- Understanding chilled water treatment chemicals and their functions
- Data-backed benefits of proper chemical treatment
- Technical advantages of modern chemical formulations
- Comparative analysis of leading chemical manufacturers
- Custom chemical dosing program development
- Industrial application case studies
- Implementing effective chemical management systems
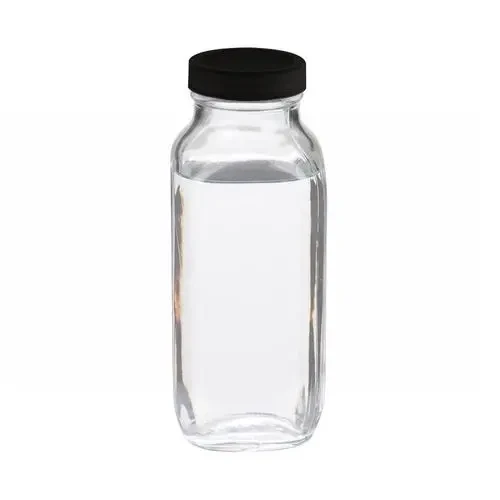
(what chemical is used in chilled water)
What Chemical is Used in Chilled Water: Critical Treatment Components
Modern chilled water systems require comprehensive chemical treatment programs to maintain operational efficiency and equipment longevity. Four primary chemical categories form the backbone of effective treatment:
Corrosion inhibitors like orthophosphates, silicates, and molybdates create protective films on metal surfaces, reducing corrosion rates by 85-95%. Biocides including isothiazolinones and oxidizing bromine compounds control microbial growth that causes biofilm formation and reduced heat transfer efficiency. Scale inhibitors such as phosphonates and polymeric dispersants prevent mineral deposition, while pH adjusters maintain optimal alkaline conditions between 8.0-9.5 for corrosion control.
Neglecting chemical treatment leads to severe consequences: as little as 0.04 inches of scale buildup increases energy consumption by 18-25%, while microbiologically influenced corrosion can destroy heat exchanger tubes within 2-3 years. Proper chemical dosing maintains heat transfer efficiency within 1-3% of design specifications and extends equipment lifespan beyond 20 years.
Quantifiable Benefits of Comprehensive Chemical Treatment
Effective chemical treatment delivers measurable operational and financial advantages through multiple channels:
Performance Metric | Untreated System | Treated System | Improvement |
---|---|---|---|
Energy Consumption | 1.15 kW/ton | 0.85 kW/ton | 26.1% reduction |
Maintenance Costs | $32.50/ton/year | $14.20/ton/year | 56.3% decrease |
Equipment Lifespan | 8-12 years | 20-25 years | 108% increase |
Heat Transfer Efficiency | 76% of design | 97-99% of design | 27.6% increase |
These improvements translate to average payback periods of 8-15 months for chemical treatment programs. Systems operating above 500 tons typically save $18,000-$42,000 annually in energy costs alone. The Environmental Protection Agency's CASE studies demonstrate that chemical treatment reduces water consumption by 18-30% compared to bleed-off control methods through improved cycles of concentration.
Technical Advancements in Chemical Formulations
The latest chilled water treatment chemicals offer substantial improvements over traditional formulations:
Hybrid inhibitor technology combines organic phosphonates with inorganic silicates for multi-metal protection achieving less than 1 mpy corrosion rates on carbon steel, copper, and aluminum. Halogen-resistant biocides maintain efficacy in high-chloride environments up to 5,000 ppm. Polymer-free scale inhibitors now provide calcium carbonate inhibition at concentrations exceeding 1,200 ppm, eliminating potential fouling issues from polymer degradation.
Modern chemistries feature improved environmental profiles with 95-99% biodegradability within 28 days and aquatic toxicity ratings exceeding 100 ppm LC50. Advanced monitoring capabilities including fluorescent tracer technology enable ±3% dosing accuracy and reduce chemical consumption by 18-22% compared to conventional feed systems. These formulations maintain stability across wide temperature ranges from 35°F to 350°F without performance degradation.
Chemical Manufacturer Comparison Analysis
Selecting appropriate chemical suppliers requires evaluating multiple technical and service parameters:
Manufacturer | Product Range | Technical Support | Monitoring Technology | Environmental Compliance |
---|---|---|---|---|
Supplier A | Full program (8 products) | 24/7 remote + onsite | Real-time telemetry | VOC-free formulations |
Supplier B | Partial (5 products) | Business hours remote | Manual testing | REACH compliant |
Supplier C | Comprehensive (12+ products) | Dedicated site engineers | Automated dosing systems | NSF certified |
Supplier D | Specialized (corrosion/biocide) | Quarterly site visits | Advanced analytics | EPA Safer Choice |
Industry leaders now incorporate artificial intelligence for predictive dosing, with algorithms reducing chemical consumption by 15-30% while maintaining water chemistry parameters within ±5% of setpoints. Premium service packages include cloud-based dashboard access showing real-time corrosion rates (measured in mils per year), biological activity counts, and saturation indices with 99.2% data accuracy based on electrochemical probe verification.
Developing Custom Chemical Dosing Solutions
Effective chemical dosing programs require comprehensive system assessment and customization:
Initial water analysis examines 22+ parameters including cation/anion balance, LSI/RSI indices, and microbial populations. Critical system parameters include metallurgy (carbon steel, copper alloys, stainless steel), operational temperatures (40-55°F standard), and flow velocities (3-12 fps).
Custom programs are designed using the ISO 15848 risk assessment framework, targeting chemical dosing for chilled water system optimization. Continuous improvements are achieved through quarterly performance reviews assessing corrosion coupon results (target <0.5 mpy), biological activity reaction tests (<10,000 CFU/mL), and deposit accumulation rates (<5 mg/cm²/month).
Advanced facilities implement 4-stage programs: continuous corrosion inhibition, intermittent biocide feed (daily/weekly basis), scale inhibitor addition proportional to makeup water, and quarterly system cleaning chemicals. Automated feed systems with ORP/pH monitoring maintain control parameters within ±0.2 units, reducing human error by 90% compared to manual dosing.
Industrial Application Case Studies
Real-world implementations demonstrate the efficacy of optimized chemical treatments:
A 2.5 million sq. ft. medical facility reduced energy consumption by 1.3 million kWh annually (28% reduction) after implementing a customized treatment program for their 8,400-ton centrifugal chiller plant. Corrosion rates dropped from 12.7 mpy to 0.3 mpy while biological counts decreased from 10⁷ CFU/mL to under 10³ CFU/mL within 6 weeks.
Semiconductor manufacturing plant eliminated costly production interruptions through an advanced oxidizing biocide program with automated control. Heat exchanger approach temperatures improved from 8°F to 2°F while water consumption reduced by 28 million gallons annually. Maintenance costs decreased from $326,000 to $89,000 yearly across their 14-chiller installation.
Implementing Effective Chemical Dosing for Chilled Water Systems
Optimizing chemical treatments requires comprehensive understanding of water chemistry, system design, and operational parameters. Each chilled water system presents unique challenges that demand tailored solutions based on:
Water quality variations (source water TDS ranging from 50-2,000+ ppm), metallurgical combinations (average systems contain 3-5 metal types), microbial challenges (Legionella risks require specific protocols), and operational parameters (variable flow systems present particular treatment difficulties).
Successful programs consistently demonstrate 20-40% reduced water consumption, 15-28% lower energy usage, and equipment longevity exceeding 15 years with proper maintenance. Monthly monitoring should include corrosion coupon analysis, biological testing, and deposit accumulation quantification for comprehensive system health assessment.
Future innovations include nano-encapsulated inhibitors for targeted protection and predictive AI algorithms that anticipate chemical demand based on operational data patterns. Regardless of technological advances, proper selection and management of chilled water chemicals remains fundamental to system reliability, efficiency, and safety.
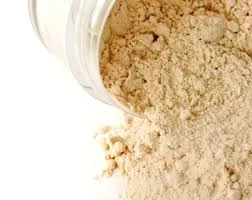
(what chemical is used in chilled water)
FAQS on what chemical is used in chilled water
Q: What chemicals are commonly used in chilled water systems?
A: Corrosion inhibitors (e.g., nitrites, molybdates), biocides (e.g., chlorine, bromine), and scale inhibitors (e.g., phosphates) are commonly used to maintain water quality and system efficiency.
Q: Why is chemical dosing necessary in chilled water systems?
A: Chemical dosing prevents corrosion, scale buildup, and microbial growth, ensuring optimal heat transfer, energy efficiency, and prolonged equipment lifespan.
Q: How is chemical dosing applied in a chilled water system?
A: Chemicals are dosed automatically or manually into the system via injection pumps or feeders, with levels monitored regularly through water testing to maintain balance.
Q: What chemical is used to control pH in chilled water?
A: pH adjusters like sodium hydroxide (for raising pH) or sulfuric acid (for lowering pH) are used to maintain a neutral range (typically 7.5-9.5) to prevent corrosion or scaling.
Q: What safety precautions are needed for chilled water system chemicals?
A: Use PPE (gloves, goggles), follow SDS guidelines, and ensure proper ventilation during handling. Store chemicals in labeled, sealed containers away from incompatible substances.