Understanding PPQ and Q10 Key Concepts in Quality Management
In today's manufacturing and business environment, maintaining high standards of quality is paramount for success. Two critical frameworks that assist organizations in achieving this are Production Part Approval Process (PPAP) and the concept of Q10, which refers to the Quality Management system in organizations. Together, they provide a robust structure for ensuring that products meet required specifications and customer expectations.
What is PPAP?
The Production Part Approval Process (PPAP) is a standardized method used in the automotive and manufacturing industries to demonstrate that the manufacturer understands the requirements and is capable of producing parts that meet those requirements. Typically used when introducing new products or processes, PPAP ensures that all engineering design specifications and customer requirements are met before mass production begins.
The PPAP process includes several key components design records, engineering changes, customer engineering approval, planning, and product specifications. These documents form the basis of the approval process and ensure a collaborative approach between suppliers and customers. By adhering to PPAP, companies can reduce the chances of defects and enhance product reliability, ultimately resulting in higher customer satisfaction.
Introducing Q10
On the other hand, Q10 is a concept that pertains to the total quality management of an organization. It goes beyond just manufacturing processes; it encompasses all aspects of a business, including design, production, distribution, and customer service. The Q10 framework emphasizes the importance of quality control and continuous improvement across all operations.
ppq q10
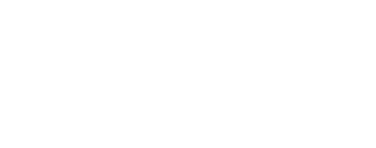
The principle behind Q10 is simple quality is everyone’s responsibility. Every employee, from top management to frontline workers, plays an essential role in ensuring that quality standards are met. This participatory approach not only fosters a culture of quality within the organization but also leads to improved efficiency and reduced costs. By integrating Q10 into their daily operations, businesses can cultivate a mindset focused on quality, leading to long-term success.
The Interconnection between PPAP and Q10
The interplay between PPAP and Q10 is critical for organizations striving for excellence. While PPAP focuses primarily on the approval process for production parts, Q10 provides a broader quality management perspective that helps organizations implement and sustain quality initiatives.
By incorporating Q10 principles into the PPAP process, companies can enhance their product development strategies. For instance, utilizing Q10’s continuous improvement philosophy during the PPAP can identify potential issues earlier in the production process, which in turn may lead to quicker resolutions and less waste. This combination ensures that all products not only meet initial specifications but also align with the overarching goals of product quality and customer satisfaction.
Conclusion
In conclusion, PPAP and Q10 serve as foundational pillars in the landscape of quality management. PPAP offers a structured approach to validating the quality of production parts, while Q10 fosters a culture of quality throughout the organization. By understanding and effectively utilizing these frameworks, organizations can significantly improve their product quality and enhance customer satisfaction. As the business environment continues to evolve, the integration of these concepts will remain critical for manufacturers and service providers aiming for long-term success and competitiveness in the market.