The Role of Chemicals in Cooling Towers Enhancing Efficiency and Longevity
Cooling towers are essential components in many industrial processes, providing a cost-effective way to remove excess heat. These systems use water to transfer heat from machinery or other process fluids into the atmosphere, thereby keeping equipment operating at safe temperatures. However, the effectiveness of cooling towers can be significantly impacted by various factors, including the quality of the water they use. This is where chemicals come into play. In this article, we will explore the various chemicals used in cooling towers, their purposes, and the importance of maintaining a balanced approach for optimal performance.
The Importance of Water Treatment in Cooling Towers
Cooling towers operate using large volumes of water, which can become contaminated with scale, corrosion, and biological growth over time. Inadequate treatment can lead to decreased efficiency, increased energy consumption, and potential damage to the system. Therefore, to maintain effective heat exchange and prolong the system's lifespan, it is crucial to use appropriate water treatment chemicals.
Common Chemicals Used in Cooling Towers
1. Biocides One of the major challenges in cooling towers is the growth of algae, bacteria, and other microorganisms. Biocides, such as chlorine, bromine, and non-oxidizing biocides, are used to control these biological contaminants. These chemicals help prevent biofilm formation, which can inhibit heat transfer efficiency and clog pipes. Regular monitoring and dosing of biocides are essential to ensure their effectiveness without harming the environment.
2. Corrosion Inhibitors The metals in cooling towers can corrode over time due to exposure to water, oxygen, and various chemicals. Corrosion inhibitors, such as zinc, molybdate, and phosphate, are added to the cooling water to create a protective barrier on metal surfaces, preventing rust and extending the lifespan of the equipment. The selection of the appropriate corrosion inhibitor depends on the materials used in the cooling system and the operating conditions.
3. Scale Inhibitors As water evaporates in the cooling tower, dissolved minerals such as calcium and magnesium can concentrate and precipitate, forming scale. Scale buildup can impair heat transfer and increase energy costs. Scale inhibitors, including polyacrylic acid and phosphonates, are employed to prevent mineral deposits from forming. These additives work by altering the crystal growth of scale-forming minerals, keeping them suspended in the water instead.
chemical used in cooling tower
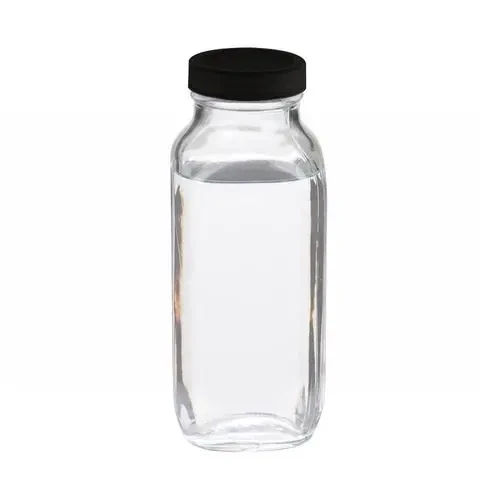
4. pH Adjusters Maintaining the proper pH balance in cooling water is crucial for optimal performance. Chemicals such as sulfuric acid or sodium hydroxide are used to adjust and stabilize pH levels. A balanced pH helps to enhance the effectiveness of other treatment chemicals, reduce corrosion rates, and prevent scaling.
5. Dispersants To further improve water quality, dispersants are used to keep suspended particles, such as silt and debris, evenly distributed in the water. This prevents the accumulation of particles that can lead to fouling and clogging in the system.
Balancing Chemical Use and Environmental Impact
While the use of chemicals in cooling towers is essential for their effective operation, it is equally important to consider their environmental impact. The introduction of chemicals into the water system can pose risks to aquatic life and the surrounding ecosystem. Thus, many industries are now adopting more sustainable practices, including the use of biodegradable chemicals, optimizing dosing strategies, and implementing closed-loop water systems to minimize discharge.
Additionally, regular monitoring and maintenance are vital to ensure that chemical concentrations remain within safe limits. Employing automated monitoring systems can help in maintaining real-time data, allowing facility managers to make informed decisions regarding chemical dosing and treatment strategies.
Conclusion
In conclusion, the right selection and management of chemicals in cooling towers are crucial for maintaining their efficiency and longevity. Biocides, corrosion inhibitors, scale inhibitors, pH adjusters, and dispersants each play a vital role in ensuring optimal performance. However, it is imperative to balance chemical use with environmental considerations to minimize potential impacts. As industries continue to evolve, so will the strategies and chemicals used in cooling towers, ultimately leading to more efficient and sustainable operations. By understanding and implementing effective water treatment practices, we can enhance cooling tower performance while safeguarding our environmental resources.