The Impact of Talc as an Additive in Plastic Manufacturing
In recent years, the use of talc as an additive in plastic production has garnered significant attention within the materials science community. Talc, a naturally occurring mineral composed primarily of magnesium, silicon, and oxygen, serves a variety of functions in enhancing the properties of plastics. Its unique characteristics make it an ideal additive in various plastic formulations, particularly in the production of polypropylene (PP) and polyethylene (PE) composites.
Talc's primary role in plastic manufacturing is to improve stiffness and dimensional stability. When added to polypropylene, for example, talc increases the material's rigidity without adding significant weight. This characteristic makes talc-filled polypropylene particularly suitable for applications requiring high performance under load, such as automotive parts, household appliances, and industrial containers. The enhancement in stiffness allows manufacturers to produce thinner, lighter parts while still maintaining structural integrity, subsequently leading to weight reduction in overall products.
The Impact of Talc as an Additive in Plastic Manufacturing
Talc also contributes to the thermal and dimensional stability of plastics. By lowering the thermal expansion coefficient, talc helps in minimizing warping and deformation of plastic components under varying temperature conditions. This reliability is vital in applications where precision is key, such as in electronic housings and automotive components. Furthermore, the addition of talc enhances the thermal resistance of plastics, allowing them to withstand higher service temperatures without losing mechanical properties.
talc additive plastic
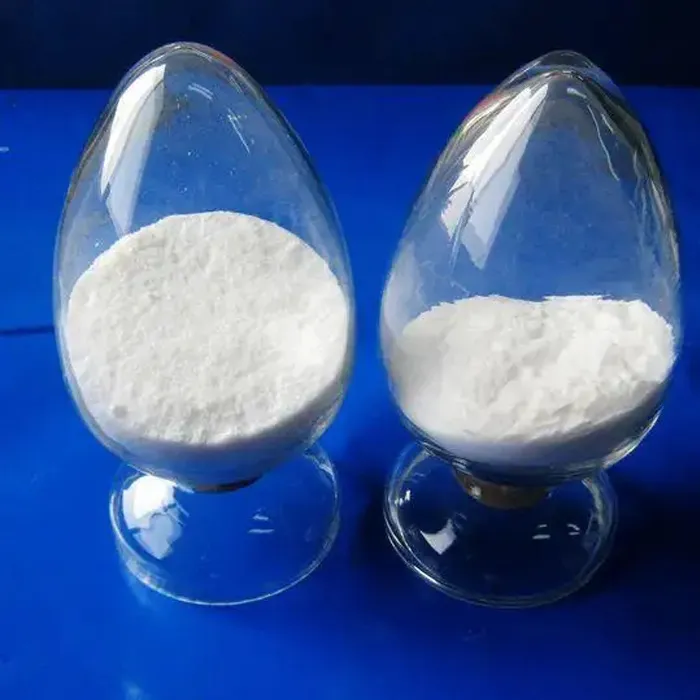
In addition to its mechanical and thermal benefits, talc can influence the aesthetic properties of plastics. It provides a matte finish that can enhance the visual appeal of products, making them suitable for consumer markets where appearance is a significant factor. Talc-filled plastics can achieve a balance between functionality and aesthetics, meeting the demands of various industries, from consumer goods to packaging.
However, the use of talc as a plastic additive is not without its challenges and controversies. Environmental concerns related to the mining and processing of talc have led to scrutiny regarding the sustainability of its use. Companies are increasingly being called upon to demonstrate responsible sourcing and processing of raw materials. As such, there is a growing trend towards integrating talc sourced from environmentally sustainable operations. Moreover, the health implications of talc, particularly in relation to its association with certain health risks when inhaled in dust form, have raised awareness and led to rigorous safety regulations in manufacturing processes.
The evolving landscape of plastic production necessitates a consideration of alternative additives that can mimic the performance-enhancing attributes of talc. Research is ongoing to identify synthetic alternatives that offer similar benefits without the environmental and health concerns associated with talc. These alternatives may offer new formulations that leverage the desired properties of talc while promoting sustainability and safety.
In conclusion, talc remains a vital additive in the field of plastic manufacturing due to its ability to enhance stiffness, improve processing efficiency, and contribute to dimensional stability. While challenges exist in terms of environmental sustainability and health considerations, ongoing research and development efforts aim to address these issues, ensuring that talc can continue to play an essential role in the evolution of plastic materials. As the industry continues to innovate, the future of talc in plastic production hinges on the balance between performance benefits and sustainable practices, marking an exciting era for materials engineering and design.