Understanding Polyolefin Masterbatch A Key Component in Plastics Manufacturing
Introduction
In the world of plastics, the term masterbatch is frequently mentioned, especially when it comes to enhancing the properties of polyolefin materials. Polyolefins, which include polypropylene (PP) and polyethylene (PE), are among the most widely used plastics globally due to their excellent chemical resistance, affordability, and versatility. Polyolefin masterbatches are concentrated mixtures of additives, pigments, and other functional agents that are encapsulated in a polymer carrier, primarily used to improve the application properties of plastic products.
What is Polyolefin Masterbatch?
Polyolefin masterbatch is essentially a plastic concentrate containing a high concentration of additives that can include colorants, antioxidants, UV stabilizers, fillers, flame retardants, or processing aids. The masterbatch is produced by blending these additives into a polymer resin, resulting in highly concentrated product formulations that can be diluted during the final production stages. This practice improves efficiency as manufacturers can handle small quantities of masterbatch rather than bulk quantities of the individual components.
Types of Polyolefin Masterbatches
1. Color Masterbatch This is one of the most common types of polyolefin masterbatches, used to impart color to plastic products. Manufacturers can achieve a wide range of colors by mixing pigments with a polyolefin carrier. This enhances aesthetic appeal and can also contribute to brand recognition.
2. Additive Masterbatch These masterbatches contain functional additives that enhance the performance of the final product. This can include UV stabilizers to protect against sunlight degradation, flame retardants for safety, and processing aids to improve manufacturing efficiency.
3. Filler Masterbatch Fillers are often added to reduce material costs while maintaining the desired physical properties of the final product. Common fillers include talc, calcium carbonate, and glass fibers, which can modify rigidity, toughness, and thermal properties.
4. Specialty Masterbatches These include formulations designed for specific applications, such as antimicrobial masterbatches which provide resistance to bacteria and fungi, or anti-static masterbatches that reduce static charge accumulation in plastics.
polyolefin masterbatch
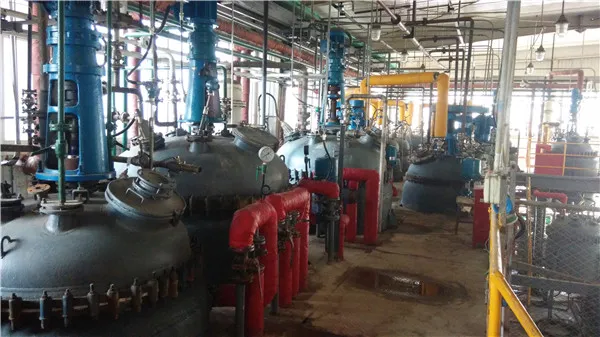
Benefits of Using Polyolefin Masterbatch
1. Enhanced Performance By incorporating specific additives through masterbatches, manufacturers can significantly enhance the physical and chemical properties of polyolefin products. This can include improved strength, flexibility, thermal stability, and resistance to environmental stress.
2. Efficiency and Cost Reduction Using masterbatches allows for precise formulation and reduces waste. Since the masterbatch holds a concentrated form of the additives, it allows for easier scaling during production and helps manufacturers achieve the desired properties without the need for complex mixing processes.
3. Consistency One of the major challenges in plastics manufacturing is ensuring the uniform distribution of additives. Masterbatches offer consistent quality and performance, as they are pre-processed and standardized before introduction into the production line.
4. Customization The ability to tailor masterbatches to meet specific requirements provides manufacturers with the flexibility to create customized solutions. Whether it’s a unique color, special performance characteristics, or specific regulatory compliance, masterbatches can be engineered to fit diverse needs.
Applications of Polyolefin Masterbatces
Polyolefin masterbatches are used across various industries. In packaging, they improve the appearance and performance of materials used for food containers, bags, and films. The automotive industry benefits from using these masterbatches to enhance the durability and aesthetic quality of interior and exterior components. Electronics manufacturers use polyolefin masterbatches to create housings that are not only visually appealing but also meet necessary safety standards.
Conclusion
Polyolefin masterbatches play a pivotal role in modern plastics manufacturing, providing significant advantages in terms of performance, efficiency, and customization. As industries continue to emphasize sustainability and innovation, the demand for high-quality masterbatches is expected to increase. Understanding and leveraging the potential of polyolefin masterbatches will be essential for manufacturers looking to enhance their product offerings and maintain competitive advantages in the evolving market landscape.