The Role of Plastic Additive Manufacturing in Modern Industry
Plastic additive manufacturing, commonly referred to as 3D printing, has revolutionized how we approach the design and production of plastic components. This innovative technique, which builds objects layer by layer from a digital file, has set new standards in the manufacturing industry, allowing for unprecedented levels of customization, efficiency, and sustainability.
The Basics of Plastic Additive Manufacturing
At its core, additive manufacturing involves the use of materials, often engineered plastics, that are deposited in successive layers to create a three-dimensional object. This process contrasts sharply with traditional subtractive manufacturing methods, which remove material from a solid block to produce the final part. With additive manufacturing, there is minimal waste since the material is added rather than taken away.
The most common methods of plastic additive manufacturing include Fused Deposition Modeling (FDM), Stereolithography (SLA), and Selective Laser Sintering (SLS). Each technique has its unique advantages; for example, FDM is widely used for its simplicity and cost-effectiveness, while SLA provides high precision and excellent surface finish.
Benefits of Plastic Additive Manufacturing
1. Customization and Design Freedom One of the most significant advantages of plastic additive manufacturing is its ability to produce highly customized parts. Traditional manufacturing often requires costly molds and tooling to create even minor variations in design. In contrast, additive manufacturing allows for easy adjustments to a digital model, enabling manufacturers to produce a unique part without significant additional costs.
2. Reduced Lead Times The traditional manufacturing process can be time-consuming, involving several steps from design to production. With additive manufacturing, design iterations can be rapidly tested and altered, significantly reducing the lead times associated with bringing a product to market. This rapid prototyping capability allows companies to respond to market demands quickly and efficiently.
plastic additive manufacturing
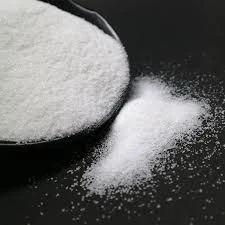
3. Material Efficiency and Sustainability Additive manufacturing generates less waste than traditional techniques since it uses only the necessary amount of material for each part. Additionally, many manufacturers are now exploring biodegradable and sustainable plastic materials for additive printing, minimizing environmental impact. This focus on sustainability aligns with the growing consumer demand for eco-friendly products.
4. Lightweight Structures Additive manufacturing excels at creating lightweight yet strong structures. This feature is particularly valuable in industries such as aerospace and automotive, where reducing weight can improve fuel efficiency and performance. Designers can employ complex geometries that are often impossible to achieve through traditional manufacturing techniques.
Challenges and Limitations
Despite its many advantages, plastic additive manufacturing also faces several challenges. Material Limitations The range of materials that can be used in additive manufacturing is still growing, but it is not as diverse as traditional manufacturing materials. While advancements are being made, certain applications may still require more robust or specific material properties than current 3D printing materials can offer.
Surface Finish and Tolerances Parts produced via additive manufacturing may not always meet the same surface finish or tight tolerances as those produced through traditional methods. However, post-processing techniques, such as sanding or coating, can address these issues, albeit at an increased cost and time requirement.
Future Trends
Looking ahead, the future of plastic additive manufacturing seems bright. Continuous advancements in technology are expected to improve the materials available, the speed of manufacturing, and the overall quality of the finished products. Innovations like multi-material printing and hybrid processes that combine additive and subtractive methods are also on the rise, promising even more versatility in production.
In conclusion, plastic additive manufacturing is poised to become a cornerstone of modern manufacturing across various sectors. Its ability to produce customized, efficient, and sustainable products aligns perfectly with the needs of today's rapidly evolving market. As technology continues to advance, it will undoubtedly play a pivotal role in shaping the future of manufacturing.