Stabilizers in Polymers Enhancing Durability and Performance
Polymers have permeated countless aspects of modern life, serving as essential materials in applications ranging from packaging to automotive components. However, their inherent vulnerabilities to environmental factors such as heat, light, and oxygen can lead to degradation over time, affecting their performance and usability. This is where stabilizers come into play. Stabilizers are additives that enhance the lifespan and functionality of polymer materials, making them critical for both manufacturers and end-users.
Types of Stabilizers
Stabilizers can be broadly categorized into several types based on their specific functions. The most common types include heat stabilizers, UV stabilizers, antioxidant stabilizers, and processing stabilizers.
1. Heat Stabilizers Many polymers face thermal degradation during processing and application. Heat stabilizers, such as metallic soaps and organic phosphites, are incorporated into polymer formulations to prevent changes in color and structural integrity when exposed to high temperatures. They are particularly important in applications involving high thermal stress, such as electrical cables and automotive parts.
2. UV Stabilizers Ultraviolet (UV) radiation can cause significant damage to polymers, leading to discoloration, loss of mechanical properties, and brittleness. UV stabilizers, including benzotriazole and hindered amine light stabilizers (HALS), absorb or reflect harmful UV rays, thus extending the life of materials used in outdoor applications, like garden furniture and roofing membranes.
3. Antioxidant Stabilizers Oxidation is another major cause of polymer degradation. Antioxidants, such as phenolic compounds and phosphites, are used to prevent oxidative degradation by neutralizing free radicals formed during environmental exposure. This is crucial for maintaining the physical properties of polymers, especially in products intended for long-term use.
stabilizers in polymers
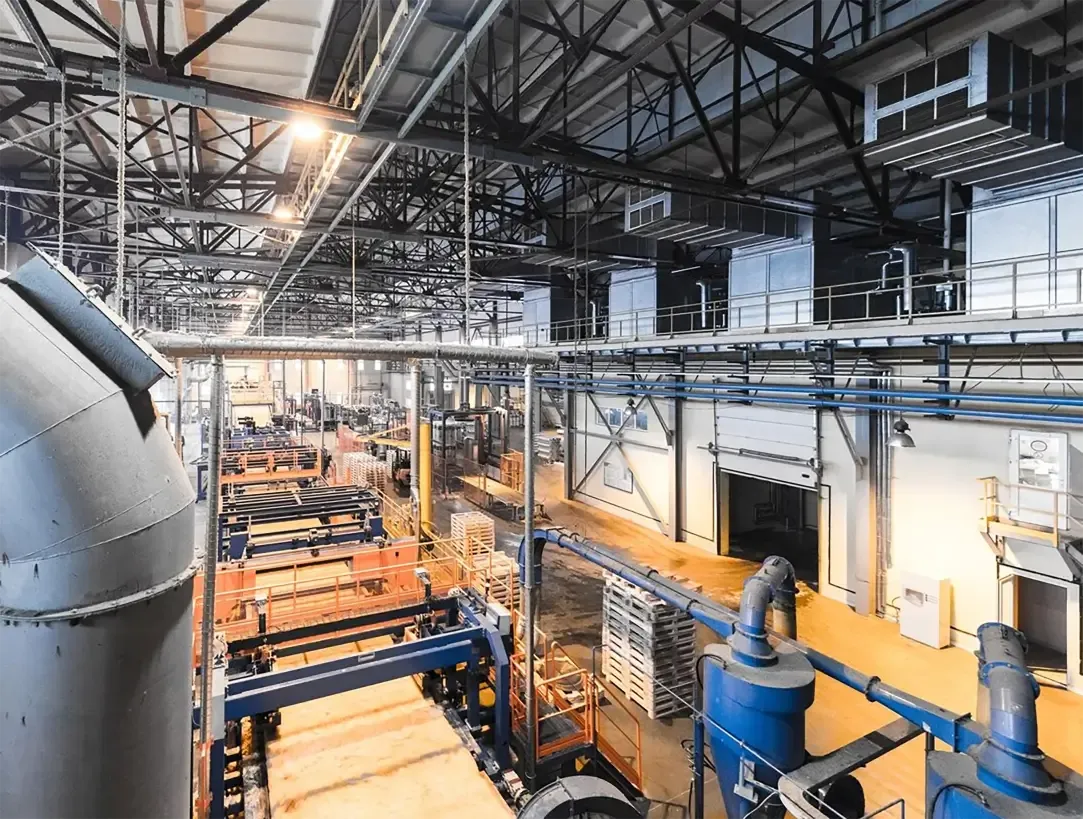
4. Processing Stabilizers During the manufacturing process, polymers are subjected to mechanical and thermal stresses that can lead to degradation. Processing stabilizers, such as silicone-based additives, improve the flow and processing characteristics of polymers, ensuring that they maintain their integrity throughout production.
Importance in Application
Incorporating stabilizers into polymer formulations is not just beneficial; it is often essential for specific applications. For instance, automotive manufacturers rely heavily on heat and UV stabilizers to ensure that components will withstand extreme conditions without failing prematurely. Similarly, the packaging industry utilizes various stabilizers to enhance the shelf life of products, protecting them from environmental factors that could compromise quality.
Moreover, as the demand for more sustainable and environmentally-friendly materials grows, the role of stabilizers in facilitating the use of recycled polymers becomes increasingly important. Stabilizers can help overcome the limitations often associated with recycled materials, such as lower mechanical properties and color variations, enabling manufacturers to produce high-quality products that meet regulatory and consumer demands.
Conclusion
The inclusion of stabilizers in polymers is a vital aspect of material science that significantly enhances the durability, performance, and longevity of polymeric products. By selecting the appropriate type of stabilizer for specific applications, manufacturers can address the challenges posed by environmental factors and ensure that their products remain reliable and efficient over time. As technology advances and sustainability becomes a more pressing concern, the development of new and improved stabilizers will continue to play a crucial role in the evolution of polymer materials, paving the way for more resilient and sustainable applications in the future.