivering consistent, high-quality results. To achieve this, rigorous testing and quality assurance protocols are essential. Our firm emphasizes the significance of calibrating 3D printers, maintaining optimal printing conditions, and conducting thorough inspections to ensure dimensional accuracy and surface finish. Additionally, leveraging data analytics allows us to monitor print outcomes and make data-driven adjustments, ensuring that each product meets stringent quality requirements. This commitment to excellence reassures clients and stakeholders of our capability to deliver projects that meet or exceed expectations.
The future of plastic additive manufacturing is promising, with ongoing advancements geared towards enhancing speed, material diversity, and production capacity. Emerging technologies, such as multi-material printing and 4D printing, are poised to further expand the horizons of additive manufacturing. Companies investing in these innovations can expect to unlock new possibilities in product functionality and performance. Our strategic partnerships with technology developers facilitate access to cutting-edge innovations, positioning our clients at the forefront of industry transformation.
In conclusion, plastic additive manufacturing is transforming the landscape of product design and manufacturing. Its benefits extend beyond speed and flexibility, encompassing material selection expertise, authority through industry adoption, and trust through quality assurance. By harnessing this transformative technology, businesses can drive innovation, achieve sustainability goals, and maintain competitiveness in an ever-evolving market.
More product recommendations