Common Plastic Additives Enhancing Performance and Durability
Plastics have become an integral part of modern life, offering versatility, durability, and a wide range of applications. However, the raw polymers used to manufacture plastics often require various additives to enhance their properties and performance in specific applications. These additives can improve processing, provide stability, enhance aesthetics, and increase functionality. Here, we will explore some common plastic additives and their roles in the plastics industry.
1. Plasticizers
Plasticizers are one of the most frequently used additives in the production of flexible plastics, particularly polyvinyl chloride (PVC). These substances reduce the viscosity of the polymer, making it easier to process and mold, while also imparting flexibility to the final product. Common plasticizers, like phthalates, are widely utilized in products such as vinyl flooring, wall coverings, and packaging materials. Nonetheless, due to health concerns associated with some plasticizers, including phthalates, the industry has been looking for safer alternatives.
2. Stabilizers
Stabilizers are crucial for protecting plastics from degradation caused by exposure to heat, light, and oxygen. Without stabilizers, plastics can become brittle or discolored, resulting in diminished mechanical performance and shorter service life. UV stabilizers, for example, are essential for outdoor applications where exposure to sunlight can be detrimental. Metal stearates and chlorinated paraffins are often added to stave off thermal degradation during manufacturing processes, ensuring that the plastic maintains its integrity during production and usage.
3. Fillers
common plastic additives
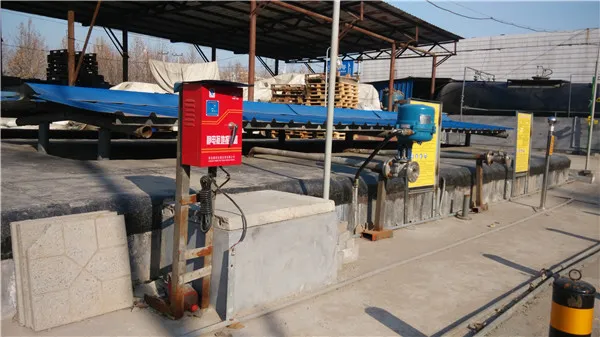
Fillers are materials added to plastics to enhance their physical properties, reduce production costs, and improve performance characteristics. Common fillers include calcium carbonate, talc, and glass fibers. These fillers can reinforce the plastic, making it stronger and more rigid, which is particularly useful in applications requiring enhanced strength, such as automotive parts and construction materials. Moreover, fillers can enhance the thermal and electrical properties of plastics, making them suitable for a broader range of applications.
4. Flame Retardants
Flame retardants are additives that decrease the flammability of plastic products, making them safer for use in various environments. These additives can be classified as either halogenated or non-halogenated. Halogenated flame retardants work by releasing hydrogen halides when exposed to heat, which interferes with combustion. Non-halogenated alternatives are gaining popularity due to stricter regulations regarding halogenated substances and their environmental impact. Flame retardants are commonly used in electronics, furniture, and construction materials to meet safety standards.
5. Colorants
Colorants, including pigments and dyes, enhance the aesthetics of plastic products. They can provide vibrant colors, improve opaqueness, and even impart special effects such as metallic or pearlescent finishes. The choice of colorant depends on the desired application and the properties of the base polymer. For example, certain pigments are designed to withstand UV light to prevent fading and maintain the product's appearance over time.
Conclusion
The use of plastic additives plays a crucial role in the functionality and performance of plastic products. From improving flexibility and durability to enhancing safety and aesthetics, additives contribute to a wide array of properties that meet consumer demands and regulatory requirements. As the industry evolves and faces challenges related to sustainability and health regulations, the development of novel, eco-friendly additives will be essential to ensure the continued viability of plastic materials in our everyday lives. Understanding these additives and their implications is vital for manufacturers, consumers, and policymakers alike in navigating the future of plastics.