Chemicals Used in Cooling Tower Water Treatment
Cooling towers are critical components in many industrial processes, serving to dissipate excess heat through the evaporation of water. However, the water utilized in these systems can be susceptible to various forms of contamination, including scale formation, corrosion, algae growth, and bacterial proliferation. Effective water treatment is essential to maintain the operational efficiency of cooling systems and to ensure environmental compliance. Several chemicals are commonly employed in cooling tower water treatment to mitigate these issues.
1. Biocides
One of the primary concerns in cooling tower water systems is the growth of biological contaminants, such as algae, bacteria, and fungi. Legionella bacteria, in particular, can pose serious health risks and should be effectively controlled. Biocides are chemical agents specifically designed to eliminate or inhibit the growth of these microorganisms. Common biocides used in cooling towers include chlorine, bromine, and various non-oxidizing biocides. Chlorine is a traditional choice due to its effectiveness and cost-efficiency, while bromine is often preferred in certain applications because of its lower volatility and higher stability over a broader pH range. Non-oxidizing biocides, such as quaternary ammonium compounds and isothiazolinones, can provide an alternative for systems that may be sensitive to oxidation.
2. Corrosion Inhibitors
Cooling tower systems often work with metallic components, which can be prone to corrosion due to the presence of dissolved oxygen and other corrosive agents in the water. Corrosion can lead to significant equipment damage, reduced efficiency, and increased maintenance costs. To combat this, corrosion inhibitors are added to the water. Common inhibitors include phosphate-based compounds, molybdate, and azole. These chemicals work by forming a protective film on the metal surfaces, thereby preventing the electrochemical reactions that lead to corrosion. It is essential to select the right corrosion inhibitor based on the specific metallurgy of the system and the water chemistry.
chemicals used in cooling tower water treatment
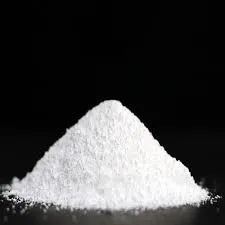
Scaling is another prevalent issue in cooling towers, particularly in areas with hard water. Mineral deposits can accumulate on heat exchange surfaces, reducing efficiency and increasing energy consumption. To prevent scale formation, scale inhibitors are introduced into the water. These are often phosphate or polymer-based substances that interfere with the crystallization process of scale-forming minerals such as calcium carbonate and magnesium silicate. Effective use of scale inhibitors can prolong the life of the cooling system and reduce the frequency of chemical cleaning.
4. pH Adjusters
The pH level of cooling tower water is critical for the overall effectiveness of water treatment chemicals. A balanced pH ensures optimal performance of biocides, corrosion inhibitors, and scale inhibitors. If the pH is either too low or too high, it can lead to excessive corrosion or scaling, respectively. Common pH adjusters include acetic acid for lowering pH and sodium hydroxide or sodium bicarbonate for raising it. Regular monitoring and adjustment of pH levels are crucial to maintaining an efficient water treatment program.
5. Antifoams
Foam formation in cooling towers is often a result of surface-active agents present in the water, which can be caused by biological activity or chemical additives. Excessive foam can significantly impair heat transfer efficiency and oxygen transfer rates. Antifoams, typically silicone or non-silicone based, are employed to reduce foam formation and ensure smooth operation of the cooling tower.
Conclusion
The effective treatment of cooling tower water is vital for optimizing system performance and ensuring environmental compliance. By utilizing a combination of biocides, corrosion inhibitors, scale inhibitors, pH adjusters, and antifoams, industrial facilities can mitigate the risks associated with scale formation, corrosion, and microbial growth. As regulations around water use and treatment continue to evolve, operators must remain vigilant in their management practices, continuously monitoring water chemistry and adjusting chemical treatments as necessary. The right combination of chemicals, tailored to the specific needs of the cooling system, will contribute significantly to its efficiency and longevity.