Stabilizers in Plastic Enhancing Durability and Performance
In the world of plastics, stabilizers play a crucial role in ensuring that materials maintain their integrity and performance over time. Plastics, while versatile and widely used, are susceptible to degradation when exposed to environmental factors such as UV radiation, heat, and oxygen. Stabilizers are additives incorporated into plastic formulations to enhance their durability and extend their lifespan.
One of the primary functions of stabilizers in plastics is to inhibit the effects of ultraviolet (UV) radiation. Many plastics, especially those used in outdoor applications like construction materials, furniture, and automotive components, are exposed to sunlight. UV radiation can cause photodegradation, leading to discoloration, brittleness, and loss of mechanical properties. UV stabilizers, such as hindered amine light stabilizers (HALS) and UV absorbers, absorb or dissipate UV energy, preventing damage and preserving the aesthetic and functional qualities of the plastic.
Stabilizers in Plastic Enhancing Durability and Performance
Oxidation is another significant factor that can compromise the performance of plastics. When exposed to oxygen and heat, polymers can undergo oxidative degradation, resulting in a loss of tensile strength and flexibility. To combat this issue, antioxidant stabilizers are incorporated into plastic formulations. These compounds, which can be primary or secondary antioxidants, work by scavenging free radicals formed during the degradation process, thereby extending the material’s useful life.
stabilizer in plastic
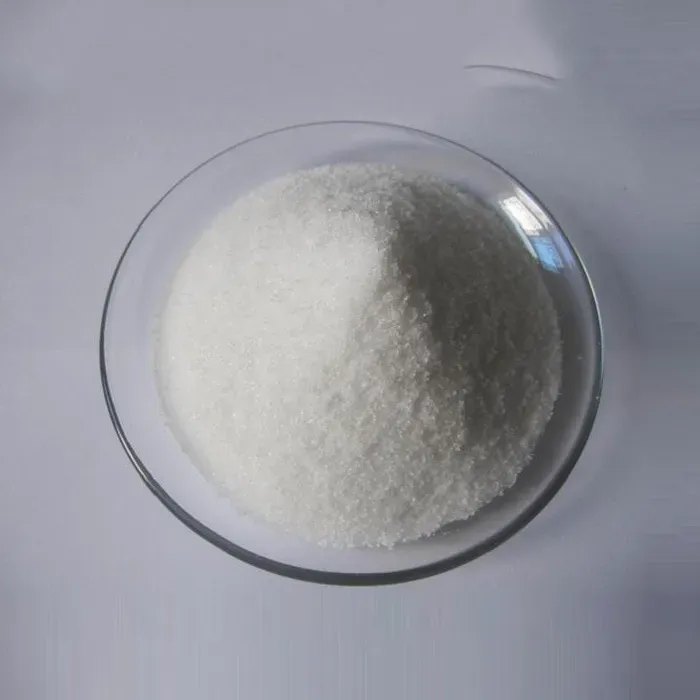
Additionally, stabilizers can improve the processing characteristics of plastics. Certain additives can enhance the flow properties of molten plastic during extrusion or injection molding, allowing for easier manufacturing and improved finished product quality. These processing aids can result in smoother surfaces and reduce defects, ultimately leading to cost savings in production.
The choice of stabilizer depends on various factors, including the type of plastic, its intended application, and the environmental conditions it will face. For example, polyvinyl chloride (PVC) often requires different types of stabilizers compared to polyethylene or polypropylene. Manufacturers must carefully select stabilizers to align with the specific requirements of their products while also considering regulatory compliance and environmental sustainability.
The increasing emphasis on sustainability has also ushered in a new era of plastic stabilizers. Many manufacturers are now exploring bio-based and non-toxic alternatives to traditional stabilizers. These green alternatives aim to mitigate the environmental impact of plastic production and disposal, aligning with global efforts to reduce plastic pollution.
In conclusion, stabilizers are an integral part of plastic manufacturing, enhancing the durability, performance, and processability of various polymer products. By preventing degradation caused by UV radiation, heat, and oxidation, stabilizers play a vital role in ensuring that plastics fulfil their practical and aesthetic functions over extended periods. As the industry continues to evolve, the development of innovative and sustainable stabilizers will be key to meeting both consumer demands and environmental challenges, paving the way for a brighter future in the realm of plastics. Through ongoing research and development, the use of stabilizers will continue to adapt to the changing landscape of materials science and technology, reinforcing the importance of these additives in the plastic industry.