Additives Used in Plastic Manufacturing
In the dynamic world of plastic manufacturing, additives play a crucial role in enhancing the properties and performance of polymer products. From improving durability to imparting color, these substances help manufacturers meet specific requirements for various applications. As the demand for innovative and high-quality plastics continues to rise, understanding the types and functions of additives becomes increasingly important.
One of the primary categories of additives is stabilizers, which are essential for protecting plastics from degradation due to environmental factors such as heat, light, and oxygen. UV stabilizers, for instance, are employed to prevent the breakdown of plastic surfaces exposed to sunlight. This is particularly important for outdoor applications where longevity is a concern. Additionally, heat stabilizers are used during processing, ensuring that the plastic maintains its integrity at high temperatures.
Another significant group of additives is plasticizers. These substances are often added to make plastics more flexible and less brittle. Commonly used in polyvinyl chloride (PVC), plasticizers work by increasing the distance between polymer chains, allowing for greater mobility and flexibility. This makes the end product suitable for applications such as flexible tubing, flooring, and various consumer goods.
Furthermore, fillers are utilized to enhance the mechanical properties and reduce production costs. Fillers, such as talc, calcium carbonate, and glass fibers, can improve strength, stiffness, and thermal stability of plastics. By incorporating fillers, manufacturers can achieve desired performance characteristics while optimizing material usage. For example, adding glass fibers can significantly enhance the tensile strength of composites, making them ideal for automotive and construction applications.
additives used in plastic manufacturing
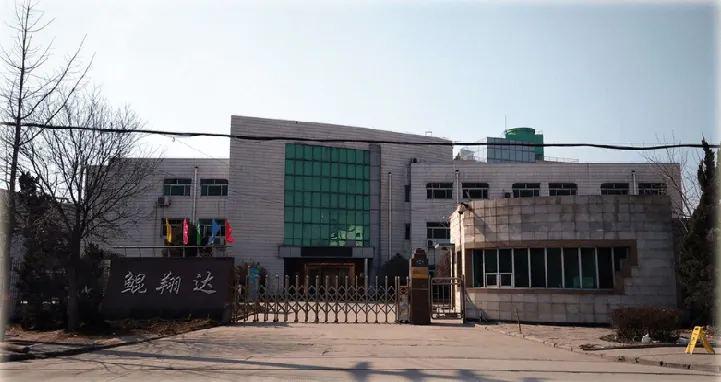
Colorants are another vital category of additives. They determine the aesthetic appeal of plastic products and can be in the form of dyes or pigments. Colorants not only provide visual appeal but also contribute to functionality, as certain pigments can offer UV protection. With the growing trend towards personalization and branding, colorants play an integral role in differentiating products in the marketplace.
Moreover, flame retardants are critical for ensuring safety in many applications, particularly in electronics and construction. These additives help reduce the flammability of plastics and minimize the spread of flames in case of a fire. Regulatory standards increasingly demand the use of flame retardants, which has led to the development of various effective formulations tailored for different materials and applications.
Lastly, as sustainability gains importance in the manufacturing arena, biodegradable additives and recycled materials are becoming more prevalent. These innovations strive to reduce the environmental impact of plastic waste while meeting consumer demands for eco-friendly products.
In conclusion, additives are indispensable in plastic manufacturing, providing a range of benefits that enhance product performance, safety, and appeal. As technology advances and sustainability becomes a greater focus, the role of these additives will continue to evolve, paving the way for the next generation of innovative plastic products.