- Introduction to What Chemical is Used for Water Treatment
- Key Types of Chemicals Used for Treatment of Water
- Technical Advantages and Performance Metrics
- Chemical Products for Boiler Water Treatment
- Manufacturer Comparisons: Performance and Cost
- Customized Water Treatment Chemical Solutions
- Case Studies: Application of What Chemical is Used for Water Treatment
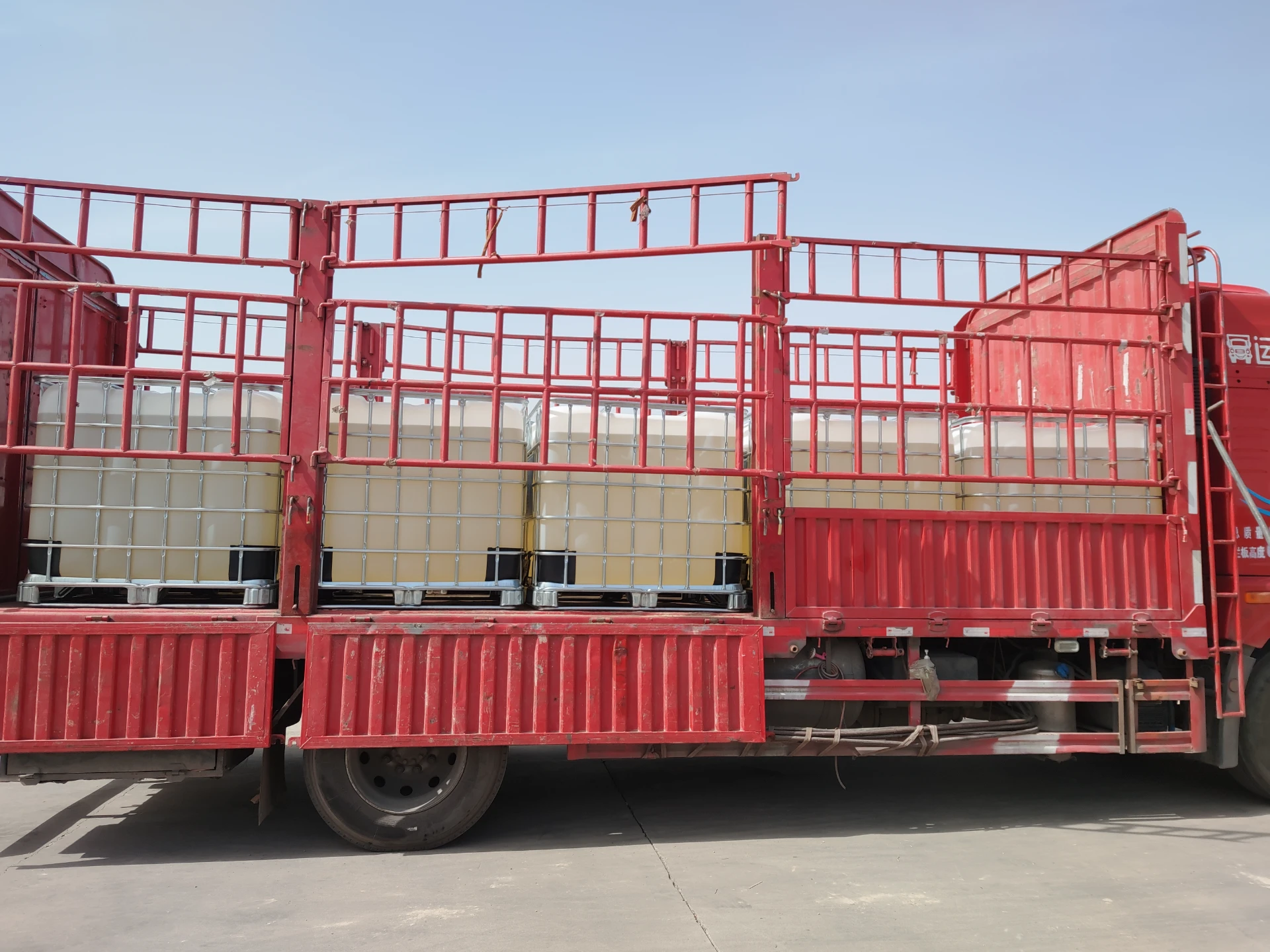
(what chemical is used for water treatment)
Introduction to What Chemical is Used for Water Treatment
The growing need for clean and safe water has led to advanced water treatment technologies globally. Understanding what chemical is used for water treatment
is crucial for businesses, municipalities, and industries aiming to meet regulatory standards and ensure public health. Water treatment employs specific chemicals to remove contaminants, neutralize harmful substances, and improve quality. From municipal drinking water systems to industrial applications, these chemicals are the backbone of efficient purification processes, directly impacting quality, safety, and sustainability.
Key Types of Chemicals Used for Treatment of Water
The selection of chemicals used for treatment of water depends on the water's origin, intended application, and target contaminants. The most widely utilized chemicals include:
- Coagulants and Flocculants: Alum, ferric chloride, and polyaluminum chloride facilitate the aggregation and removal of suspended solids through coagulation and flocculation processes.
- Chlorine and Chlorine Compounds: Sodium hypochlorite and chlorine dioxide are primary disinfectants for killing pathogenic organisms.
- Oxidizing Agents: Potassium permanganate and hydrogen peroxide oxidize iron, manganese, and organic contaminants.
- pH Adjusters: Lime, sodium hydroxide, and sulfuric acid manage water pH for corrosion control and process optimization.
- Antiscalants and Corrosion Inhibitors: Polyphosphates and organophosphonates prevent mineral scaling and equipment degradation.
- Activated Carbon: Used to adsorb organic compounds and remove taste, odor, and chemical pollutants.
Technical Advantages and Performance Metrics
The effectiveness of a chemical used for treatment of water is measured by several performance metrics:
- Contaminant Removal Efficiency: State-of-the-art coagulants such as polyaluminum chloride (PAC) outperform traditional alum, achieving up to 97% removal of turbidity compared to 92% for alum, according to a 2022 industry survey.
- Disinfectant Residual Stability: Modern stabilized chlorine dioxide provides a stable residual for up to 48 hours, compared to only 12-24 hours for standard sodium hypochlorite.
- Dosing Accuracy and Process Integration: Automated dosing systems paired with advanced chemicals can reduce overdosing by up to 20%, saving costs and reducing by-product formation.
- Environmental Impact: New generation antiscalants are biodegradable and non-toxic, resulting in lower aquatic toxicity scores (<2 mg/L LC50 for Daphnia magna).
Chemical Products for Boiler Water Treatment
Industrial boilers present unique water treatment demands requiring specialized chemicals to prevent corrosion, scale buildup, and microbiological fouling:
- Oxygen Scavengers: Deaerators may remove oxygen mechanically, but chemicals like sodium sulfite and hydrazine are essential for eliminating residual dissolved oxygen, inhibiting corrosion.
- Phosphate-Based Scale Inhibitors: These manage deposited minerals like calcium carbonate by keeping them in solution and preventing hard scale formation.
- Alkalinity Builders: Chemicals such as sodium hydroxide and trisodium phosphate raise pH and optimal alkalinity for minimizing acidic condensate attack.
- Condensate Line Protectants: Neutralizing amines such as cyclohexylamine guard against corrosion in steam return lines.
Manufacturer Comparisons: Performance and Cost
A critical analysis of leading water treatment chemical manufacturers reveals distinct differences in product efficiency, cost, and sustainability credentials. The following table summarizes a comparative analysis based on 2023 third-party evaluations:
Manufacturer | Key Product | Turbidity Removal (%) | Cost (USD/ton) | Biodegradability (%) | Global Market Share (%) |
---|---|---|---|---|---|
SNF Group | Flopam Flocculant | 93 | 1,200 | 95 | 23 |
Kemira | Superfloc A130 | 96 | 1,250 | 91 | 18 |
BASF | Magnafloc LT27 | 97 | 1,320 | 94 | 15 |
Solvay | Hydrex 6000 Series | 92 | 1,100 | 92 | 11 |
Kurita Water | Kuriflock PA | 95 | 1,340 | 96 | 6 |
Choosing the right supplier involves balancing removal performance, cost per treated volume, product availability, and sustainability profile. While higher performance is key for stringent requirements, operational cost and environmental factors increasingly drive purchase decisions.
Customized Water Treatment Chemical Solutions
No single chemical or standard treatment approach delivers optimal results for every water source or industry. Providers now offer tailor-made chemical packages aligned with customers’ water profiles and process goals. A typical customization workflow includes:
- Comprehensive Water Analysis: Advanced analytical testing determines targeted contaminants, pH, alkalinity, and microbial loads.
- Simulation and Jar Testing: Laboratory-scale experiments confirm the best coagulant or flocculant blends, dosing ranges, and expected results.
- Smart Dosing Integration: Digital controllers and real-time monitoring systems regulate chemical dosing, responding dynamically to water quality fluctuations — yielding up to 12% chemical savings compared to manual schemes.
- Performance Auditing: Ongoing monitoring and adjustment optimize cost, ensure compliance, and extend equipment lifespans.
Case Studies: Application of What Chemical is Used for Water Treatment
Demonstrating real-world success, the deployment of appropriate chemical solutions underpins high-performance water treatment systems across various sectors:
1. Municipal Drinking Water—Urban Facility, Southeast Asia
To achieve a 99.99% reduction in Escherichia coli, the city’s utility introduced a chlorine dioxide generator system. Chlorine dioxide dosage was reduced by 18% over previous sodium hypochlorite dosing, while achieving superior taste and odor control. Daily monitoring showed disinfection by-products (DBPs) decreased by 27%, supporting regulatory compliance.
2. Textile Industry—Boiler Water Treatment, Eastern Europe
A leading textile manufacturer faced recurring boiler scale and corrosion, impacting productivity and maintenance costs. By switching to a Kurita-blend antiscalant and oxygen scavenger, scale formation dropped by 91%, with dissolved oxygen levels reduced to below 0.007 mg/L. This extended maintenance intervals from every 6 months to yearly, cutting operating expenses by $44,000 annually.
3. Pharmaceutical Production—Ultrapure Water, North America
This facility used a tailored package of coagulant, activated carbon, and membrane-compatible antiscalant, keeping endotoxin levels below 0.25 EU/mL and producing water suitable for injection (WFI). Smart dosing achieved chemical consumption reduction by 14% compared to baseline.
These case studies exemplify how precision selection, application, and monitoring of what chemical is used for water treatment delivers tangible quality, compliance, and cost-saving outcomes across diverse industries.
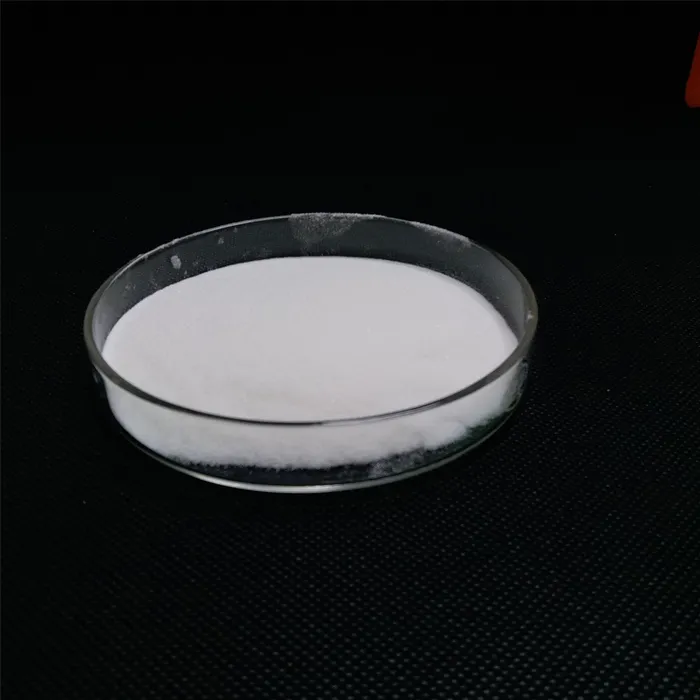
(what chemical is used for water treatment)