The Significance of Polyolefin Masterbatch in Modern Plastics Industry
In the realm of polymer technology, polyolefin masterbatch has emerged as a critical component, transforming the landscape of manufacturing and processing plastics. Masterbatches are concentrated mixtures of additives and pigments encapsulated in a polymer carrier, which allow manufacturers to achieve specific properties and colors in their end products. Polyolefin masterbatch specifically targets polyolefin resins such as polyethylene (PE) and polypropylene (PP), both of which are among the most widely used plastics in the industry.
Understanding Polyolefin Masterbatch
Polyolefins are a class of polymers derived from the polymerization of olefins. The most common types include low-density polyethylene (LDPE), high-density polyethylene (HDPE), and polypropylene. The versatility, lightweight nature, and chemical resistance of these materials have rendered them essential in various applications, including packaging, automotive parts, and consumer goods.
Polyolefin masterbatch serves multiple purposes. By integrating additives, manufacturers can enhance the mechanical properties, thermal stability, UV resistance, and color of polyolefin products. This is particularly beneficial in applications where durability and aesthetics are paramount. For instance, in the packaging industry, vibrant colored films produced with colored masterbatches not only fulfill functional requirements but also improve product appeal on retail shelves.
The Benefits of Using Polyolefin Masterbatch
1. Consistency and Quality Control One of the primary advantages of using masterbatches is the ability to achieve consistent coloration and performance in thermoplastic processing. This consistency minimizes production challenges and ensures that final products meet regulatory and consumer standards.
2. Enhanced Processing Efficiency Utilizing masterbatches can lead to improved efficiency during the production process. These concentrates are easier to handle, transport, and mix compared to separate additives and pigments. This streamlined approach reduces the likelihood of production errors and allows for faster transitions between different colors and formulations.
3. Cost-Effectiveness Although the initial cost of masterbatches may be higher compared to bulk additives, they can prove to be cost-effective in the long run. The high concentration of pigments and additives means that only small amounts are needed to achieve desired properties. Additionally, minimizing waste and improving process efficiencies can lead to significant savings.
polyolefin masterbatch
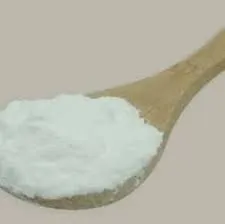
4. Customization The versatility of polyolefin masterbatches allows manufacturers to tailor formulations to meet specific needs. Whether it’s developing a unique color for branding or enhancing certain mechanical properties for specific applications, bespoke masterbatch solutions can be designed to meet a wide range of requirements.
Applications Across Industries
Polyolefin masterbatch finds applications in diverse sectors, highlighting its versatility. In the automotive industry, masterbatches can enhance the visual appeal of interior and exterior components while improving their durability against UV radiation and heat. In the packaging sector, colorful films, containers, and bags benefit from the aesthetic and functional attributes conferred by masterbatches, making products more attractive to consumers.
Moreover, in the agricultural sector, polyolefin masterbatches can be utilized to produce films that enhance crop yield by offering UV protection, moisture retention, and pest resistance. The construction industry also sees applications in producing materials that require color stability and strength.
Future Trends in Polyolefin Masterbatch Development
As industries strive for sustainability, the future of polyolefin masterbatches appears promising. Innovations in bio-based additives and pigments are paving the way for eco-friendlier solutions that reduce the carbon footprint of plastic products. Incorporating recycled materials into masterbatch formulations is another trend gaining traction, supporting the circular economy initiatives.
Additionally, advancements in nanotechnology are allowing for the development of masterbatches that can enhance not only the mechanical properties but also improve barrier functions and reduce weight, aligning with industry demands for lightweight and high-performance materials.
Conclusion
Polyolefin masterbatch is an invaluable asset within the plastics industry, delivering enhanced performance, aesthetic appeal, and operational efficiency. As technology continues to evolve, and sustainability becomes more critical, the adaptability and innovation surrounding polyolefin masterbatches will likely play a key role in the development of future materials. By understanding and harnessing the potential of polyolefin masterbatches, manufacturers can create higher-quality products that meet the demands of today's markets while paving the way for a more sustainable future.