The Role of Chemicals in Cooling Tower Water Treatment
Cooling towers are essential components in various industries, helping to dissipate heat generated by industrial processes and systems. To maintain efficiency and prolong the lifespan of cooling towers, effective water treatment is critical. This is where chemicals come into play, as they serve multiple functions preventing corrosion, controlling scale, and reducing biological fouling.
Corrosion Control
One of the most significant challenges in cooling tower operations is corrosion, which can lead to severe damage and increased maintenance costs. Corrosion inhibitors are chemical additives that form a protective film on the metal surfaces of cooling systems, thereby preventing corrosion. Common materials used as corrosion inhibitors include phosphate-based compounds, molybdates, and amines. Each of these chemicals works differently phosphates bind with metal ions, thereby preventing them from reacting with corrosive agents, while molybdates provide a passivation effect that protects against rust formation.
The choice of corrosion inhibitor may depend on the specific metals used in the cooling system and the water chemistry. An essential step in managing corrosion involves regular monitoring and adjustment of the chemical dosage to ensure optimal protection.
Scale Control
Another critical aspect of cooling tower water treatment is scale control. As water evaporates in the cooling tower, the concentration of dissolved minerals, such as calcium and magnesium, increases. This can lead to the formation of scale, which accumulates on heat exchange surfaces, reducing efficiency and increasing energy costs.
Scale inhibitors, such as polyacrylic acids, phosphonates, and organic phosphates, are commonly used to manage scaling. These chemicals work by modifying the way mineral crystals form, either by preventing them from precipitating out of solution or by keeping them in a dispersed state. Using a combination of scale inhibitors can often yield better results, as different compounds target various types of scale formations.
Biocide Treatments
chemicals used in cooling tower water treatment
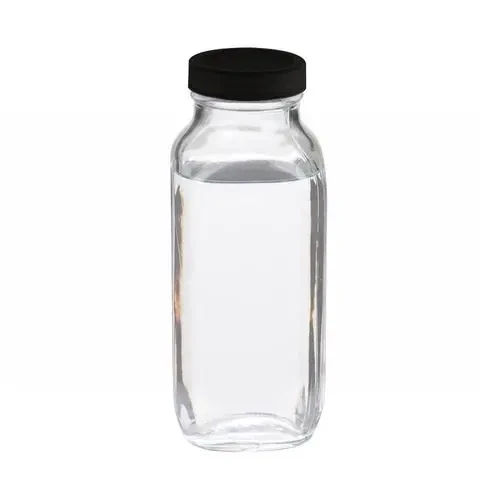
Biological fouling is another concern for cooling towers, as bacteria, algae, and other microorganisms can grow rapidly in warm, stagnant water. This biofilm can significantly hinder heat transfer efficiency and lead to corrosion. To combat this problem, biocides are introduced into the cooling water.
Biocides can be classified into two main categories oxidizing and non-oxidizing agents. Oxidizing biocides, such as chlorine and bromine, work by destroying microbial cells through oxidation. They are effective at quickly reducing microbial populations but may require careful monitoring to avoid harmful side effects, such as chlorine gas release.
Non-oxidizing biocides, including isothiazolinones and quaternary ammonium compounds, release biocidal agents in a controlled manner, often resulting in fewer operational challenges. They can be effective over extended periods and often require less frequent application than oxidizing agents.
pH and Alkalinity Adjustment
Maintaining the proper pH and alkalinity levels in cooling tower water is crucial for optimizing chemical treatment effectiveness. The water's pH affects the solubility of many scaling compounds and the performance of corrosion inhibitors. For instance, lower pH levels could enhance the corrosive nature of water, while higher levels may promote scale formation.
To achieve the desired pH levels, chemicals such as sodium hydroxide, sulfuric acid, or bicarbonate may be used. Regular monitoring and adjustment are vital to maintain balance, as fluctuations can lead to inefficiencies and operational problems.
Conclusion
In summary, the effective treatment of cooling tower water is essential for maintaining optimal performance and prolonging equipment lifespan. The use of various chemicals plays a pivotal role in controlling corrosion, scaling, and biological fouling. By carefully selecting and managing these chemicals, industries can enhance their cooling systems' efficiency, reduce maintenance costs, and promote sustainability. Continuous monitoring and adjustment are essential to tailor water treatment programs to specific operational conditions, ensuring that cooling towers operate at peak performance while minimizing environmental impacts. As technology advances, the future of cooling tower water treatment will likely involve more sophisticated chemical formulations and testing methodologies, further enhancing their efficacy and safety in industrial applications.