The Role of Plastic Fillers in Modern Manufacturing
Plastic fillers are essential materials in the manufacturing and processing of plastics, serving to enhance the properties of polymer products while reducing costs. Fillers can vary widely in composition and characteristics, including organic materials like wood flour, inorganic substances like calcium carbonate, and synthetic compounds. These fillers are incorporated into plastic formulations to modify aspects such as rigidity, strength, density, thermal resistance, and impact resistance.
Types of Fillers
One of the primary classifications of plastic fillers is based on their origin natural and synthetic. Natural fillers include materials like wood flour, cotton, and various minerals, while synthetic fillers are engineered substances such as glass fibers, carbon black, and various silicates. Each type of filler offers distinct advantages, making them suitable for different applications.
- Calcium Carbonate A popular choice due to its low cost and excellent compatibility with various polymers, calcium carbonate is used not only to reduce expense but also to improve rigidity. Its excellent physical constants help maintain the integrity of the plastic while enhancing its thermal stability.
- Talc This mineral filler is known for its ability to improve the tensile strength and thermal stability of polymers. It also provides a smooth surface finish, making it ideal for products like automotive components and consumer electronics.
- Glass Fibers Glass fibers offer significant strength improvements, especially in thermosetting plastics. They are used in applications that require high rigidity and mechanical strength, such as in the automotive and aerospace industries.
Benefits of Using Fillers
The incorporation of fillers into plastic materials can yield several benefits
plastic fillers
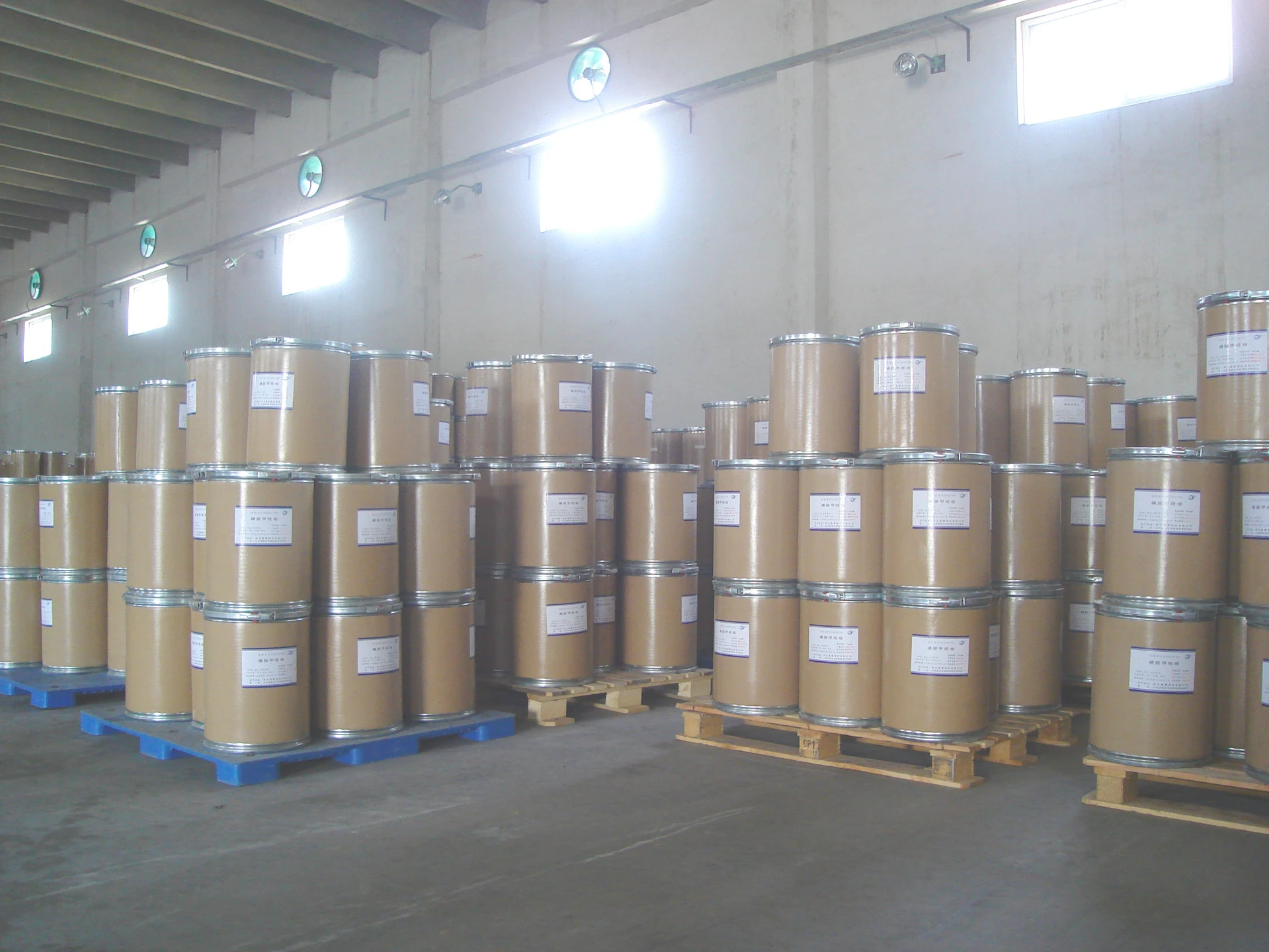
1. Cost Reduction By substituting a portion of the polymer matrix with inexpensive fillers, manufacturers can significantly reduce production costs without compromising product performance.
2. Enhanced Mechanical Properties Fillers can increase the strength, stiffness, and impact resistance of plastics, making them suitable for a broader range of applications. For instance, filled polymers often demonstrate improved dimensional stability under stress.
3. Improved Processability Fillers can enhance the flow properties of plastic materials during processing, leading to more efficient manufacturing processes. This can result in shorter cycle times and improved overall productivity.
4. Customization of Physical Properties Different fillers allow for the customization of properties such as thermal resistance, electrical conductivity, and moisture barriers. This versatility enables manufacturers to tailor products to specific end-use requirements.
Environmental Considerations
While fillers offer various benefits, the environmental impact of plastic fillers is becoming a critical concern. Many fillers are derived from non-renewable sources or require significant energy for extraction and processing. Furthermore, the use of certain fillers can affect the recyclability of plastic products.
The increasing emphasis on sustainable practices in manufacturing is prompting researchers to explore bio-based fillers as alternatives. Natural fibers, such as hemp, kenaf, and flax, are gaining traction due to their renewable nature and lower environmental footprint. By integrating these bio-based fillers, manufacturers can produce environmentally friendly composites with desirable mechanical properties.
Conclusion
In summary, plastic fillers play a crucial role in the modern manufacturing landscape, providing significant enhancements in product performance and cost efficiency. Their ability to improve mechanical properties, processability, and customization options makes them valuable in a wide array of applications. However, the industry must also address the environmental challenges linked to traditional fillers and explore sustainable alternatives. As technology advances, the development of more eco-friendly fillers may pave the way for a greener future in the plastic manufacturing sector. This will not only benefit manufacturers but also contribute positively to environmental sustainability and resource conservation.