Fillers for Polymers Enhancing Performance and Reducing Costs
Polymers are ubiquitous in modern manufacturing due to their versatility and ability to be molded into various shapes. However, to enhance their performance, reduce costs, and achieve specific properties, fillers are often incorporated into polymer formulations. Fillers are inert materials that are added to plastics, coatings, and rubber to improve their mechanical, thermal, and chemical properties. This article explores the different types of fillers used in polymers, their benefits, and the trends shaping their usage in the industry.
Types of Fillers
Fillers can be categorized into two primary types reinforcing fillers and non-reinforcing fillers. Reinforcing fillers, such as glass fibers, carbon black, and natural fibers, are used to enhance the strength and stiffness of polymers. These fillers are essential in applications where mechanical performance is critical, such as in automotive parts and structural components.
On the other hand, non-reinforcing fillers, such as calcium carbonate, talc, and silica, are typically used to reduce the cost of polymers without significantly affecting their mechanical properties. These fillers can improve the processing characteristics of polymers, such as flowability and viscosity, making them easier to mold and shape during manufacturing.
Benefits of Using Fillers
The incorporation of fillers into polymer formulations offers numerous benefits. Firstly, fillers can significantly reduce the production cost of polymers. By replacing a portion of the polymer resin with a less expensive filler, manufacturers can lower their material costs, making their products more competitive in the market.
fillers for polymers
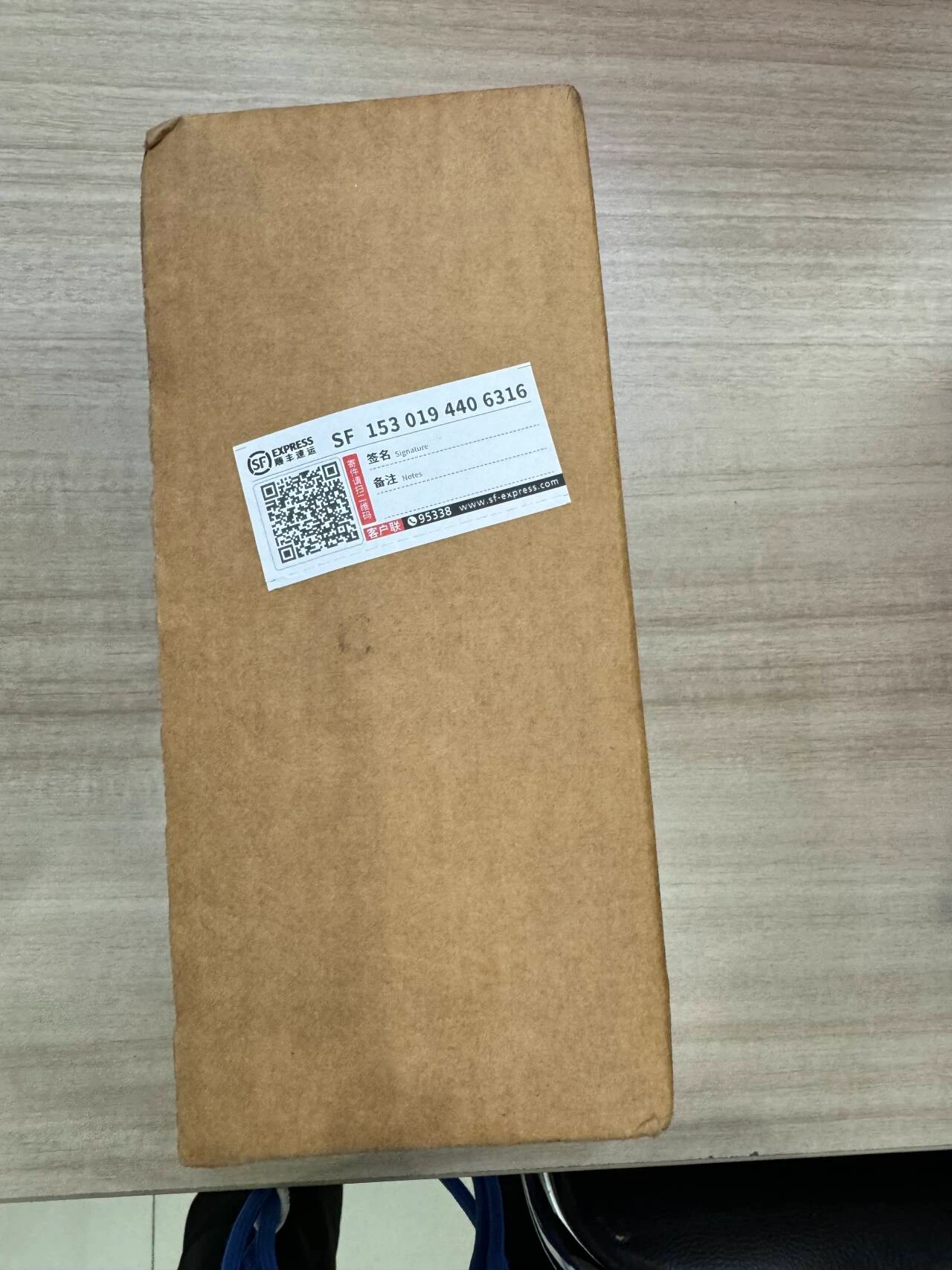
Secondly, fillers can enhance the physical properties of polymers. For example, adding glass fibers can improve tensile strength and impact resistance, making the material more durable. Similarly, adding flame-retardant fillers can improve the fire resistance of polymers, which is particularly important in applications such as electrical insulation and automotive interiors.
Moreover, fillers can improve processing characteristics. Some fillers can enhance the flow properties of polymers during injection molding, allowing for better filling of molds and reducing defects. Additionally, fillers can influence the thermal conductivity of polymers, making them suitable for applications that require heat dissipation.
Current Trends in Fillers for Polymers
There is a growing trend towards the use of sustainable and bio-based fillers in polymer formulations. As environmental concerns rise, manufacturers are seeking alternatives to traditional filler materials that are more eco-friendly. Natural fibers, such as kenaf, jute, and hemp, are increasingly being used as fillers due to their biodegradability and low carbon footprint. These fillers not only provide mechanical reinforcement but also contribute to a more sustainable manufacturing process.
Furthermore, the development of nanocomposites is gaining traction in the polymer industry. Nanoparticles, such as silica or clays, are being explored for their ability to enhance the properties of polymers at very low filler loading levels. This can lead to lightweight materials with superior performance characteristics, paving the way for innovation in various sectors, including automotive, aerospace, and consumer goods.
Conclusion
Fillers play a crucial role in optimizing the properties and performance of polymers. By selecting the right type of filler, manufacturers can achieve cost savings while enhancing the mechanical, thermal, and processing characteristics of their products. With the shift towards sustainable materials and the rise of nanocomposites, the landscape of fillers for polymers is evolving rapidly. As these trends continue to shape the industry, the future of polymer applications looks promising, offering a blend of performance, sustainability, and cost efficiency.