The Role of Chemicals Used in Boilers
Boilers play a critical role in various industries, including power generation, manufacturing, and heating systems. They convert water into steam through combustion, which is then used for a myriad of applications. However, to maintain the efficiency and longevity of these systems, the use of chemicals is essential. This article explores the types and functions of chemicals used in boilers while also discussing their importance in ensuring optimal performance.
One of the primary purposes of using chemicals in boilers is to control water chemistry. Water quality is crucial, as impurities can lead to various issues such as scaling, corrosion, or carryover of contaminants in the steam. Therefore, chemical treatments are employed to address these problems.
1. Corrosion Inhibitors
Corrosion is a significant concern in boiler systems, especially in the metal components exposed to high temperatures and pressures. Corrosion inhibitors are chemicals that help to protect the metal surfaces of the boiler. They work by forming a protective film on the metal, preventing the reaction between the metal and water or steam. Commonly used corrosion inhibitors include sodium nitrite, molybdate, and phosphates. By inhibiting corrosion, these chemicals can prolong the lifespan of boiler components, reduce maintenance costs, and improve overall reliability.
Scaling occurs when dissolved minerals in the water precipitate and accumulate on the heat transfer surfaces of the boiler. This can significantly reduce heat transfer efficiency and lead to overheating or even boiler failure. Scale inhibitors, such as polyacrylic acid or phosphonates, are added to the feedwater to prevent the formation of scale. These chemicals interfere with the crystallization process of minerals, allowing them to remain suspended in the water. By controlling scale formation, these inhibitors help maintain heat transfer efficiency and reduce energy consumption.
chemical used in boiler
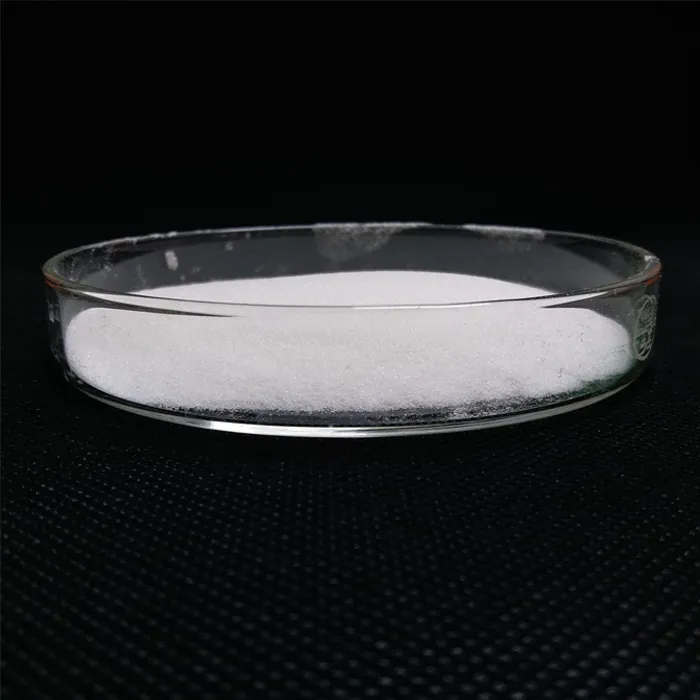
3. pH Control Agents
The pH level of boiler water is a crucial factor in preventing both corrosion and scaling. Maintaining an optimal pH level (typically between 10.5 and 11.5) helps to ensure that the water remains neutral and reduces the risk of acid-related corrosion. pH control agents, such as sodium hydroxide or ammonia, can be added to the boiler water to achieve this balance. Regular monitoring and adjustment of pH levels are essential for maintaining the integrity of the boiler system.
4. Oxygen Scavengers
Oxygen is a leading cause of corrosion in boiler systems. Oxygen scavengers, such as hydrazine or sodium sulfite, are added to the water to remove dissolved oxygen. These chemicals react with the oxygen to form non-corrosive byproducts, thereby protecting the metal surfaces. Eliminating dissolved oxygen is vital for preventing pitting and other forms of localized corrosion.
Conclusion
The use of chemicals in boiler systems is vital for ensuring efficient and safe operation. Corrosion inhibitors, scale inhibitors, pH control agents, and oxygen scavengers play crucial roles in maintaining water quality and protecting the integrity of boiler components. Proper chemical management not only enhances the performance of boilers but also extends their operational life, reduces maintenance costs, and minimizes the risk of downtime. As industries continue to rely heavily on boiler systems, the importance of effective chemical treatment will only grow, underscoring the need for diligent monitoring and management of boiler water chemistry.