Understanding Chemical Dosing in Cooling Towers
Cooling towers are essential components in various industrial and commercial operations, providing efficient heat exchange for large systems needing cooling. To maintain their optimal performance and prevent issues such as scaling, corrosion, and biological growth, appropriate chemical dosing is crucial. This article explores the significance of chemical dosing in cooling towers, the types of chemicals used, and best practices for effective management.
Importance of Chemical Dosing
Chemical dosing in cooling towers serves several critical functions
1. Scale Control As water evaporates in cooling towers, dissolved minerals like calcium and magnesium concentrate, leading to scaling on heat exchange surfaces. Chemical scale inhibitors, such as phosphonates, are added to the water to prevent mineral precipitation and maintain efficiency.
2. Corrosion Prevention The metal components of cooling towers are susceptible to corrosion, which can lead to leaks, inefficiencies, and costly repairs. Corrosion inhibitors, often designed with specific metal interactions in mind, are used to form protective films on surfaces, minimizing damage.
3. Biological Control Cooling towers can become breeding grounds for bacteria and algae, which not only reduce efficiency but can also pose health risks (e.g., Legionella pneumophila). Biocides, including chlorine, bromine, and non-chlorine alternatives, are dosed to manage biological growth.
4. pH Control Maintaining an appropriate pH level is vital for chemical performance and system integrity. pH adjusters, such as sodium hydroxide or sulfuric acid, are used to keep the water within the desirable range (typically between 6.5 and 8.5) to optimize chemical efficacy and system performance.
Types of Chemicals Used in Cooling Towers
The selection of chemicals for dosing depends on the specific requirements of the cooling system. Here are some common types of chemicals
- Scale Inhibitors These include phosphonates, which disrupt crystal formation and help keep minerals in solution.
- Corrosion Inhibitors Compounds like sodium molybdate or nitrites are often used depending on the metallurgy of the cooling system.
cooling tower chemical dosing pdf
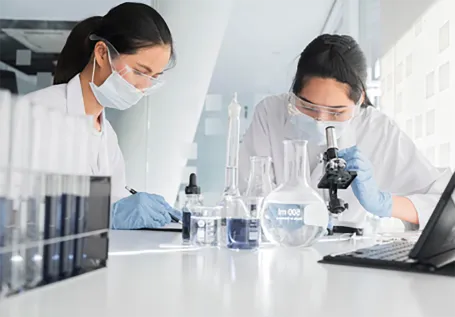
- Biocides Chlorine and bromine are traditional choices, while glutaraldehyde and quaternary ammonium compounds serve as alternative biocides with different environmental impacts.
.
- pH Adjusters Sodium hydroxide (for raising pH) and sulfuric acid (for lowering pH) are commonly used to maintain the water's acidity.
Best Practices for Chemical Dosing
To ensure effective chemical dosing in cooling towers, several best practices should be followed
1. Regular Water Testing Frequent testing of water quality is essential to determine the concentration of scaling and corrosion potential, as well as microbial growth. Parameters to monitor include conductivity, pH, and bacterial counts.
2. Automated Dosing Systems Implementing automated chemical dosing systems can enhance precision and reduce human error. These systems can adjust chemical feed rates based on real-time water quality analysis.
3. Proper Training Personnel involved in managing cooling towers should be trained in chemical handling and dosing practices. Understanding the properties and reactions of chemicals is crucial for safety and effectiveness.
4. Documentation and Monitoring Keeping detailed records of chemical usage, water quality tests, and maintenance activities helps identify trends and allows for informed adjustments in chemical dosing.
5. Environmental Considerations Selecting chemicals with lower environmental impacts is increasingly important. Non-chlorine biocides and biodegradable inhibitors can help minimize ecological risks.
Conclusion
Chemical dosing in cooling towers is not merely an operational requirement; it is a critical management practice that ensures efficiency, longevity, and safety. By utilizing appropriate chemicals and adhering to best practices, industries can enhance the performance of their cooling systems while mitigating environmental impacts. As technology advances, integrating automated systems and eco-friendly practices will be essential for the future of cooling tower management. Proper attention to chemical dosing today leads to more sustainable and effective cooling solutions tomorrow.