Understanding Fillers in Polymers Enhancing Performance and Cost-Effectiveness
Polymers are ubiquitous in modern materials science, playing a critical role in a diverse array of applications, from everyday household items to advanced engineering solutions. However, with the growing demand for performance, durability, and cost-effectiveness, the incorporation of fillers into polymer matrices has become increasingly important. Fillers are substances added to polymer formulations to enhance their properties, modify performance, or reduce manufacturing costs. This article explores the nature of fillers, their types, and their impact on polymer properties.
What Are Fillers?
Fillers can be defined as inert substances added to a polymer matrix to improve its physical and mechanical properties without significantly altering its fundamental characteristics. They can be used to modify various aspects of polymers, including strength, stiffness, thermal stability, and overall cost. Fillers can be categorized into two main types
1. Reinforcing Fillers These are high-strength materials that provide enhanced mechanical properties to polymers. Common examples include glass fibers, carbon black, and silica. Reinforcing fillers are primarily used in composite materials, where they significantly increase the tensile strength and rigidity of the polymer.
2. Non-Reinforcing Fillers Unlike reinforcing fillers, non-reinforcing fillers typically serve to reduce costs and improve processing ease rather than enhance mechanical strength. Examples include calcium carbonate, talc, and clay. These fillers can also enhance certain properties, such as thermal conductivity or opacity, depending on the specific application.
Benefits of Using Fillers in Polymers
The incorporation of fillers into polymers offers numerous advantages. One of the primary benefits is cost reduction. By adding inexpensive filler materials, manufacturers can lower the overall production costs of polymer products while still meeting performance requirements. This is particularly beneficial in industries where large quantities of materials are needed, such as in packaging and automotive manufacture.
what are fillers in polymers
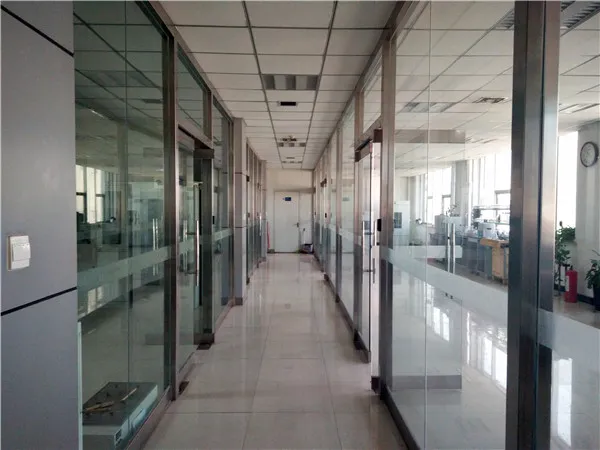
Fillers can also enhance the mechanical properties of polymers. For instance, the addition of glass fibers can increase the tensile strength and impact resistance of thermoplastic materials, making them suitable for demanding applications. Furthermore, fillers can improve thermal and electrical properties, facilitating the development of materials for specialized uses, such as electronics or automotive components.
Another significant advantage is the modification of processing characteristics. Fillers can improve the flow properties of polymers during manufacturing processes such as extrusion or injection molding, allowing for more efficient production methods and reducing energy consumption.
Applications of Filled Polymers
Filled polymers find applications across various industries. In the automotive sector, filled polypropylene is widely used in the production of dashboard components due to its lightweight and enhanced strength. In construction, filled composites are utilized for cladding and insulation materials, where enhanced mechanical properties and thermal insulation are crucial.
In consumer products, fillers are often used in plastics to provide desired textures or aesthetics. For instance, talc is commonly added to polyethylene products to improve opacity and surface finish. Additionally, in electronics, filled polymers can serve as effective insulators, with additives that enhance thermal conductivity and prevent overheating.
Conclusion
In summary, fillers play a vital role in enhancing the performance, durability, and cost-effectiveness of polymer materials. By selecting the appropriate type of filler, manufacturers can tailor polymers to meet the specific demands of a wide variety of applications. As technology and materials science continue to advance, the use of fillers in polymers will likely expand, leading to the development of even more efficient and innovative material solutions. This symbiotic relationship between fillers and polymers exemplifies the ongoing evolution of materials design, driven by the need for performance and sustainability in an ever-changing market.