Understanding PQC and CQ10 A Deep Dive into Their Significance in Today's World
In contemporary discussions surrounding quality management and operational excellence, the terms PQC (Process Quality Control) and CQ10 (Continuous Quality Improvement) frequently arise. These concepts play a pivotal role in ensuring that organizations not only meet but exceed customer expectations in an increasingly competitive environment. To grasp their full significance, it is essential to understand their definitions, applications, and benefits.
What is PQC?
PQC, or Process Quality Control, revolves around systematically monitoring and controlling a process to ensure that it operates at its full potential. It involves various statistical techniques that help identify variations in a process, enabling organizations to maintain quality standards. The core aim of PQC is to minimize process variability and enhance efficiency while ensuring that products meet quality specifications consistently.
PQC is often employed in manufacturing industries, where maintaining consistent quality is critical. By using tools such as control charts, process mapping, and performance metrics, organizations can pinpoint defects and inefficiencies early in the production cycle. This proactive approach not only saves costs associated with rework and scrap but also boosts customer satisfaction by delivering high-quality products reliably.
What is CQ10?
On the other hand, CQ10, or Continuous Quality Improvement, is a broader philosophy focused on the ongoing enhancement of products, services, and processes. Unlike PQC, which often targets specific processes, CQ10 adopts an organization-wide perspective, ensuring that continuous enhancement becomes ingrained in the company culture.
pqq cq10
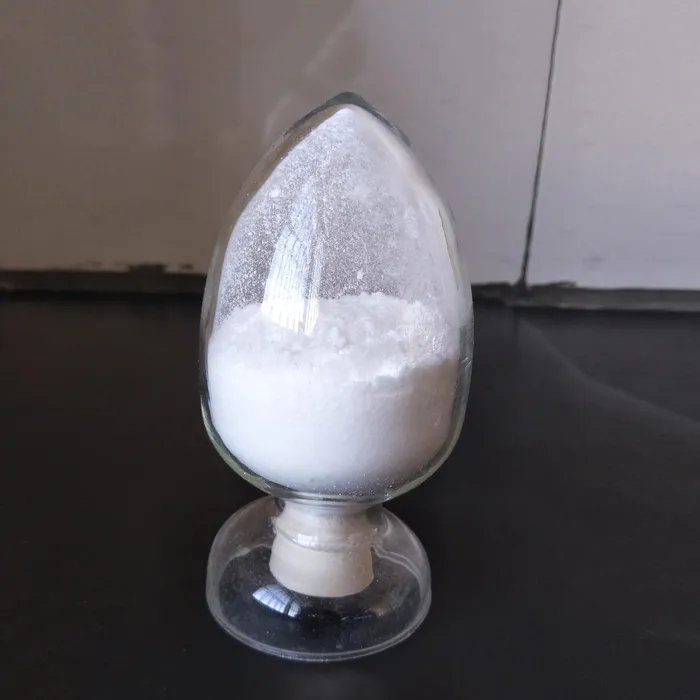
CQ10 involves the systematic evaluation of processes and practices, followed by interventions aimed at improving them. Techniques such as Plan-Do-Check-Act (PDCA) cycles, Six Sigma, and Total Quality Management (TQM) are common methodologies that underpin continuous quality improvement efforts. CQ10 encourages a culture of collaboration, where employees at all levels are empowered to contribute to quality initiatives.
The Interconnection Between PQC and CQ10
PQC and CQ10, while distinct, are not mutually exclusive. In fact, an effective quality management system often integrates both to achieve optimal results. PQC provides a robust framework for controlling processes, while CQ10 drives the continuous evolution of these processes over time. Together, they form a comprehensive approach to quality management that equips organizations to adapt to changing market demands and technological advancements.
For instance, during a PQC assessment, an organization may find that a specific production line experiences variations leading to defects. By implementing PQC practices, they can stabilize the process. Simultaneously, through CQ10 initiatives, the organization can explore innovative ways to improve the design of the product or implement new technologies that enhance efficiency, ensuring that the quality improvements are sustainable in the long run.
Benefits of PQC and CQ10
The benefits of implementing PQC and CQ10 are manifold. Organizations that prioritize these methodologies often see enhancements in efficiency, reduced operational costs, higher customer satisfaction, and improved employee morale. A commitment to quality also strengthens an organization’s reputation and competitive advantage in the marketplace.
In conclusion, PQC and CQ10 are essential pillars of modern quality management that enable organizations to navigate the complexities of today’s business environment. By embracing both process control and continuous improvement, companies can not only meet but exceed the expectations of their customers, positioning themselves for long-term success. As industries evolve, the importance of integrating these concepts becomes increasingly clear, making them indispensable tools for any organization aiming to thrive in a dynamic landscape.