Understanding Boiler Feed Water Chemicals Importance and Applications
Boiler feed water is a critical component in the operation of steam boilers, essential for processes across various industries including power generation, chemical manufacturing, and food processing. The quality of the feed water directly influences boiler efficiency, longevity, and the safety of operations. Therefore, the use of appropriate boiler feed water chemicals is imperative to ensure optimal performance.
Feed water must be treated before entering the boiler, as untreated water can contain impurities such as dissolved gases, minerals, and microorganisms that lead to various types of corrosion, scale formation, and fouling. Each of these issues can dramatically reduce the efficiency of the boiler and may even lead to catastrophic failures if not addressed appropriately. To mitigate these problems, several types of chemicals are used in the treatment of boiler feed water.
One of the most common chemicals used is oxygen scavengers, such as sodium sulfite or hydrazine. These compounds react with dissolved oxygen in the feed water to prevent corrosion, which can severely damage boiler components and piping systems. By eliminating oxygen, these chemicals help safeguard the integrity of steel and iron surfaces where corrosion might otherwise occur.
Another significant category of treatment chemicals includes scale inhibitors. Hard water often contains high levels of calcium and magnesium, which can precipitate as scale deposits on boiler tubes. These deposits act as insulators, leading to overheating and increased fuel consumption. Phosphates and polymers are commonly used as scale inhibitors, working by precipitating calcium and magnesium into a form that can be easily removed from the system.
boiler feed water chemicals
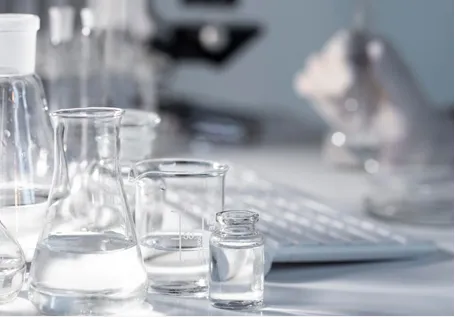
In addition to scale control, pH control agents are crucial for maintaining an optimal pH range in the boiler water, typically between 10 and 11.5. Maintaining this pH is key to minimizing corrosion. Chemicals such as sodium hydroxide or carbonate can be added to adjust the pH, ensuring a stable chemical environment for boiler operation.
Moreover, anti-foaming agents may also be included in the treatment regime. Foaming can disrupt the boiler's water-water interface, potentially leading to steam carryover, which diminishes efficiency and can introduce water into the steam system. By using silicone-based antifoams, operators can help maintain stability in the boiler operation.
Another aspect of boiler feed water treatment is the use of biocides to manage microbial growth. The presence of bacteria and other microorganisms in feed water can lead to biofouling, where biological films form on surfaces, further exacerbating resistance to heat transfer and potentially leading to other operational complications. Effective biocides, such as sodium hypochlorite or various non-oxidizing agents, are employed to control microbial populations.
In summary, the treatment of boiler feed water with appropriate chemicals is essential for ensuring the efficiency and safety of boiler operations. Oxygen scavengers, scale inhibitors, pH control agents, anti-foaming agents, and biocides all play vital roles in maintaining system integrity. Failure to implement a comprehensive feed water treatment program can lead to reduced efficiency, increased operational costs, and, ultimately, costly repairs or shutdowns. As industries continue to demand improved energy efficiency and sustainability, the importance of boiler feed water chemicals will remain a cornerstone of effective boiler operation and maintenance.