Plastic Fillers and Additives Enhancing Versatility and Performance
The world of plastics is vast and diverse, with an ever-growing array of applications in various industries, from automotive to consumer goods. One of the key factors that influence the performance, cost, and sustainability of plastic materials is the use of fillers and additives. These components play a crucial role in enhancing the properties of plastics, enabling manufacturers to produce materials tailored for specific applications while optimizing costs.
Understanding Plastic Fillers
Fillers are inert materials introduced into plastic formulations to improve certain physical or aesthetic properties without significantly affecting the overall performance. They can vary in composition, size, and shape, and are primarily used for the following reasons
1. Cost Reduction One of the main reasons for incorporating fillers is to reduce the overall material cost. By replacing a portion of the resin with a less expensive filler, manufacturers can achieve desirable properties at a lower price point.
2. Improved Mechanical Properties Fillers can enhance the strength, stiffness, and durability of plastics. For instance, glass fibers are commonly used to reinforce thermoplastics, significantly increasing their tensile strength.
3. Surface Finish and Aesthetic Qualities Fillers can also enhance the surface finish of plastics. Talc, calcium carbonate, and chalk are often added to improve the smoothness and gloss of the final product, making it more visually appealing.
4. Thermal and Acoustic Properties Certain fillers can improve the thermal stability and acoustic insulation of plastic products. The addition of materials like barium sulfate can enhance sound dampening capabilities.
5. Weight Reduction Lightweight fillers, such as hollow microspheres, can be employed to reduce the density of plastic products, which is particularly beneficial in industries like automotive, where weight savings can lead to improved fuel efficiency.
Common Types of Fillers
Several types of fillers are utilized in plastic formulations, each with unique characteristics and applications
- Mineral Fillers Talc, calcium carbonate, and clay are among the most common mineral fillers. They are often used in polypropylene and polyethylene to enhance stiffness and heat resistance. - Fibrous Fillers Glass fibers, carbon fibers, and natural fibers (like hemp or jute) are extensively utilized for their reinforcing properties, providing higher strength-to-weight ratios.
plastic fillers and additives
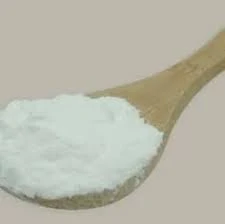
- Organic Fillers These include materials derived from natural sources, such as wood flour, which can impart a more environmentally friendly profile and contribute to a unique texture in biocomposites.
The Role of Additives
While fillers primarily focus on modifying the physical properties of plastics, additives play a broader role in enhancing the functionality of plastic materials. These substances are incorporated into the polymer matrix to achieve specific outcomes
1. Stabilizers Additives such as UV stabilizers and antioxidants help plastics withstand environmental stresses and prevent degradation caused by exposure to sunlight or heat.
2. Plasticizers These substances improve the flexibility and workability of plastic materials. Commonly used in PVC formulations, plasticizers lower the glass transition temperature, making the final product more pliable.
3. Flame Retardants In applications where fire resistance is critical, flame retardant additives are included to mitigate the risk of ignition and slow down the spread of flames.
4. Colorants Dyes and pigments are used to alter the color of plastics, allowing for creativity in product design and differentiation in the marketplace.
5. Processing Aids These additives enhance the processing of plastics during manufacturing, improving flow characteristics and reducing viscosity.
Future Trends
As the demand for sustainable and high-performance plastics increases, the role of fillers and additives is becoming more sophisticated. Innovations in biodegradable fillers and environmentally friendly additives are gaining traction as manufacturers aim to reduce their ecological footprint.
Moreover, the development of multifunctional fillers that combine several beneficial properties is on the rise. These advancements not only improve product performance but also provide manufacturers with the flexibility to create new solutions tailored to evolving market needs.
In conclusion, plastic fillers and additives are integral to the plastic industry, enhancing the performance and versatility of materials used across various applications. As technology continues to evolve, the future of plastics, driven by innovative and sustainable filler and additive solutions, looks promising. It is crucial for manufacturers to stay abreast of these developments to meet the challenges and opportunities in a rapidly changing market landscape.