The Role of Chemicals in Reverse Osmosis Treatment
Reverse osmosis (RO) is a widely used water purification technology that leverages a semi-permeable membrane to separate contaminants from water. This process is fundamental in various applications, ranging from residential water treatment systems to large-scale industrial operations. While the mechanics of reverse osmosis are crucial, the chemicals employed during the treatment process significantly influence its efficiency and effectiveness. This article delves into the various types of chemicals used in reverse osmosis treatment and the roles they play in optimizing the purification process.
1. Antiscalants
One of the primary challenges in reverse osmosis systems is membrane fouling and scaling. Minerals such as calcium carbonate, barium sulfate, and silica can precipitate and form deposits on the membrane surface, reducing its efficiency and lifespan. Antiscalants are chemical agents designed to prevent the formation of these scales by inhibiting crystal growth and dispersing existing particles. By incorporating antiscalants into the pretreatment process, operators can significantly extend the operational life of their RO membranes and minimize downtime caused by membrane cleaning and replacement.
In many cases, the feed water contains suspended solids and colloidal particles that can contribute to fouling. Coagulants and flocculants are chemicals that facilitate the aggregation of these small particles into larger clusters, known as flocs. The addition of coagulants, such as aluminum sulfate or ferric chloride, helps to destabilize the colloidal particles, while flocculants, such as polyacrylamides, enhance the formation of larger flocs that can be more easily removed via sedimentation or filtration. This pretreatment step is crucial for improving RO membrane performance and preventing fouling.
3. pH Adjusters
reverse osmosis treatment chemicals
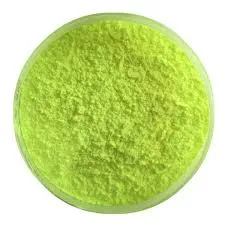
The pH of feed water can significantly affect both the solubility of scaling minerals and the overall performance of the RO process. Chemicals such as sulfuric acid, sodium hydroxide, or citric acid are often used as pH adjusters to maintain optimal acidity or alkalinity levels. Adjusting the pH can help to keep scaling minerals in solution, thus minimizing the risk of membrane fouling. Additionally, maintaining the appropriate pH is essential for maximizing the efficiency of both antiscalants and coagulants.
4. Biocides
Biological fouling caused by microorganisms can also impact RO systems, leading to reduced performance and increased maintenance costs. Biocides, such as chlorine, chloramines, or specific non-oxidizing biocidal products, are employed to control microbial growth. The careful application of biocides can prevent biofilm formation on the membrane surface, ensuring that the RO system operates at optimal levels. However, it is essential to consider the compatibility of biocides with the RO membranes, as some can cause membrane degradation if not handled correctly.
5. Cleaning Chemicals
Despite preventive measures, RO membranes may still require periodic cleaning to remove accumulated foulants. A variety of cleaning chemicals, including acidic and alkaline cleaners, are used depending on the type of foulants present. For instance, acidic cleaners are effective against mineral scales, while alkaline cleaners can remove organic matter and biofilms. Regular cleaning of membranes ensures sustained performance and production quality in reverse osmosis systems.
Conclusion
The use of chemicals in reverse osmosis treatment is integral to maintaining system efficiency and prolonging membrane life. From antiscalants and coagulants to biocides and cleaning agents, these chemicals play a vital role in optimizing the purification process. As technology continues to advance, ongoing research and development in water treatment chemicals will further enhance the effectiveness of reverse osmosis systems, ensuring reliable access to clean water for both industrial and residential applications.