The Importance of Laser Marking Additives for Plastics
In the rapidly evolving world of manufacturing and branding, the need for effective and innovative marking solutions has become paramount. Laser marking has emerged as one of the most efficient methods for creating durable, high-quality marks on various materials, particularly plastics. However, the complexity of marking different types of plastics necessitates the integration of laser marking additives.
Understanding Laser Marking
Laser marking involves using focused laser beams to create marks on the surface of materials. This technology is widely appreciated for its precision and permanence. Unlike traditional printing methods, laser marking does not require inks or solvents, making it an environmentally friendly solution. Moreover, the marks created by lasers are typically resistant to wear and tear, ensuring that branding and product information remain intact over time.
The Role of Additives in Laser Marking
Despite its advantages, marking certain plastic substrates can be challenging due to their properties. This is where laser marking additives play a crucial role. These additives are materials incorporated into the plastic formulation to enhance the laser marking process. They help in improving contrast, ensuring better visibility and definition of the mark upon laser treatment.
There are various types of additives that can be utilized in this process, including colorants, foaming agents, and specific laser-absorbing compounds. For instance, certain colorants can absorb the laser energy effectively, leading to a clearer and more vivid mark. Foaming agents can create a contrasting background by generating bubbles when exposed to the laser, helping the marking stand out even more.
Types of Laser Marking Additives
1. Colorants These are one of the most commonly used additives. They come in various forms, including pigments and dyes. When exposed to laser energy, these colorants can change in color or depth, providing a striking contrast against the plastic surface.
laser marking additives for plastics
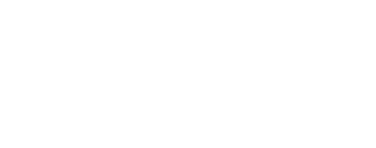
2. Thermal Additives These additives are designed to modify the thermal properties of plastics. They help in controlling the heat distribution during the marking process, ensuring that the material does not deform while achieving a high-quality mark.
3. Blowing Agents These are used to create a foam effect by generating gas during the laser marking process. This not only enhances the aesthetic appeal of the mark but also improves its readability.
4. Laser-Durable Compounds These additives are specifically designed to enhance the durability of the marks created by laser technologies. They ensure that the markings can withstand environmental factors such as UV exposure and abrasion.
Applications and Benefits
The applications for laser marking additives in plastics are vast, spanning industries such as packaging, automotive, medical, and electronics. In the packaging industry, for example, laser marking is utilized for product identification, expiration dates, and barcodes. In the automotive sector, it ensures traceability and compliance with regulations.
The benefits of using laser marking additives extend beyond mere aesthetics. They enhance production efficiency, reduce waste, and promote sustainability by eliminating the need for additional inks and solvents. Furthermore, the permanent nature of laser markings helps companies in maintaining their branding integrity.
Conclusion
In summary, laser marking additives for plastics are essential for achieving high-quality, durable, and visually appealing marks. As industries increasingly recognize the benefits of laser technology, the demand for effective marking solutions will continue to rise. By integrating appropriate additives into plastic formulations, manufacturers can ensure that their products not only meet regulatory requirements but also stand out in a competitive marketplace.