The Role of Anti-Static Additives in Plastic Materials
In the modern world, plastics are ubiquitous materials utilized across various industries, from packaging to electronics. One significant challenge associated with plastic materials is their propensity to accumulate static electricity. This static charge can lead to costly problems, including dust attraction, material handling difficulties, and equipment malfunction. To mitigate these issues, anti-static additives play a vital role in enhancing the performance of plastic products.
Understanding Static Electricity in Plastics
Plastics, by their nature, are insulative materials. When they are rubbed against another material or come into contact with similar surfaces, they can become electrically charged. This static charge can cause two main issues first, it can attract dust and other particulates, leading to cleanliness problems, especially in industries such as electronics and cleanrooms; second, it can result in electrostatic discharge (ESD), which can damage sensitive electronic components.
Types of Anti-Static Additives
Anti-static additives are substances incorporated into plastic materials to reduce their surface resistivity and minimize static charge buildup
. These additives can be broadly categorized into two types primary and secondary agents.1. Primary Anti-Static Additives These are often surfactants or conductive polymers that provide immediate anti-static effects by forming a conductive layer on the surface of the plastic. They reduce surface resistivity and dissipate electrostatic charges effectively. Common primary agents include ethylene glycol, glycerol, and quaternary ammonium compounds, which can be mixed with polymers during the manufacturing process.
2. Secondary Anti-Static Additives These additives work differently; rather than providing immediate anti-static properties, they modify the material's properties over time. Secondary additives often include carbon black, metal powders, or other conductive fillers that create a conductive network within the plastic matrix. This allows static electricity to dissipate more effectively over the lifespan of the product.
anti static additives for plastic
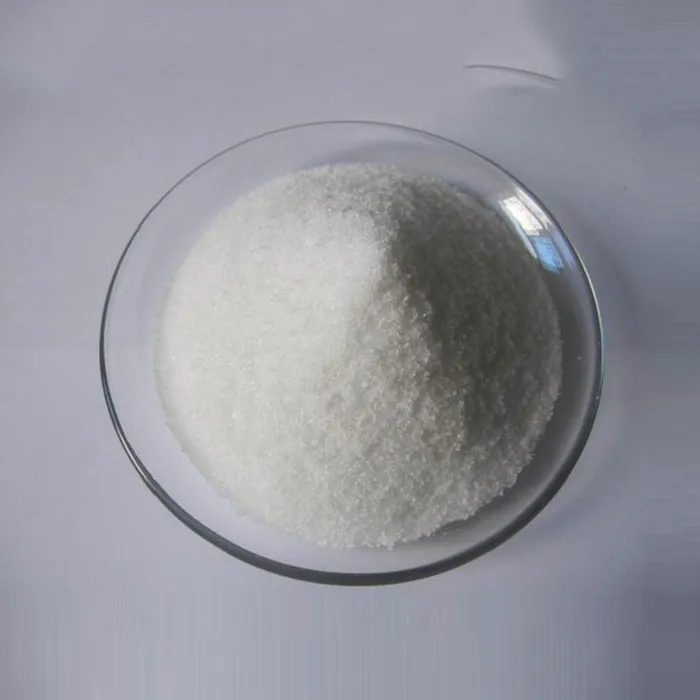
Benefits of Using Anti-Static Additives
The incorporation of anti-static additives in plastics offers several benefits. First and foremost, it significantly reduces the risk of static-related issues, enhancing safety in environments where flammable materials are present. In the electronics industry, the use of anti-static materials is crucial to ensure the integrity of components and prevent costly damages due to ESD.
Moreover, anti-static additives help maintain the cleanliness of surfaces by reducing dust attraction. This is particularly essential in cleanroom settings where even minor contaminants can compromise product quality. By minimizing static buildup, these additives contribute to better performance and enhanced durability of plastic products.
Application Across Industries
Various industries leverage anti-static additives in their plastic formulations to achieve specific performance criteria. In the packaging sector, anti-static additives are often used in containers and films to protect sensitive products. In the automotive and aerospace industries, these additives help prevent static build-up in fuel lines and electronic systems. Similarly, in medical devices, anti-static properties are essential to ensure that equipment operates correctly without interference from static charges.
Conclusion
The use of anti-static additives in plastics is a critical factor in overcoming the challenges posed by static electricity. By understanding and applying these additives, manufacturers can produce high-quality plastic products that meet stringent performance standards across multiple industries. As technology advances, the development of more efficient and effective anti-static solutions will continue to enhance the safety, cleanliness, and reliability of plastic materials in our daily lives.