Chemical Treatment of Cooling Tower Water Ensuring Efficiency and Longevity
Cooling towers are a crucial component in various industrial processes, particularly in power plants, chemical manufacturing, and HVAC systems. They help dissipate heat by transferring it from cooling water to the environment, but maintaining the efficiency and longevity of these towers requires careful management of the water used. One effective way to achieve this is through chemical treatment, which helps to control scale, corrosion, and microbiological growth.
The Importance of Water Quality in Cooling Towers
Cooling towers operate on the principle of evaporative cooling, where water absorbs heat from equipment and, in turn, loses some of this water through evaporation. The makeup water used in these systems often contains dissolved minerals, organic matter, and microorganisms that can impact the tower’s performance. Poor water quality can lead to several issues, including scaling, corrosion of metal components, and biofouling, which can reduce the efficiency of heat exchange processes and increase maintenance costs.
Common Issues in Cooling Tower Water
1. Scaling The collection of minerals such as calcium and magnesium in cooling water can lead to the formation of scale on heat exchange surfaces. This not only reduces the efficiency of heat transfer but also increases energy consumption and operational costs. 2. Corrosion Chemical reactions between water and the materials used in the cooling tower system can lead to corrosion. This is particularly problematic in metal components, where corrosion can result in leaks, equipment failure, and extensive downtime.
3. Biological Growth Cooling towers are susceptible to the growth of algae, bacteria, and other microorganisms due to the warm, moist environment. Biofilms can form on surfaces, insulating them against heat transfer, while pathogens pose health risks to workers and surrounding communities.
Chemical Treatment Solutions
chemical treatment of cooling tower water
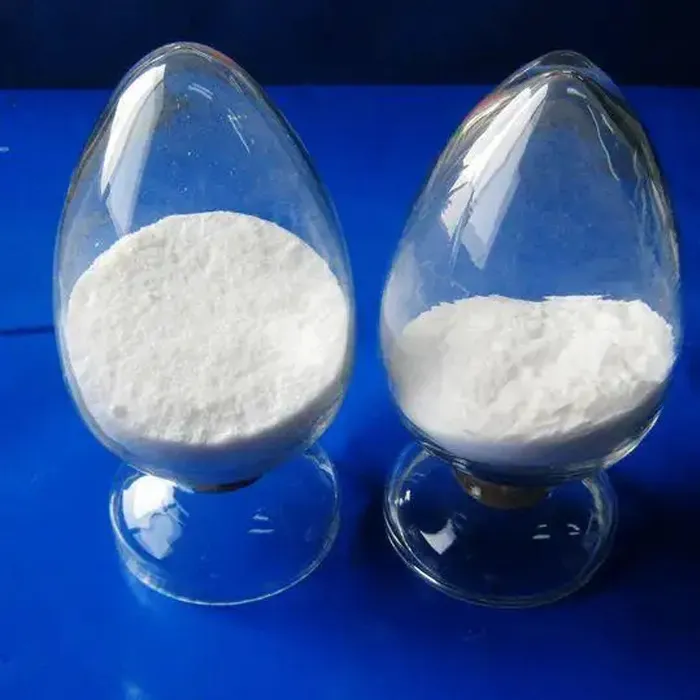
To address these issues, chemical treatment programs must be employed, often tailored to the specific requirements of the facility and the characteristics of the water source. Here are some common chemical treatments used in cooling tower systems
1. Scale Inhibitors These chemicals help to prevent the deposition of scale-forming minerals in the cooling system. Common scale inhibitors include polyphosphates and polymers, which work by either chelating or dispersing scale-forming ions, thus keeping them in solution and preventing them from settling on surfaces.
2. Corrosion Inhibitors Protecting metal components from corrosion is vital for maintaining equipment integrity. Various corrosion inhibitors, such as nitrites, phosphates, or molybdates, can be added to the system to create a protective film on metal surfaces, reducing the rate of corrosion.
3. Biocides To combat biological fouling, chemical biocides such as chlorine, bromine, and isothiazolinones are employed. These substances kill harmful microorganisms and help maintain a clean water system. It is essential, however, to use these chemicals judiciously to minimize environmental impact and avoid creating resistant strains of bacteria.
4. pH Adjusters The pH level of the cooling water can significantly impact both scaling and corrosion rates. By using pH adjusters (such as sulfuric acid or sodium hydroxide), operators can maintain optimal pH levels that reduce the risk of both issues.
Conclusion
The chemical treatment of cooling tower water is a vital aspect of industrial water management that contributes to operational efficiency and longevity. By implementing a comprehensive chemical treatment program, facilities can address scaling, corrosion, and biological growth effectively, which leads to improved heat transfer efficiency, decreased maintenance costs, and enhanced system reliability.
Ultimately, investing in chemical treatments not only ensures the optimal performance of cooling towers but also promotes sustainability by reducing water waste and energy consumption. Regular monitoring and adjustments to the treatment program based on water quality assessments will help maintain these systems in peak condition, safeguarding both productivity and environmental compliance.