Understanding Additives Used in Plastic Manufacturing
Plastic manufacturing is a complex process that transforms raw materials into useful products that we interact with daily. To enhance the performance, durability, and aesthetic appeal of plastic products, manufacturers often incorporate a variety of additives during production. These additives play crucial roles in altering the physical, chemical, and mechanical properties of plastics, making them more versatile and suitable for specific applications.
Types of Additives
1. Stabilizers One of the primary concerns in plastic manufacturing is the degradation of materials due to exposure to heat, light, and oxygen. Stabilizers are added to mitigate these effects. For instance, UV stabilizers protect plastics from ultraviolet radiation, which can lead to discoloration and brittleness. Thermal stabilizers, such as antioxidants, prevent thermal degradation during processing, ensuring that the integrity of the plastic is maintained.
2. Plasticizers These are substances added to increase the flexibility and workability of plastics. By reducing the glass transition temperature of the polymer, plasticizers make the material softer and more pliable. Common plasticizers include phthalates, which are widely used in PVC products. However, due to health concerns, manufacturers are increasingly looking for safer alternatives to traditional plasticizers.
3. Fillers Fillers are materials added to plastics to improve their mechanical properties, reduce costs, and enhance certain characteristics like thermal and electrical insulation. They can be inorganic, like calcium carbonate and talc, or organic, such as wood flour. Fillers also affect the density and opacity of the plastic, making them essential for achieving desired specifications in final products.
4. Colorants The aesthetic appeal of plastic products is often a primary consideration in manufacturing. Colorants, including pigments and dyes, allow manufacturers to create a wide range of colors for their products. These additives must be compatible with the base plastic and resist fading over time, as well as withstand various environmental factors.
5. Flame Retardants As fire safety regulations become stricter, flame retardants have become an essential additive in many plastic applications. These chemicals reduce the flammability of plastics, making them safer for use in electrical components, furniture, and building materials. However, some traditional flame retardants have come under scrutiny for their environmental impact and potential health risks, leading to a push for safer alternatives.
additives used in plastic manufacturing
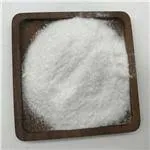
6. Anti-static Agents In various applications, especially in electronics, the build-up of static electricity can pose significant risks. Anti-static agents minimize static accumulation on plastic surfaces, protecting sensitive components from damage and ensuring the safe handling of products.
7. Impact Modifiers Plastics can be brittle, which limits their applications. Impact modifiers, such as rubber or certain copolymers, are added to enhance the toughness and impact resistance of plastic products. This is particularly important in applications such as automotive parts and packaging materials, where durability is critical.
8. Processing Aids These additives facilitate the manufacturing process by improving the flow of plastics during molding or extrusion. They can reduce viscosity, improve surface finish, and enhance overall production efficiency. Common processing aids include lubricants and surfactants that ensure a smooth production process.
Environmental Considerations
With the increasing focus on sustainability, the choice of additives is evolving. Manufacturers are seeking eco-friendly alternatives to traditional additives that may pose environmental risks. Biodegradable additives and natural fillers are gaining traction as industries look to reduce their ecological footprint. Additionally, the recycling of plastics often requires the removal of certain additives, which can complicate the recycling process. Therefore, the development of additive formulations that facilitate easier recycling is a growing area of innovation.
Conclusion
Additives in plastic manufacturing are essential for optimizing the properties and performance of final products. As the industry continues to evolve, the careful selection and formulation of these additives will play a vital role in meeting both consumer demands and environmental regulations. Understanding the function of various additives helps manufacturers create better products while also paving the way for more sustainable practices in an increasingly eco-conscious market. The future of plastic manufacturing will undoubtedly see further advancements, driven by the pursuit of innovation and sustainability.