Boiler Water Chemical Treatment Ensuring Efficiency and Longevity
In industrial settings, boilers play a critical role in the generation of steam, which is essential for various processes including power generation, heating, and driving turbines. However, the efficiency and longevity of a boiler system heavily depend on the quality of the water used in the boiler. This is where boiler water chemical treatment comes into play. Proper treatment of boiler water is vital to prevent scaling, corrosion, and carryover, ultimately ensuring the effective and efficient operation of boiler systems.
The Importance of Boiler Water Treatment
Boiler systems operate under conditions that can lead to a plethora of water-related issues. Without adequate treatment, the presence of impurities in the feed water can lead to scaling on the heat transfer surfaces. This scaling acts as an insulating barrier, reducing heat transfer efficiency, and leading to increased fuel consumption. In extreme cases, scale buildup can even lead to overheating and catastrophic failure of the boiler.
Another significant issue is corrosion, which can result from the presence of oxygen, carbon dioxide, and other corrosive substances in the water. Corrosion leads to the deterioration of metal components, potential leaks, and ultimately, significant costs in repairs and replacements. Additionally, improper boiler water chemistry can lead to carryover, where water droplets containing impurities are carried into the steam system. This can lead to fouling of downstream equipment, affecting overall system reliability and performance.
Key Components of Boiler Water Treatment
1. Chemical Additives The cornerstone of boiler water treatment involves the use of chemical additives designed to mitigate scaling and corrosion. Common additives include
boiler water chemical treatment
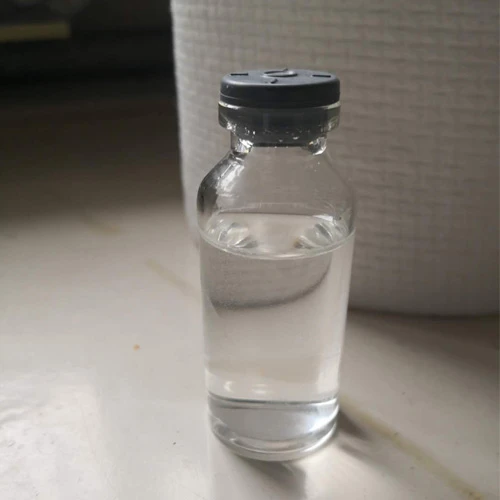
- Oxygen Scavengers These chemicals, such as sodium sulfite or hydrazine, are used to remove dissolved oxygen from the water, thereby preventing corrosion. - Scale Inhibitors Compounds like phosphate and polymer-based scale inhibitors are introduced to control mineral deposits and keep them in suspension, preventing them from adhering to boiler surfaces. - pH Adjusters Maintaining an optimal pH range is crucial for minimizing corrosion. Chemicals such as caustic soda (sodium hydroxide) or ammonia may be used to adjust the pH level of the boiler water.
2. Water Testing and Monitoring Continuous monitoring of water chemistry is critical for effective treatment. Regular testing for parameters such as pH, conductivity, total dissolved solids (TDS), and specific contaminants helps ensure that chemical dosing is adjusted according to the system’s needs. The use of automated monitoring systems can provide real-time data, allowing for immediate adjustments to treatment protocols.
3. Blowdown Practices Blowdown is the process of removing a portion of water from the boiler to control the concentration of impurities. Regular blowdown helps maintain water quality and prevents the buildup of TDS, which can lead to scaling and carryover. Proper blowdown procedures are essential for the overall effectiveness of chemical treatment programs.
Conclusion
The treatment of boiler water is a complex but essential process that ensures the efficient and safe operation of boiler systems. By implementing a comprehensive chemical treatment program that includes the use of additives, regular water quality monitoring, and effective blowdown practices, industries can significantly reduce the risks associated with scaling, corrosion, and carryover. The upfront investment in water treatment not only enhances the performance and reliability of boiler systems but also enables significant savings by reducing maintenance costs and increasing operational efficiency.
In summary, as industries increasingly recognize the importance of water quality in boiler operation, the role of chemical treatment has become more critical than ever. By prioritizing boiler water treatment, facilities can achieve optimal performance, extend equipment lifespan, and ultimately, enhance overall productivity.