Boiler Water Chemical Treatment Ensuring Efficiency and Longevity
Boilers play a crucial role in various industries, providing steam for heating, power generation, and various manufacturing processes. However, maintaining the efficiency and longevity of a boiler system requires meticulous attention to water quality. Boiler water chemical treatment is essential to prevent issues such as scaling, corrosion, and fouling, which can lead to costly repairs and operational downtimes.
Understanding Boiler Water Chemistry
The effectiveness of a boiler largely hinges on the quality of its feedwater and the water within the boiler system. The presence of impurities such as dissolved gases, minerals, and organic matter can significantly compromise boiler performance. For instance, dissolved oxygen and carbon dioxide can lead to severe corrosion of the boiler's metal surfaces, while minerals like calcium and magnesium can precipitate as scale, hindering heat transfer and causing overheating.
Chemical Treatment Approaches
To ensure optimal boiler operation, chemical treatment programs are employed to mitigate these risks. The primary objectives of boiler water treatment are to control pH levels, prevent scale formation, and inhibit corrosion. The following are common chemical treatment methods
1. Oxygen Scavengers These chemicals, such as sodium sulfite and hydrazine, are added to the feedwater to react with oxygen, thereby preventing corrosion. By removing dissolved oxygen before it can cause damage, these scavengers help protect the integrity of the boiler system.
2. Scale Inhibitors Compounds like phosphonates and polyacrylates are introduced to prevent the precipitation of scale-forming minerals. They work by altering the crystallization process, reducing the likelihood of bond formation that leads to scale accumulation.
boiler water chemical treatment
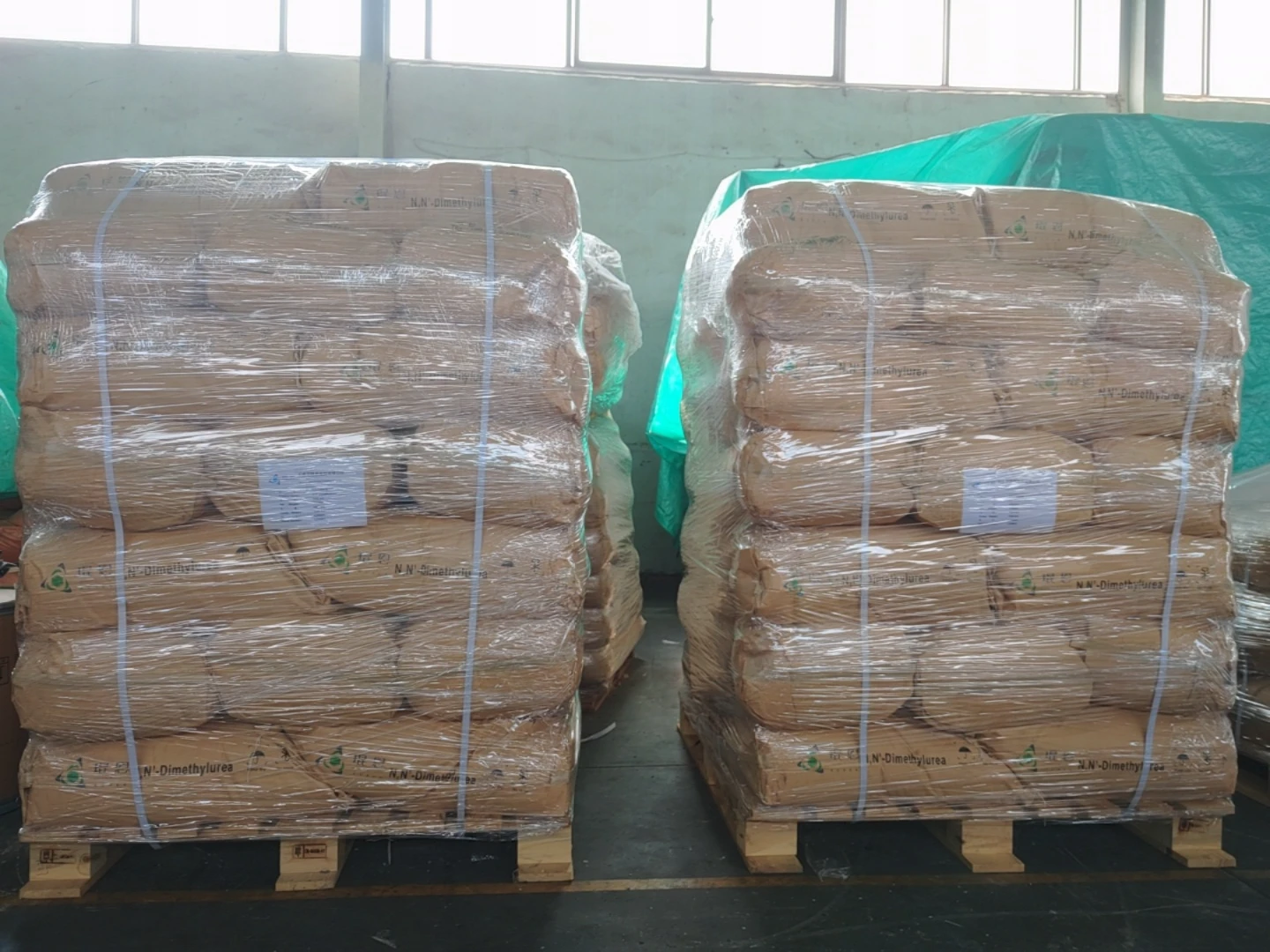
3. pH Control Agents Maintaining an appropriate pH level is critical for preventing corrosion. Alkaline substances such as sodium hydroxide or sodium bicarbonate are often used to adjust the pH in a boiler system, ensuring it remains within the optimal range (typically between 10.5 and 12.5).
4. Condensate Treatment To protect the condensate return lines and ensure system efficiency, specific chemicals are used to neutralize any acidic components formed during steam condensation. This treatment is vital for extending the life of the entire system.
Monitoring and Maintenance
The effectiveness of boiler water chemical treatment hinges on continuous monitoring and regular maintenance. Water samples must be tested routinely to gauge the levels of various parameters, including pH, conductivity, and the concentration of treatment chemicals. By analyzing these indicators, operators can adjust their treatment strategies to counter any emerging threats to boiler integrity.
Furthermore, regular blowdown processes help control the concentration of dissolved solids, thus mitigating the risks associated with scale buildup. Blowdown involves intentionally releasing a portion of water from the boiler to remove sediments and maintain a balance of minerals within the system.
Conclusion
In conclusion, boiler water chemical treatment is an indispensable aspect of boiler operation and maintenance. By implementing a robust chemical treatment program, industries can ensure efficient boiler performance while extending the lifespan of their assets. Understanding the chemistry and employing appropriate treatment methods not only safeguards against costly failures but also bolsters plant productivity and operational safety. Ultimately, investing in proper boiler water treatment is a proactive measure that pays dividends in efficiency and reliability, promoting a sustainable approach to industrial steam generation.