Understanding Plastic Masterbatch A Key Component in Modern Manufacturing
Plastic masterbatch is a concentrated mixture of additives or pigments encapsulated within a carrier polymer. This innovative product plays a pivotal role in the plastic manufacturing industry, enhancing the properties of final plastic products while streamlining the production process.
What is Plastic Masterbatch?
At its core, plastic masterbatch is designed to impart specific characteristics to plastics. It consists of three primary components the base carrier polymer, the colorant or additive, and the processing aid, which facilitates easier incorporation into the host polymer. The masterbatch can be produced in various forms, including pellets, powders, and pastes.
The advantages of using masterbatches are manifold. By providing pre-dispersion of additives or pigments, masterbatches eliminate the need for manufacturers to handle raw materials in large quantities, thus simplifying the production process. This results in improved consistency in coloring and property enhancement, ultimately leading to higher quality end products.
Types of Plastic Masterbatch
The types of plastic masterbatches are diverse, catering to a wide range of applications. Some common categories include
1. Color Masterbatch These are used to provide vibrant color to plastic products. By incorporating pigments, manufacturers can create an extensive palette of colors, allowing for product differentiation and branding.
2. Additive Masterbatch These masterbatches enhance specific properties of plastics, such as UV resistance, flame retardancy, and anti-static properties. Such enhancements are crucial for applications in various industries, including automotive, packaging, and construction.
3. Specialty Masterbatch This category includes niche products that require specific formulations, such as glow-in-the-dark or metallic effects. These specialty masterbatches open up creative possibilities for designers and manufacturers.
plastic masterbatch
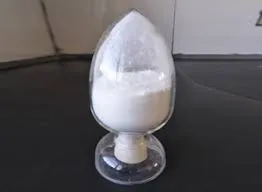
Benefits of Using Plastic Masterbatch
1. Consistency and Quality Control Masterbatches offer homogeneous distribution of additives, leading to consistent quality and performance in the final product. Manufacturers can achieve precision in color matching and property enhancement.
2. Cost-Effectiveness Utilizing plastic masterbatch can reduce the overall material costs. Masterbatches allow for the effective use of high-performance additives in smaller quantities, resulting in cost savings while maintaining desired properties in the final product.
3. Simplified Production Process The pre-dispersed nature of masterbatches reduces the complexities involved in adding additives directly to the polymer during processing. This leads to less downtime and increased efficiency in production lines.
4. Environmental Benefits With growing environmental concerns, many manufacturers are looking for ways to make their products more sustainable. Some masterbatches incorporate recycled materials or are designed to support biodegradable plastics, helping companies meet environmental regulations and reduce their carbon footprint.
Applications of Plastic Masterbatch
Plastic masterbatches find application across various industries. In packaging, for instance, they are extensively used to create visually appealing products while ensuring durability and protection. In the automotive sector, masterbatches enhance vehicle aesthetics while contributing to safety and performance through specialized properties.
Additionally, consumer goods, electronics, and medical devices all leverage the benefits of plastic masterbatches. Their versatility makes them a staple in modern manufacturing processes, enabling innovative designs and functionality.
Conclusion
Plastic masterbatch stands as a critical element in the evolution of the plastics industry. Its ability to enhance product quality, reduce costs, and facilitate sustainable practices positions it as a fundamental component in manufacturing. As technology advances and new formulations are developed, the role of plastic masterbatch will likely expand, driving further innovation across various sectors. Embracing this technology is essential for manufacturers looking to maintain a competitive edge in today's dynamic market.