Additives Used in Plastic Manufacturing Enhancing Performance and Functionality
The modern plastic manufacturing industry has evolved significantly over the years, thanks to the incorporation of various additives designed to enhance the performance and functionality of plastic materials. Additives play a critical role in determining the properties of plastics, including their mechanical strength, thermal stability, flexibility, and resistance to environmental factors. This article explores the different types of additives used in plastic manufacturing, their functions, and their importance in producing high-quality plastic products.
Types of Additives
1. Stabilizers One of the primary additives used in plastic manufacturing are stabilizers, which are employed to enhance the durability of plastics against environmental factors such as UV radiation, heat, and moisture. For instance, UV stabilizers absorb harmful ultraviolet light, preventing it from degrading the polymer chains in plastics. This is essential for outdoor applications where plastics are exposed to sunlight for long periods.
2. Plasticizers These additives are used to increase the flexibility and workability of plastics, particularly in the case of polyvinyl chloride (PVC). Plasticizers reduce the intermolecular forces between polymer chains, resulting in a softer and more pliable material. Common plasticizers include phthalates and adipates, which are widely used in applications ranging from flexible tubing to flooring.
3. Fillers Fillers are materials added to plastics to improve properties such as strength, stiffness, and thermal conductivity while reducing costs. Common fillers include calcium carbonate, talc, and glass fibers. These additives help enhance the bulk and weight of plastic products, making them more robust without significantly increasing production costs.
4. Colorants Colorants, including pigments and dyes, are used to impart color to plastic products. They can be synthetic or natural and are an essential aspect of producing visually appealing and marketable plastic items. Effective colorants not only provide aesthetic value but also ensure that the color remains stable over time, particularly against UV radiation and heat.
5. Antioxidants Additives that prevent the degradation of plastics due to oxidation are known as antioxidants. Without these additives, plastics can become brittle and lose their tensile strength over time, especially when exposed to high temperatures. Antioxidants play a crucial role in extending the lifespan of plastic products, particularly in automotive and electrical applications.
6. Flame Retardants Safety is a paramount concern in many applications, particularly in construction and electronics. Flame retardants are added to plastics to reduce flammability and enhance fire resistance. These additives help prevent the spread of flames and reduce smoke emissions during combustion, making plastic products safer for use in critical applications.
additives used in plastic manufacturing
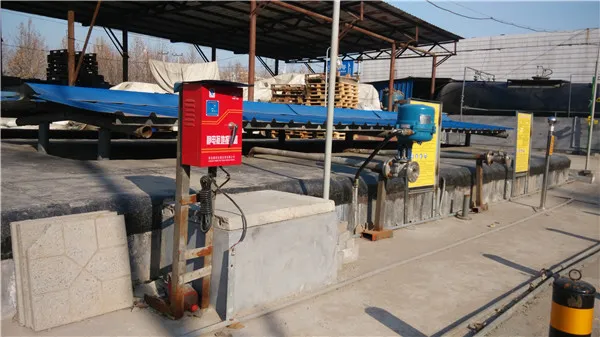
Importance of Additives in Plastic Manufacturing
The incorporation of additives in plastic manufacturing is vital for several reasons
- Improved Performance Additives enable manufacturers to tailor the properties of plastics to meet specific performance criteria for various applications. This customization is essential for industries such as automotive, construction, and consumer goods, where different performance standards are required.
- Cost Efficiency By using fillers and other cost-effective additives, manufacturers can reduce the overall material costs while still achieving desired physical and chemical properties. This is essential for maintaining competitive pricing in a global market.
- Environmental Considerations With growing concerns about sustainability, many manufacturers are turning to biodegradable additives and environmentally friendly alternatives. These innovations are crucial as the industry strives to reduce its environmental footprint and adhere to regulatory standards.
- Market Demand Consumer preferences are constantly evolving, and the demand for more specialized, high-performance plastic products is on the rise. Additives enable manufacturers to innovate and create products that meet these changing market demands.
Conclusion
In conclusion, additives used in plastic manufacturing are essential components that significantly enhance the performance, durability, and aesthetic appeal of plastic materials. As the industry continues to innovate and evolve, the development and utilization of advanced additives will play a crucial role in shaping the future of plastic products. Whether for improving safety, reducing costs, or meeting environmental standards, additives remain an integral part of the plastic manufacturing process.