The Role of Talc as an Additive in Plastics
Talc, a naturally occurring mineral composed mainly of magnesium silicate, is widely recognized for its unique physical and chemical properties. It has been utilized for centuries in various applications ranging from cosmetics to ceramics. In recent years, however, talc has gained significant importance as an additive in the plastics industry. This article explores the various roles that talc plays in enhancing the properties and performance of plastic materials.
Improving Mechanical Properties
One of the most notable benefits of incorporating talc into plastics is the improvement of mechanical properties. Talc acts as a reinforcing agent, providing increased stiffness and strength to plastic composites. It enhances tensile strength, impact resistance, and rigidity, making it particularly beneficial for high-performance applications. For example, talc-filled polypropylene is commonly used in automotive parts, household items, and packaging due to its superior strength-to-weight ratio.
Enhancing Thermal Stability
Talc also contributes to the thermal stability of plastics. When added to polymer matrices, talc can help improve the heat resistance of the final product. This is especially important in applications that involve exposure to elevated temperatures, such as automotive under-the-hood components or electrical housings. Talc’s ability to absorb heat and reduce thermal expansion makes it an ideal additive for such demanding environments.
Improving Processing and Molding Characteristics
Another significant advantage of using talc in plastics is its impact on processing and molding characteristics. Talc serves as a slip agent, improving the flow of the material during processing and enhancing the moldability of the finished product. This results in faster production cycles and reduces the occurrence of defects during manufacturing. The use of talc can also decrease the viscosity of molten plastics, making them easier to handle and shape.
talc additive plastic
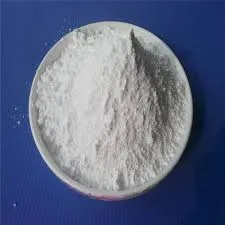
Reducing Production Costs
Incorporating talc as an additive can also lead to cost savings in the production of plastic materials. Talc is relatively inexpensive compared to other fillers and additives, making it an economical choice for manufacturers. Additionally, by increasing the volume of the product without significantly compromising mechanical properties, talc allows companies to reduce the amount of more expensive raw materials, thus lowering overall production costs.
Influencing Surface Properties
Talc can also influence the surface properties of plastics. By modifying the surface texture and finish, it can enhance aesthetic qualities such as gloss and smoothness. Furthermore, talc can improve the scratch and abrasion resistance of plastic components, making them more durable and suitable for applications where wear and tear are common.
Environmental Considerations
As the demand for sustainable materials continues to grow, the use of talc in plastics aligns with environmental considerations. Talc is a naturally derived, non-toxic mineral, which makes it an attractive option for manufacturers aiming to produce eco-friendly products. Moreover, talc can help reduce the overall carbon footprint of plastic manufacturing by improving material efficiency and reducing waste.
Conclusion
In conclusion, talc plays a vital role as an additive in the plastics industry, enhancing mechanical properties, thermal stability, and processing characteristics. Its cost-effectiveness and environmentally friendly nature further contribute to its growing popularity among manufacturers. As technology advances, the use of talc in various plastic applications is expected to increase, offering innovative solutions to meet the demands of modern industry. With its multifaceted benefits, talc continues to be an indispensable component in the development of high-performance plastic materials.