Plastic Additives and Compounding Enhancing Polymer Performance
In the realm of materials science, plastics have emerged as a cornerstone of modern manufacturing and consumer products. However, to meet the diverse demands of various applications, the raw polymers used in plastics often require enhancements through the incorporation of additives. These additives are crucial in modifying the properties of plastics, improving their performance, and prolonging their usability.
Understanding Plastic Additives
Plastic additives are substances added to polymers during the manufacturing process to impart specific characteristics or improve performance. These additives can be classified into several categories
1. Stabilizers These additives protect the plastic from degradation caused by heat, light, or environmental conditions. Heat stabilizers prevent degradation during processing, while UV stabilizers protect against sun exposure, which can cause discoloration and brittleness.
2. Plasticizers These substances are added to increase the flexibility and workability of plastics, especially in polyvinyl chloride (PVC). Plasticizers lower the glass transition temperature of the polymer, enabling it to bend and mold more easily without cracking.
3. Fillers Fillers, such as calcium carbonate or talc, are used to increase the volume and improve the mechanical properties of plastics. They can enhance strength, reduce costs, and modify other properties such as thermal conductivity and electrical insulation.
4. Flame Retardants Safety is a primary concern in many applications, and flame retardants are key additives that help reduce flammability. These substances can be inorganic or organic and are designed to slow down the spread of fire.
plastic additives and compounding
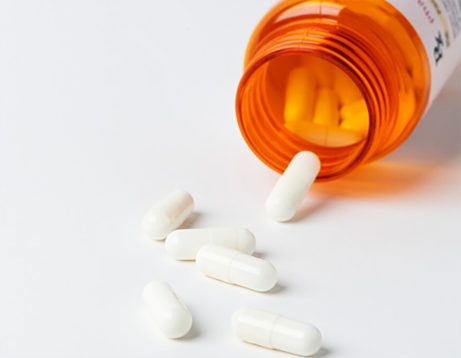
5. Colorants Colorants, including pigments and dyes, are used to impart color to plastics. This not only enhances aesthetic appeal but can also play a functional role in applications like safety equipment, where color coding is vital.
Compounding Process
The process of compounding involves combining the base resin with various additives to produce a plastic material with desired properties. This is typically done using specialized equipment such as twin-screw extruders, which ensure thorough mixing and uniform dispersion of additives throughout the polymer matrix.
During compounding, factors such as temperature, shear rate, and residence time must be carefully controlled to achieve the desired characteristics while avoiding thermal degradation of the polymer or loss of additive effectiveness. The final compounded material can then be processed into various shapes and products through methods like injection molding, blow molding, or extrusion.
The Importance of Additives in Plastics
The role of additives in plastics cannot be overstated. They enable manufacturers to tailor material properties to meet specific performance standards required by different industries—from automotive and aerospace to packaging and consumer goods. The versatility afforded by additives allows for innovations that lead to lightweight, durable, and high-performance materials.
Conclusion
As the demand for advanced plastic materials continues to grow, the importance of plastic additives and compounding becomes ever more significant. By carefully selecting and incorporating various additives, manufacturers can enhance the functionality and lifespan of plastic products, ensuring they meet the needs of a rapidly evolving market. With ongoing research and development in the area of additives, the future of plastics looks promising, paving the way for sustainable solutions and enhanced material performance.