The Role of Plastic Fillers in Modern Manufacturing
Plastic fillers, often referred to as additives, play a pivotal role in the manufacturing of a myriad of products across various industries. These substances are incorporated into plastics to enhance their properties, improve performance, and reduce production costs. This article explores the significance, types, and benefits of plastic fillers in modern manufacturing practices.
Plastic fillers are materials added to resins during the manufacturing process to modify physical and chemical properties. They can be categorized into several types, including inorganic fillers such as talc, calcium carbonate, and mica, and organic fillers such as wood flour or fibers. Each type of filler imparts specific characteristics to the final plastic product, making them suitable for a wide range of applications.
One primary function of plastic fillers is to improve the mechanical strength and durability of plastics. For instance, the addition of talc can enhance the rigidity and impact resistance of polypropylene, making it an excellent choice for automotive components. Similarly, calcium carbonate is widely used to improve the tensile strength and thermal stability of various plastic formulations. By incorporating these fillers, manufacturers can produce materials that withstand harsh conditions and extend the lifespan of products.
Another significant benefit of plastic fillers is their ability to reduce production costs. Fillers are often less expensive than the resins they replace, providing economic advantages to manufacturers. For example, plastics filled with calcium carbonate can reduce the overall material costs while maintaining desirable physical properties. This cost-effectiveness is particularly beneficial in industries such as packaging, automotive, and construction, where cost management is critical to competitiveness.
plastic fillers
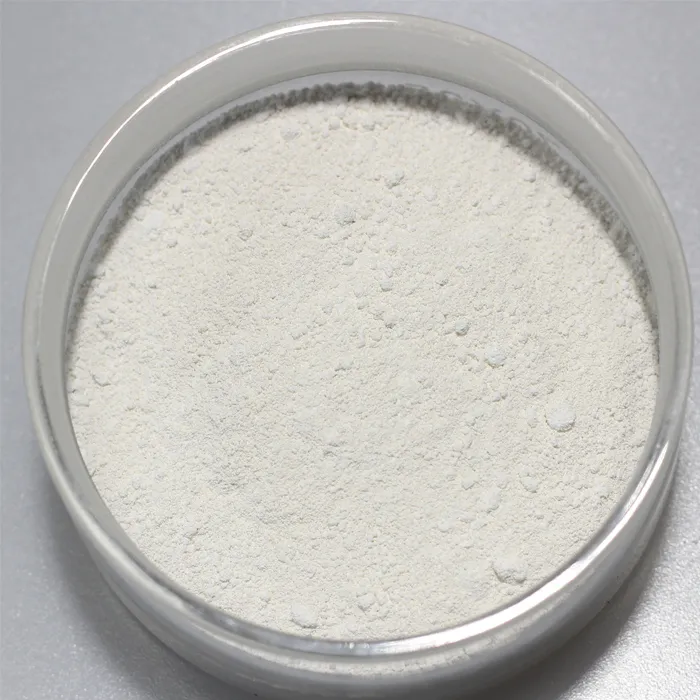
Plastic fillers also contribute to improved processing characteristics. The inclusion of fillers can enhance the flow and viscosity of the polymer melt, making it easier to process through various manufacturing techniques such as injection molding and extrusion. Additionally, certain fillers can reduce the melt temperature of plastics, leading to energy savings during processing, which is increasingly important in today's environmentally conscious manufacturing landscape.
Moreover, fillers can also facilitate improved thermal and electrical properties. For instance, the use of conductive fillers can create plastics that exhibit electrical conductivity, making them suitable for applications in electronics and electromagnetic interference (EMI) shielding. On the other hand, fillers like glass fibers enhance thermal stability and flame resistance, making plastics safe for applications in construction and home appliances.
However, it is essential to consider the environmental implications of using plastic fillers. With the increasing focus on sustainability, manufacturers need to evaluate the ecological footprint of fillers and seek alternatives that align with green practices. Biodegradable fillers, made from natural sources, are gaining popularity as companies strive to reduce their reliance on petroleum-based products. The incorporation of such sustainable fillers not only satisfies consumer demand for eco-friendly products but also adheres to stricter regulations and standards.
In conclusion, plastic fillers play an indispensable role in modern manufacturing, enhancing the performance and cost-effectiveness of plastic products. As industries continue to evolve, the demand for innovative fillers that improve sustainability while maintaining product quality will only increase. Understanding the properties and applications of various fillers will help manufacturers optimize their processes and meet the challenges of a dynamic market. Thus, the strategic use of plastic fillers will remain a cornerstone of efficient and effective production in the plastics industry.