Chemical Treatment of Cooling Towers Ensuring Efficiency and Longevity
Cooling towers are essential components in various industrial processes and commercial buildings, providing effective heat rejection through the evaporation of water. However, like any mechanical system, they require regular maintenance and careful management to ensure optimal performance. One of the most critical aspects of cooling tower maintenance is chemical treatment, which involves the use of specific chemicals to manage water quality, prevent corrosion, scale buildup, and biological growth.
The Importance of Chemical Treatment
The primary function of chemical treatment in cooling towers is to maintain water quality. During operation, cooling towers constantly cycle water that absorbs heat from industrial processes and returns it back to the system. This cycle, while necessary, can lead to concentration of impurities present in the water, such as minerals and organic matter. Without proper treatment, these impurities can lead to significant operational issues, including decreased efficiency, system failures, and increased energy consumption.
Common Challenges
1. Corrosion The metals used in cooling tower systems, such as steel and aluminum, are susceptible to corrosion when exposed to water mixed with certain chemical agents. Corrosion can lead to leaks, structural damage, and ultimately, equipment failure.
2. Scaling Hard water contains minerals like calcium and magnesium, which tend to precipitate and form scale deposits on heat exchange surfaces. Scaling reduces the heat transfer efficiency and can lead to overheating and mechanical failures.
3. Biological Growth Cooling towers can become breeding grounds for algae, bacteria, and other microorganisms. Biofilm formation can obstruct water flow, diminish heat transfer efficiency, and pose health risks, such as the spread of Legionnaires’ disease, a severe form of pneumonia caused by Legionella bacteria.
Key Chemical Treatments
To combat these challenges, cooling tower operators often employ a variety of chemical treatments
1. Corrosion Inhibitors These chemicals form a protective film on metal surfaces, preventing corrosive elements from causing damage. Common corrosion inhibitors include phosphates, chromates, and molybdates. Selecting the right inhibitor depends on the specific metallurgy of the cooling system and the water chemistry.
cooling tower chemical treatment
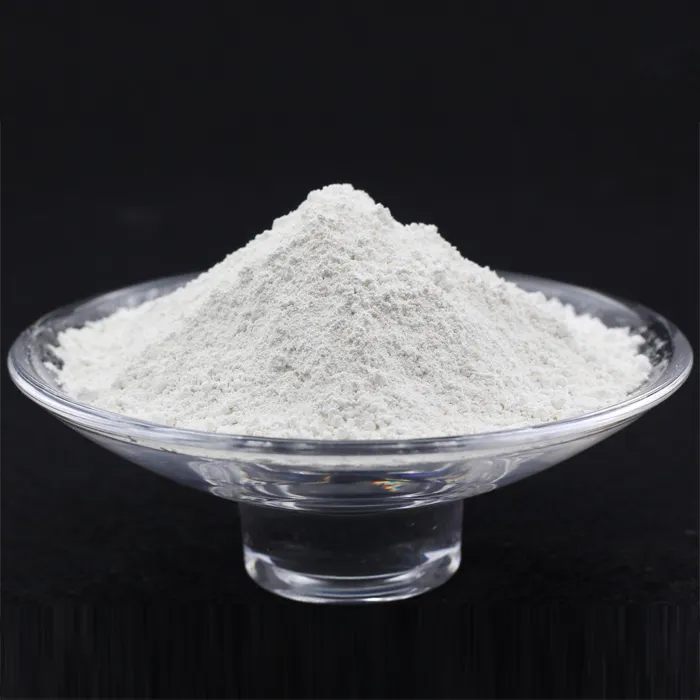
2. Scale Inhibitors Scale inhibitors, such as phosphonates and polyacrylic acids, work by disrupting the crystallization process of scale-forming minerals. This prevents them from depositing on the surfaces of the cooling tower and heat exchangers, thus maintaining efficiency.
3. Biocides Biocides are crucial in controlling microbial growth within cooling systems. They can be classified into oxidizing and non-oxidizing types. Oxidizing biocides, like chlorine and bromine, work effectively against a broad spectrum of microorganisms, while non-oxidizing biocides, such as isothiazolone, offer specific targeted treatment. Regular monitoring and dosing are vital to ensure the survival of beneficial microorganisms while keeping harmful ones in check.
Best Practices for Chemical Treatment
Implementing an effective chemical treatment program involves several best practices
1. Regular Water Testing Frequent testing of water chemistry helps identify issues before they become severe. Parameters to monitor include pH, conductivity, total dissolved solids (TDS), and specific concentrations of scale-forming and corrosive agents.
2. Proper Dosing Accurate chemical dosing is essential. Overdosing can lead to environmental harm and additional costs, while underdosing compromises system integrity. Automated treatment systems can help ensure that the right concentrations are maintained continuously.
3. Maintaining Records Keeping detailed records of water tests, chemical usage, and system maintenance can aid in troubleshooting and improving the treatment process over time.
4. Professional Consultation Working with water treatment professionals can provide insights into the most effective strategies tailored to specific cooling tower designs and local water conditions.
Conclusion
The chemical treatment of cooling towers is a crucial step in maintaining operational efficiency, safety, and longevity. By implementing a well-planned chemical management strategy that focuses on corrosion control, scale prevention, and biological treatment, operators can significantly reduce downtime, enhance energy efficiency, and extend the lifespan of their cooling systems. Regular monitoring, proper dosing, and professional consultation can lead to a more effective and efficient cooling tower operation, ultimately contributing to a more sustainable industrial practice.